Turning pulper rope into a valuable resource
Pulper ropes are a by-product of waste paper recycling. The materials contained in a pulper rope can be partly recycled and partly thermally recovered – given the right technology.
An article in cooperation with: Waste Management World | https://waste-management-world.com
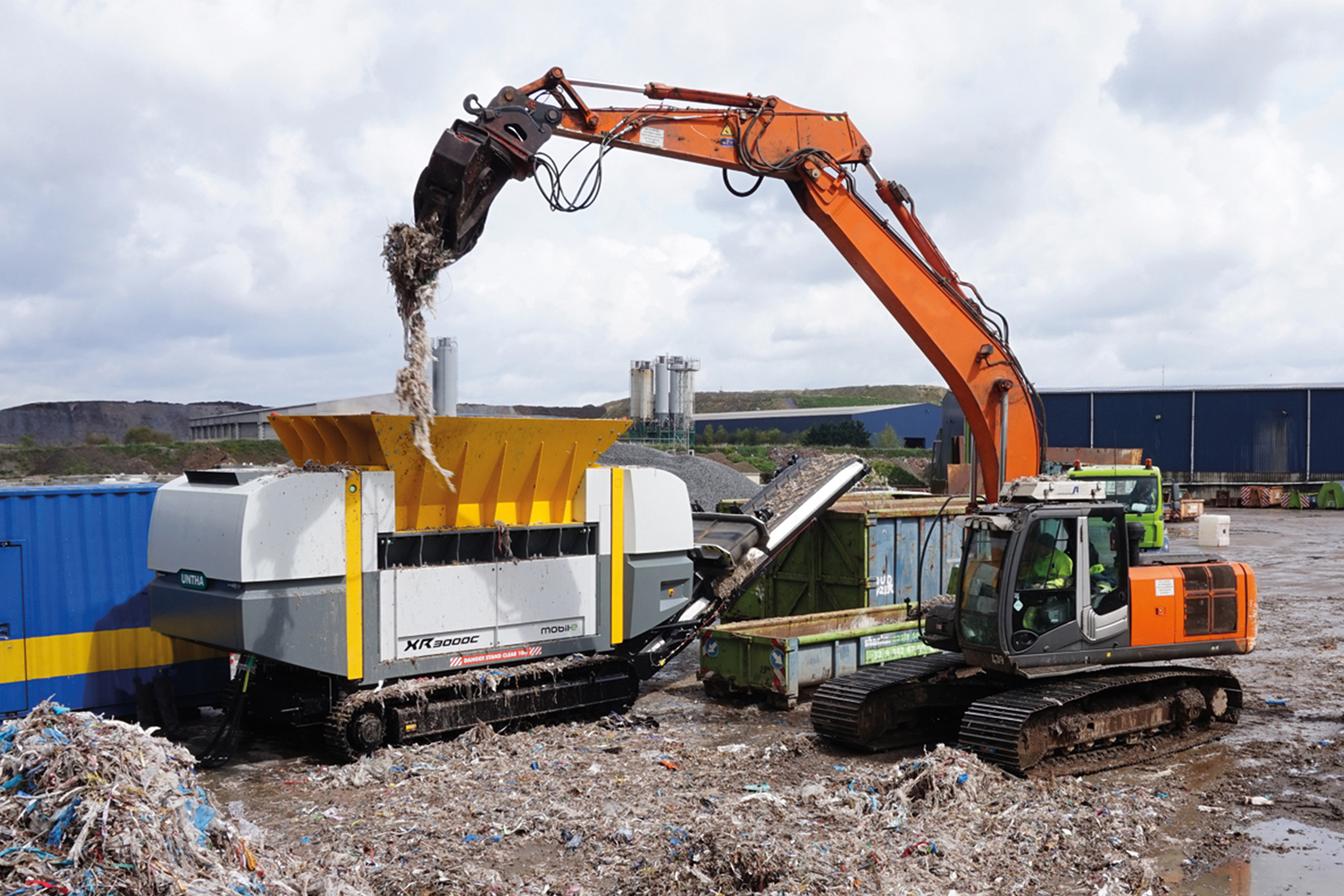
Founded in 1970 in Kuchl near Salzburg, Austria, where it is still headquartered, UNTHA offers high-quality shredders for a wide range of applications: from the recovery of valuable materials for recycling and the utilisation of residual and waste wood to the processing of waste for thermal and energy recovery. The shredders from the Austrian premium manufacturer are suitable for materials such as biological waste, electronic waste and particularly challenging materials such as tyres, mattresses and pulper ropes.
A valuable by-product
Pulper ropes are a by-product of waste paper recycling. In papermaking, waste paper, cardboard and new raw materials are dissolved and defibred with process water in machines known as pulpers. Unwanted contaminants such as wires, stickers, cords, foils, small pieces of wood and plastic or other insoluble papers also end up in the pulper. The reason for this high metal content is that waste paper is delivered in compressed bales. Wire and plastic strapping are used to keep them in shape.
In order to prevent these contaminants from becoming entangled during paper production and having to be removed at great expense, a catching device is used. In most cases, a long rope is lowered into the agitator vat, which hooks the wires and plastic parts together to form a pulper rope. This can then be removed using a pigtail winch. At regular intervals, the pulper braid is slowly and continuously pulled out of the vat, creating a metre-long braid.
Difficult to process…
The rope is long, heavy, flexible and wet. Each pulper rope is different in diameter, length and content and is difficult to process due to its composition and shape. But the ropes do contain a high-quality ferrous fraction that can be resold and recycled. And the core material, consisting of plastic wires and the like, is usually sent for thermal recycling and can be used on-site as an alternative fuel for the internal incineration process or used thermally in cement or power plants. This makes the most of these ‘waste’ materials.
…but not impossible
In addition to the varying composition and the fact that the material is wet, the pulper rope is difficult to catch in a shredder. UNTHA has solved all these problems with its XR series. “Many waste materials contain valuable materials and resources that can be used economically and ecologically. They just need to be processed correctly,” says Peter Streinik, UNTHA Head of Global Sales and Business Development – Recycling & Waste. “This is where our shredders make a valuable contribution: thanks to the highly efficient UNTHA Eco Power Drive, fully automated processes and many years of experience, UNTHA’s XR shredders can process even the most difficult material streams in a single pass and deliver a homogeneous material that can be directly recycled or thermally reused.”
The Austrian company has many years of experience with difficult materials and carries out a large number of material tests each year in its own test centre and at customers’ facilities.
The company always draws conclusions from these tests and can thus further improve the machines.
For example, when recycling pulper ropes, the fully automatic internal pusher system has been developed to work in conjunction with the shredder’s cutting unit to keep the material in a new position so that it can be better grasped by the cutting knives. In this way, this challenging material can be shredded to the required fraction size in a single pass and by a single machine. In addition, metallic parts are separated by means of an overband magnet. At the end of the shredding process, there is a recyclable, uniformly shredded metal granulate and, separately, residual materials that can be sent for thermal recycling. In addition, the shredder set-up is extremely flexible and can be adapted to each customer’s needs. “Our shredders make a valuable contribution in the area of recycling and recovery of waste materials,” adds Streinik.
Case study: VPK Group
VPK is a recycled paper manufacturer in Dendermonde, Belgium. Until a few years ago, the company sent the pulper ropes from the paper recycling process to another recycling facility for treatment. The SRF/RDF material was returned to VPK to be used for the internal incineration process.
However, the company wanted to start an internal recycling process to treat the material on site and approached UNTHA to supply a turnkey package. This included not only the shredder system, but also a conveyor system, including an electromagnetic ferrous separator and a control room.
The turnkey system has a capacity of 5 tonnes per hour and produces a 50 mm stream resulting in an almost 100 per cent ferrous fraction and also an RDF/SRF product for incineration. One operator is responsible for the operation of this shredding line. UNTHA provides regular maintenance support.