An UNTHA XR2000C shredder now lies at the heart of a € 16m hazardous waste treatment plant in Setúbal, Portugal – the country’s only facility of its kind to offer a closed loop solution for tricky materials such as solvents, used oils and fuels.
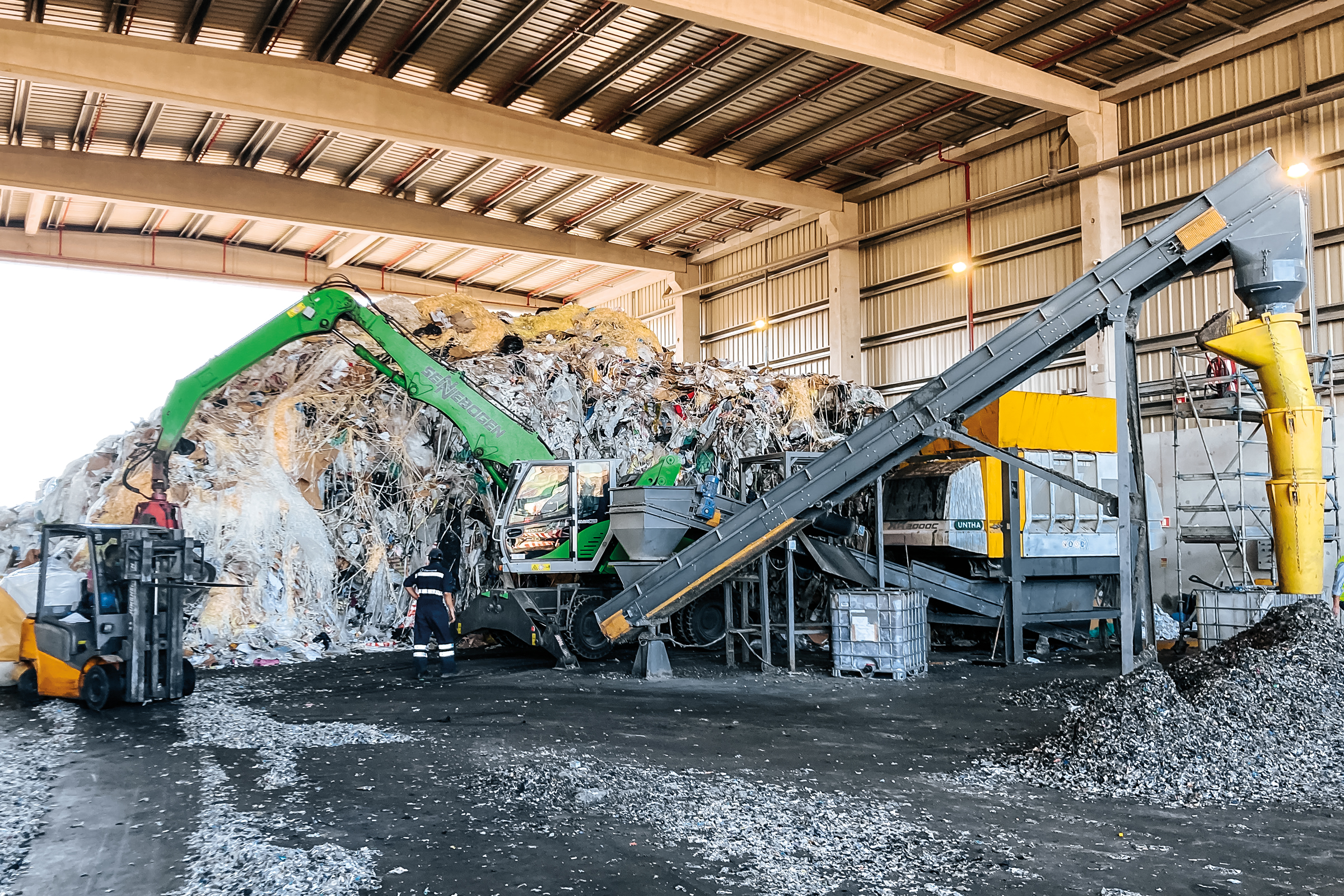
And the resulting fraction – a homogenous 35mm output material – is being used to produce RDF and SRF for national cement plants, to reduce the industry’s reliance on fossil fuels.
Carmona has long been a pioneer in the recovery and treatment of commercial, industrial and hazardous wastes, with co-founder Francisco Carmona Lobita obtaining Portugal’s first licence for the management of used oils, back in the 1970s. Fast forward to the late 1990s, and the family business became an early industry leader in the handling of hydrocarbon waste.
Now, in 2021, the 200-strong business is supporting the environmentally responsible processing of hazardous – and non-hazardous – waste on a truly national scale, having grown significantly over recent decades.
And the investment in UNTHA – which came following a visit to Austria a few years ago – means Carmona can now handle materials that would have previously been untreatable.
“We are continually investing in cutting-edge technology to ensure our business remains both efficient and progressive,” said Carmona’s managing director, Vitor Carmona. “When we heard about the capabilities of the XR, we had to see it in action and meet the people behind the machine. So we travelled to UNTHA’s innovation centre, just outside Salzburg, to see what this shredder could really do.
“We were very impressed by its robustness and versatility,” Vitor continued. “In fact, because it can comfortably handle a number of complex and abrasive wastes, with impressive throughputs, we knew it would be the only shredder we would require in our busy plant.”
Able to manufacture fuels in a single step and with low operating costs, Carmona is predicting a payback period of less than two years, for its XR investment.
“We can operate the XR with running costs of less than €3 per tonne including power and wear parts!” summarised Vitor. “I think this comfortably makes this the most efficient machine of its kind.
“The XR also shreds everything – it seems to just eat up whatever solid waste we put in it! We can now run three shifts per day, six days a week, giving us lots of capacity and the ability to become a ‘one stop shop’ for customers. As businesses in Portugal look for closed loop
solutions, this flexibility is crucial. It’s no good simply being able to recover the ‘easy’ materials – otherwise we’d never achieve the environmental progress the country is striving for.”
Carmona is no stranger to UNTHA shredding technology, having previously invested in a four shaft RS60 to help turn textiles into an alternative fuel feedstock, and the first VR machine ever sold by UNTHA back in 2014. And now – with further growth on the horizon – all eyes are on which machine will be next.