Na początku pandemii UNTHA głośno mówiła o przeoczonym potencjale zasobów, który przez długi czas pozostawał "zablokowany" w oponach, ponieważ są one powszechnie uważane za trudne - jeśli nie ekonomicznie nieopłacalne - do przetworzenia. Fascynowało nas zwracanie uwagi branży na ten strumień materiałów, między innymi dlatego, że każdego roku na całym świecie kończy się żywot 1,5 miliarda opon.
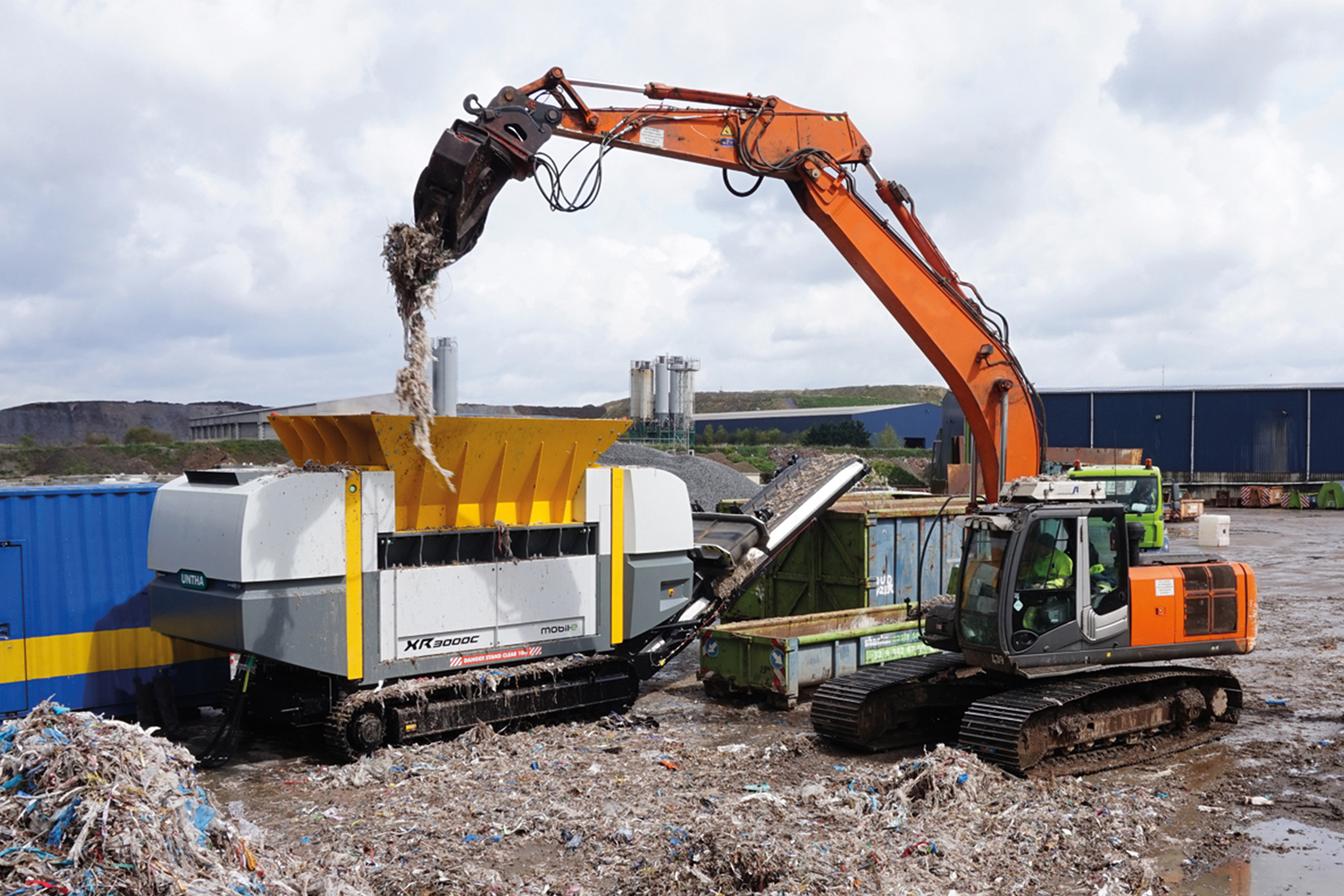
I niestety mówi się, że aż 60% z nich jest składowane, nielegalnie wyrzucane lub "tracone" z łańcucha zasobów. Postanowiliśmy więc współpracować z przemysłem, aby sprostać temu wyzwaniu. Teraz rozdrabnianie opon jest drugim najczęściej odwiedzanym obszarem naszej strony internetowej, zaraz po naszej stronie głównej! Rozdrabnianie materacy - kolejny temat, który ostatnio wręcz eksplodował w tematyce odpadów i recyklingu - nie jest daleko w tyle.
Nie poruszamy tego tematu, aby powtarzać, jak świetne są rozdrabniacze opon i materacy UNTHA. Sedno sprawy tkwi w tym, że jest to dowód na to, że innowatorzy w przemyśle nie chcą zadowolić się tym, co zawsze było robione. Dążą do postępu, napędzają większe zmiany środowiskowe i zwiększają bezpieczeństwo zasobów na świecie. A nic tak nie napędza innowacji jak kryzys.
Pomaga to wyjaśnić, dlaczego operatorzy z coraz większą uwagą przyglądają się szerokiej gamie notorycznie kłopotliwych odpadów, a warkocze z pulpera - nieunikniony produkt uboczny procesu produkcji papieru - mogą być kolejnym dużym trendem. Choć bardzo różnią się od opon i materacy, warkocze celulozowe są również często bardzo duże i kłopotliwe w obsłudze, ponieważ mogą osiągać ponad 12 m długości. Charakteryzują się one wysoką zawartością wilgoci, chyba że zostaną poddane procesowi mechanicznego odwadniania, a także zawierają wiele różnorodnych materiałów - głównie tworzywa sztucznego i metalu - zmieszanych ze sobą. Prawdziwy potencjał surowcowy tego strumienia odpadów jest zatem ograniczony, chyba że sploty zostaną poddane zaawansowanemu procesowi transformacji.
Nie oznacza to, że transformacja ta jest niemożliwa, ani że jest nieopłacalna. Wręcz przeciwnie, innowacje inżynieryjne oznaczają, że można tutaj odzyskać duże ilości stali do wytopu, a pozostały materiał można wykorzystać w projektach wytwarzania energii, jako RDF lub jeszcze bardziej wyrafinowane rozwiązanie pirolizy.
Największym wyzwaniem jest uświadomienie operatorom co jest możliwe.
Kilka lat temu, na przykład, pewna papiernia na kontynencie europejskim wysyłała 10 000 ton czystych, nieprzetworzonych odpadów z warkoczy pulpera (metal i tworzywa sztuczne w proporcji 1:3) do specjalistycznego zagospodarowania poza zakładem. Jednak z idąc z nurtem zrównoważonego rozwoju, firma chciała zamknąć obieg i wykorzystać potencjał zasobów tego strumienia odpadów we własnym zakładzie - jednocześnie czerpiąc korzyści finansowe z tego procesu. W tym przypadku, z trudnym przeznaczeniem radzi sobie rozdrabniacz UNTHA XR3000C z przekładnią o wysokim momencie obrotowym i dwoma rzędami tnącymi, z funkcją automatycznego cofania, aby pomóc w przepływie materiału. Rozdrobniona frakcja opuszcza maszynę za pośrednictwem zamkniętego poziomego przenośnika z wewnętrznymi i zewnętrznymi skrobakami ułatwiającymi czyszczenie, a następnie trafia do elektromagnetycznego separatora stali. Metalowe elementy są przeznaczone do sprzedaży, a pozostały materiał tworzy idealną specyfikację RDF dla własnej technologii przetwarzania odpadów w energię. Może on oczywiście zostać sprzedany zewnętrznemu dostawcy paliwa alternatywnego, co stanowiłoby dodatkowy strumień przychodów dla operatora. Do przetwarzania warkoczy pulpera wymagana jest specjalna technologia, ponieważ żadne dwa fragmenty splotów nie są takie same - jednorodność materiału wejściowego jest zatem mało prawdopodobna. Odwadnianie upraszcza nieco proces, podobnie jak wstępne cięcie lin do długości <3 m. Aby spełnić wymagania tego projektu, w momencie wdrożenia rozdrabniacz ten był skonfigurowany do osiągania wydajności 5 ton na godzinę. Obecnie, w innym miejscu w Europie, trwają prace nad uruchomieniem linii do przetwarzania lin pulperowych, która będzie w stanie przetwarzać 10 ton na godzinę. Dokładna technologia wymagana w danym zakładzie będzie zależeć od liczby linii rozwłókniających generujących odpady i ekonomiki danego projektu. Kluczowa jest rozmowa o tym, co jest możliwe - a także o prawdopodobnym okresie zwrotu.