References
At Schaufler GmbH in Lower Austria, copper cables, aluminium and composites have to be shredded in such a way that they could be further processed in-house. UNTHA’s XR3000C shredder turned out to be the solution. The recycling company is particularly impressed with its high throughputs, energy efficiency and low wear rates.
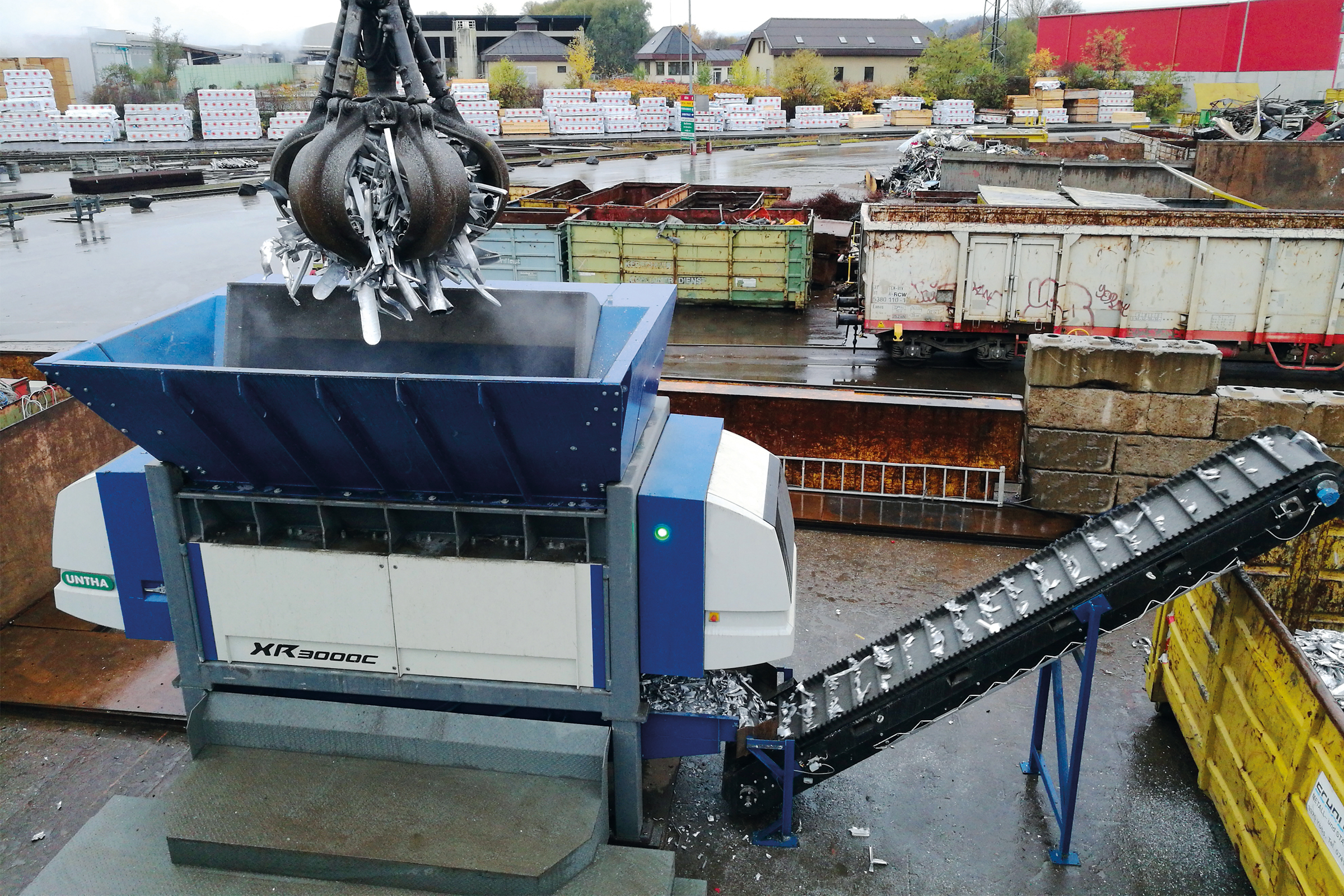
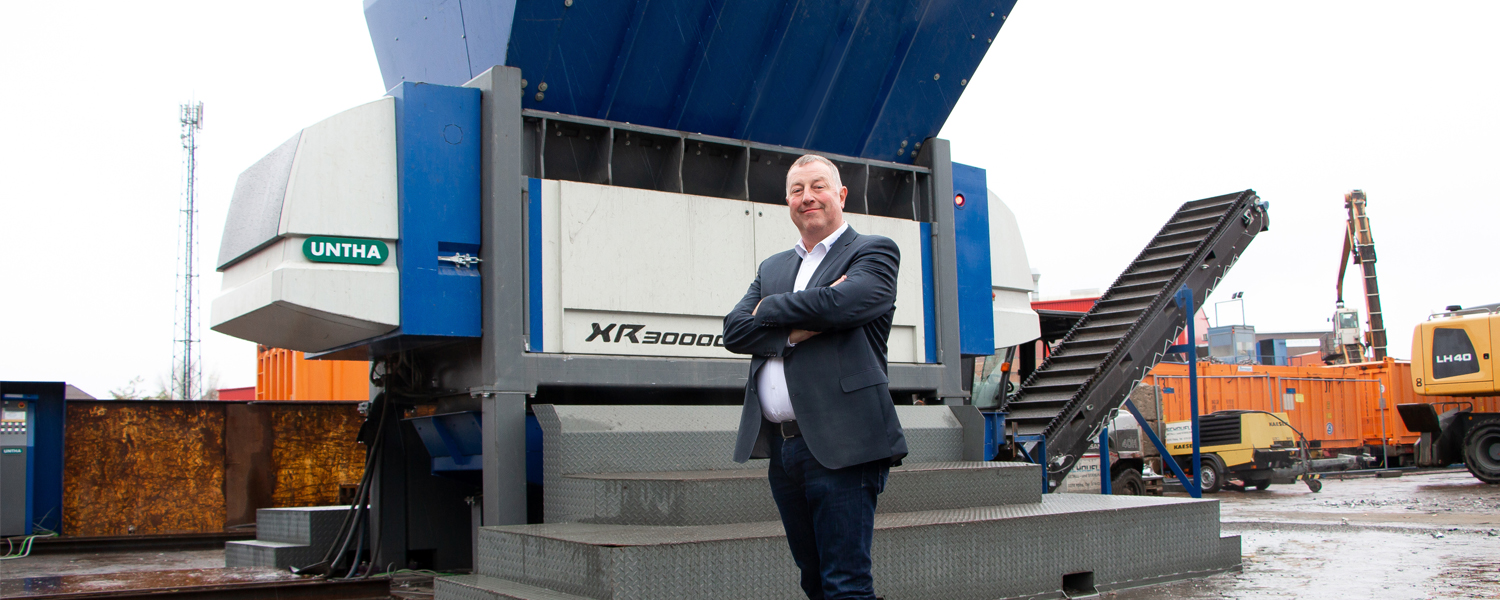
Schaufler GmbH in Ybbs an der Donau/Lower Austria is a recycling company employing 120 people. In addition to its headquarters in Ybbs, the family business that has been around since 1948 also operates sites in St Barbara/Styria and Strebersdorf near Vienna. The company's areas of activity include not just recycling, but also waste management and fitting and removal as well as a specialist iron store at the Ybbs site. Schaufler's core competence is material recycling, in particular of scrap iron and non-ferrous metals such as copper, aluminium, zinc and stainless steel.
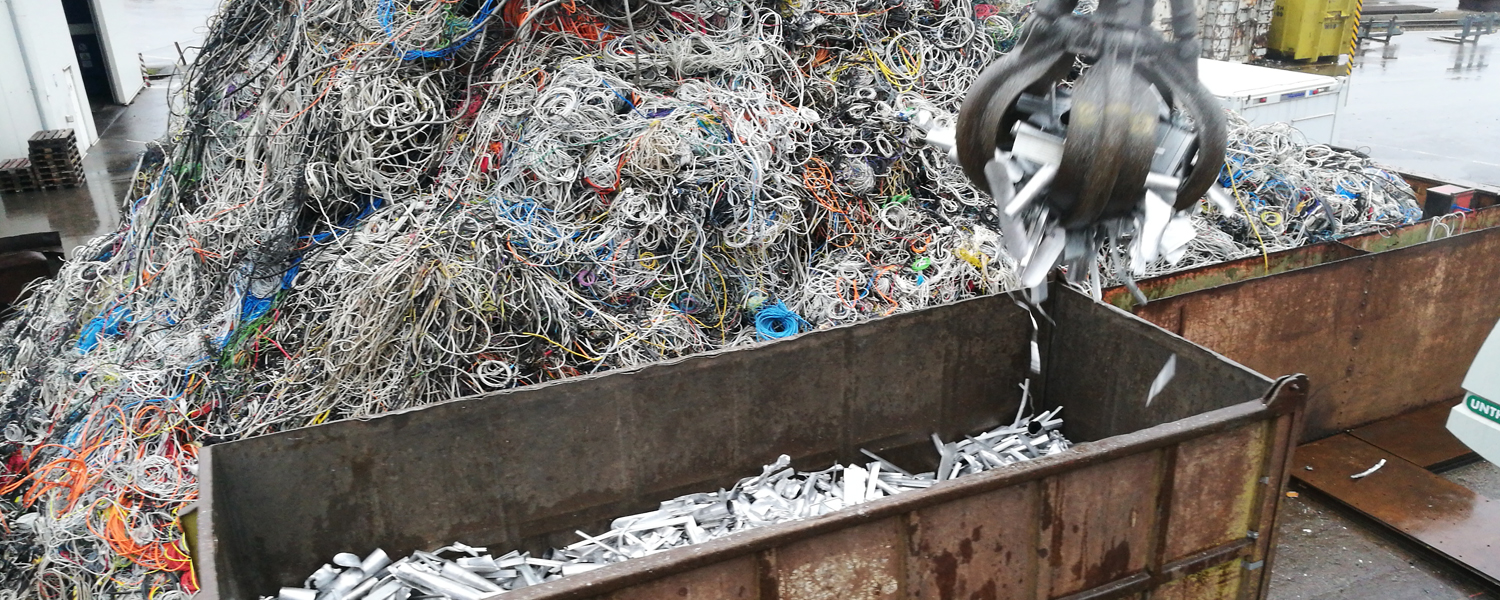
Schaufler had very clear requirements for its new shredding solution: Copper cables, aluminium and composites had to be shredded in such a way that they could be further processed in-house. In recent years, the company had been trying hard to locate processing and shredding equipment for its specialised field of application.
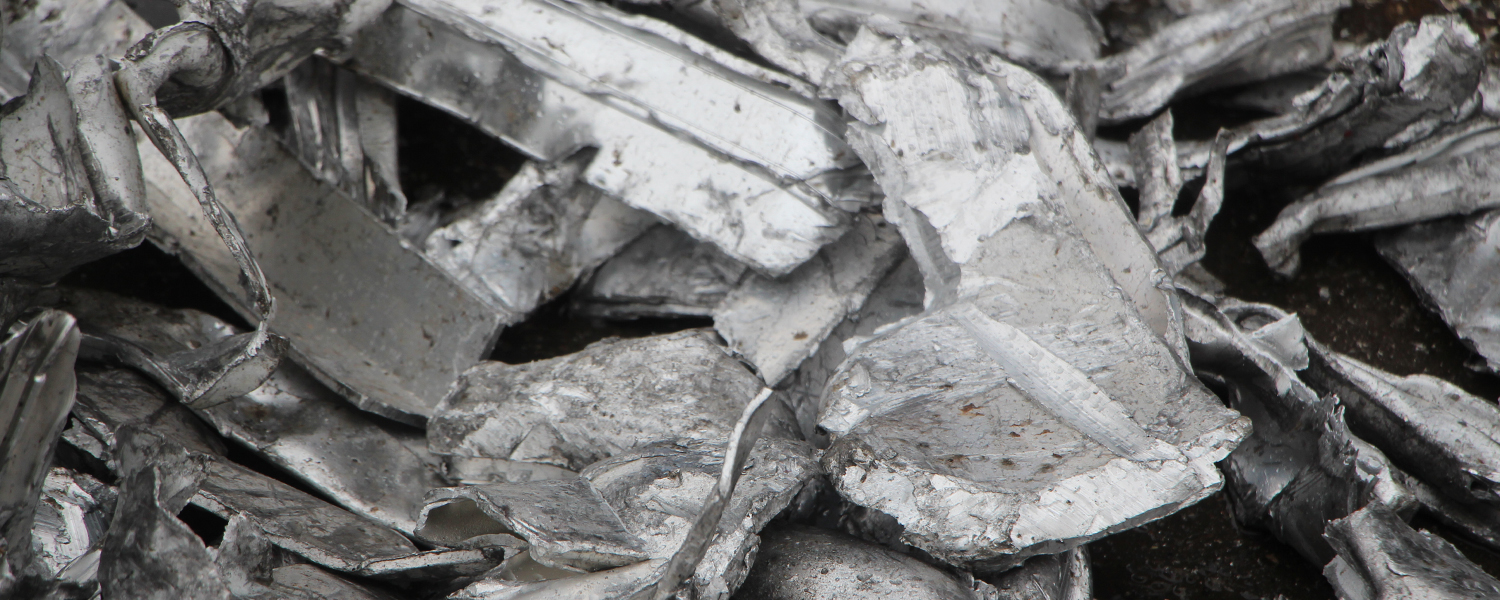
The UNTHA XR3000C offers a high throughput and is also extremely maintenance- and user-friendly. With a throughput of 20 tonnes per hour for copper cables, 8 tonnes for aluminium and 10 tonnes for composites, UNTHA's XR3000C has more than proven its enormous capacity at Schaufler GmbH. The scope of delivery also included a vibro-trough that transports the shredded material to the conveyor belt.
We were really impressed with the XR3000C, in particular with the high throughput, great energy efficiency and low wear rate. All these factors made us decide to put our trust in this product on our path towards even more comprehensive recycling services. We highly recommend the unit and UNTHA.
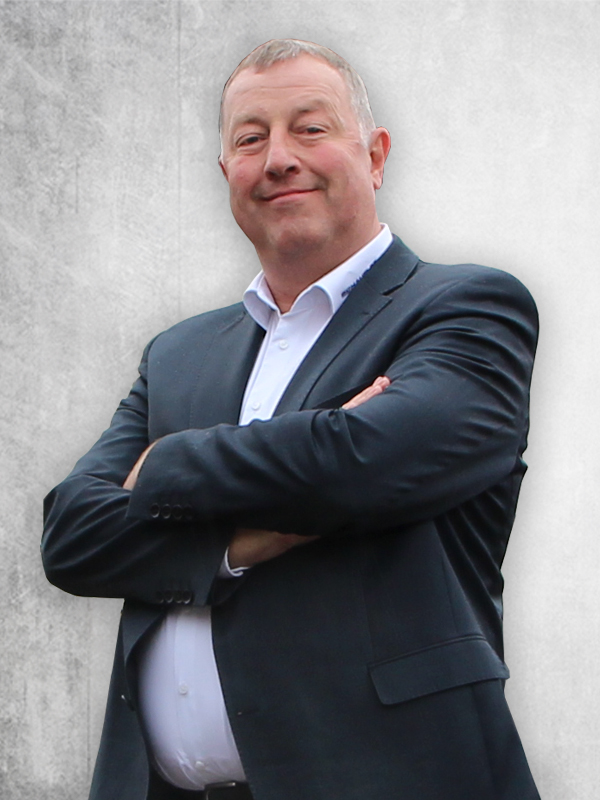
Paul Losbichler
Managing Director
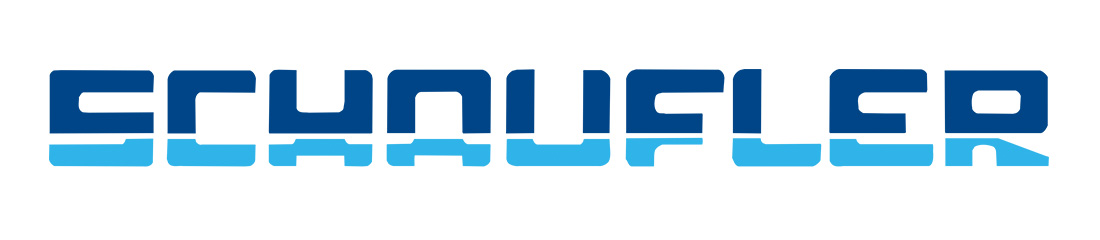
In UNTHA, Schaufler have finally found a partner who took their wishes into account and provided targeted, solution-orientated support. Schaufler was able to test their material on a
trial device and made a clear decision in favour of the XR3000C due to its impressive performance.
Decision-makers at Schaufler were particularly impressed with the high throughput rate, energy efficiency and low wear rate of the machine, which has been in operation at the Ybbs site since July 2019. For Schaufler, the quality of the output material provided by the XR3000C is also a decisive factor.
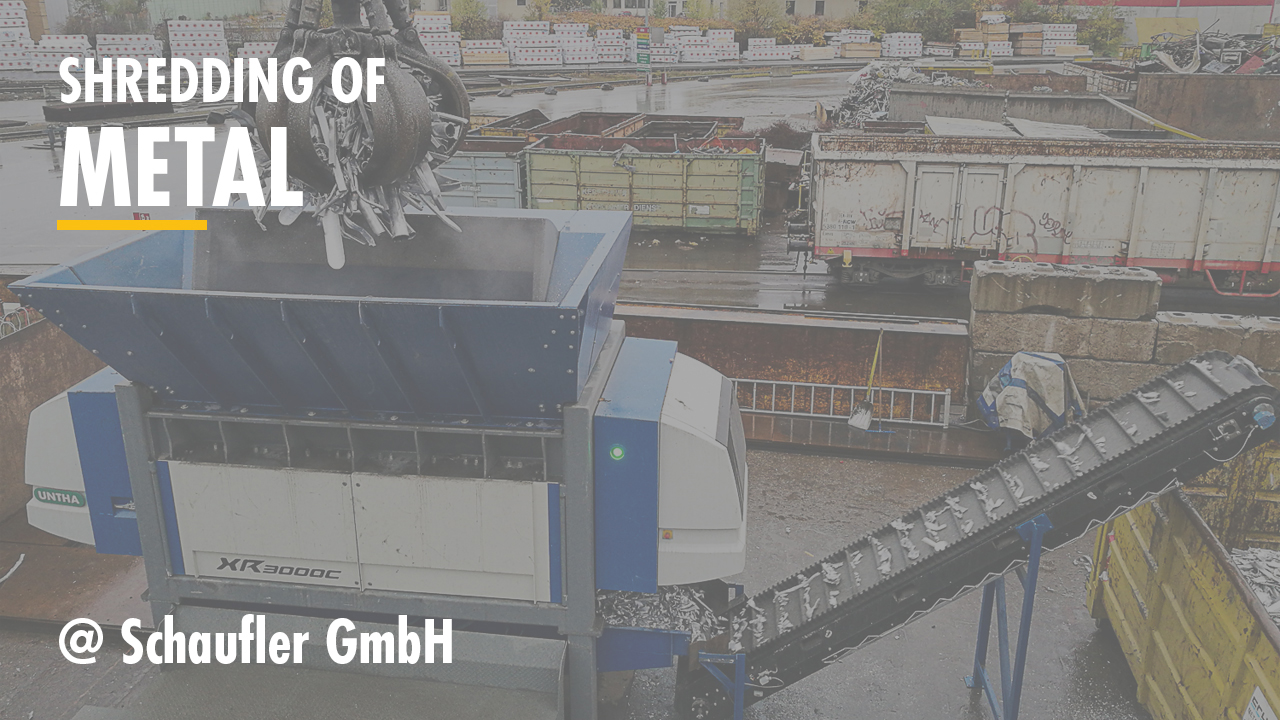
Interview with DI Dr. Paul Losbichler, CEO Schaufler GmbH