References
In the pre-shredding of non-ferrous and ferrous scrap metals the recycling company Schaufler profits from the new ZR2400W’s plus points: the best energy efficiency, swift cleaning options and high performance capacity.
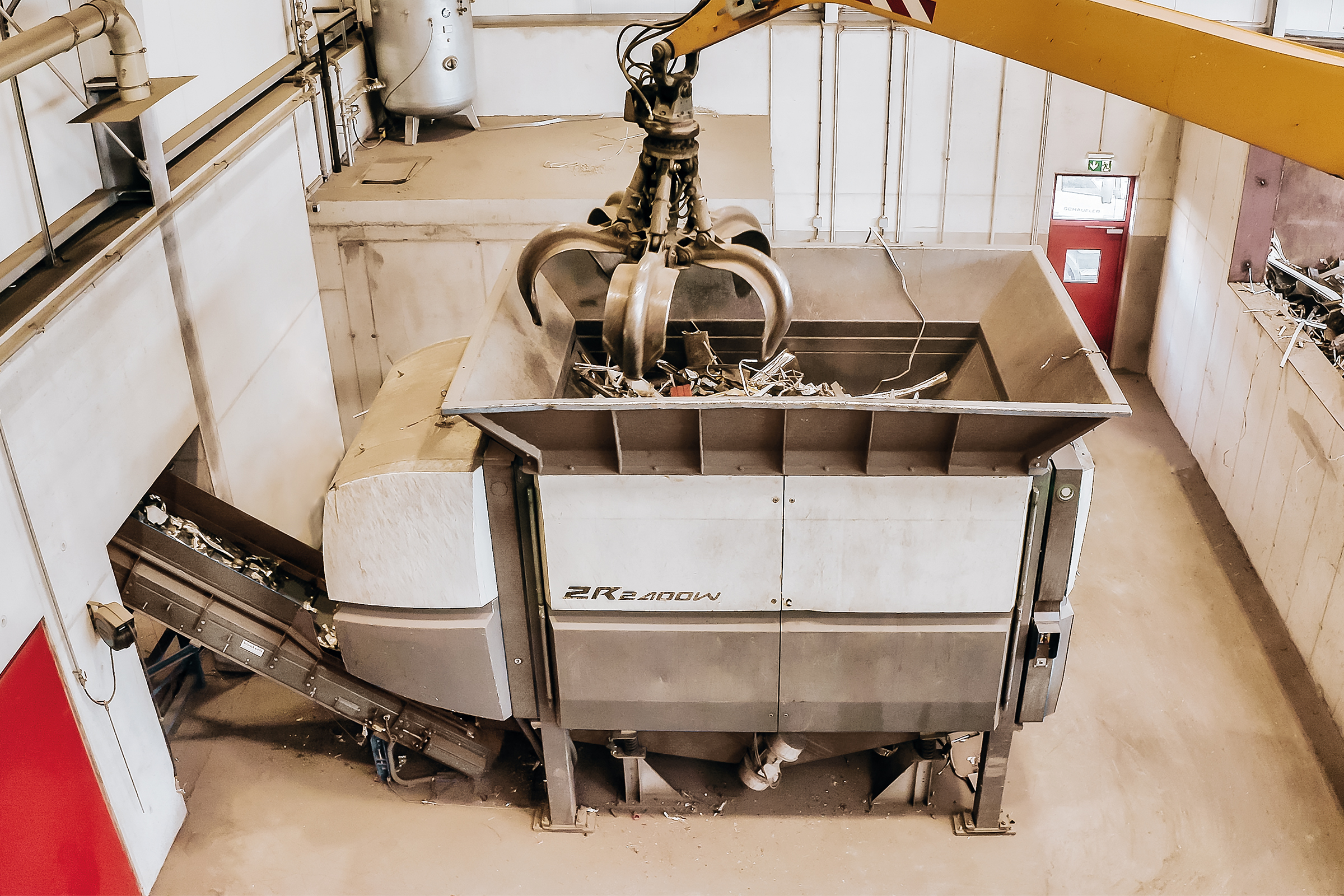
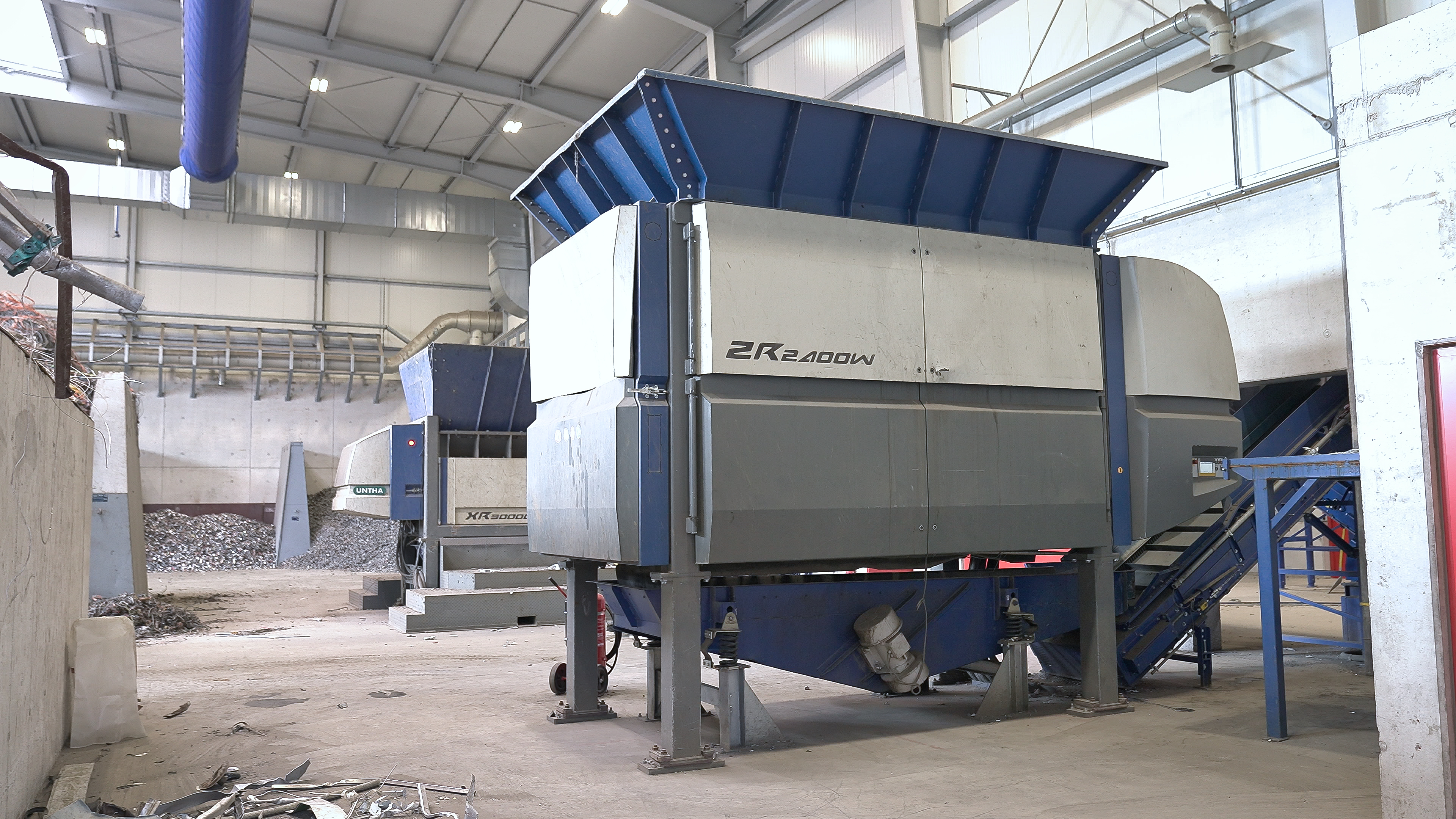
Schaufler GmbH in Ybbs an der Donau/Lower Austria is a recycling company employing 120 people. In addition to its headquarters in Ybbs, the family business that has been around since 1948 also operates sites in St Barbara/Styria and Strebersdorf near Vienna. The company's areas of activity include not just recycling, but also waste management and fitting and removal as well as a specialist iron store at the Ybbs site. Schaufler GmbH focuses on the recycling of NF and FE scraps. For NF, the emphasis lies on composites of aluminium, lead, tin and zinc.
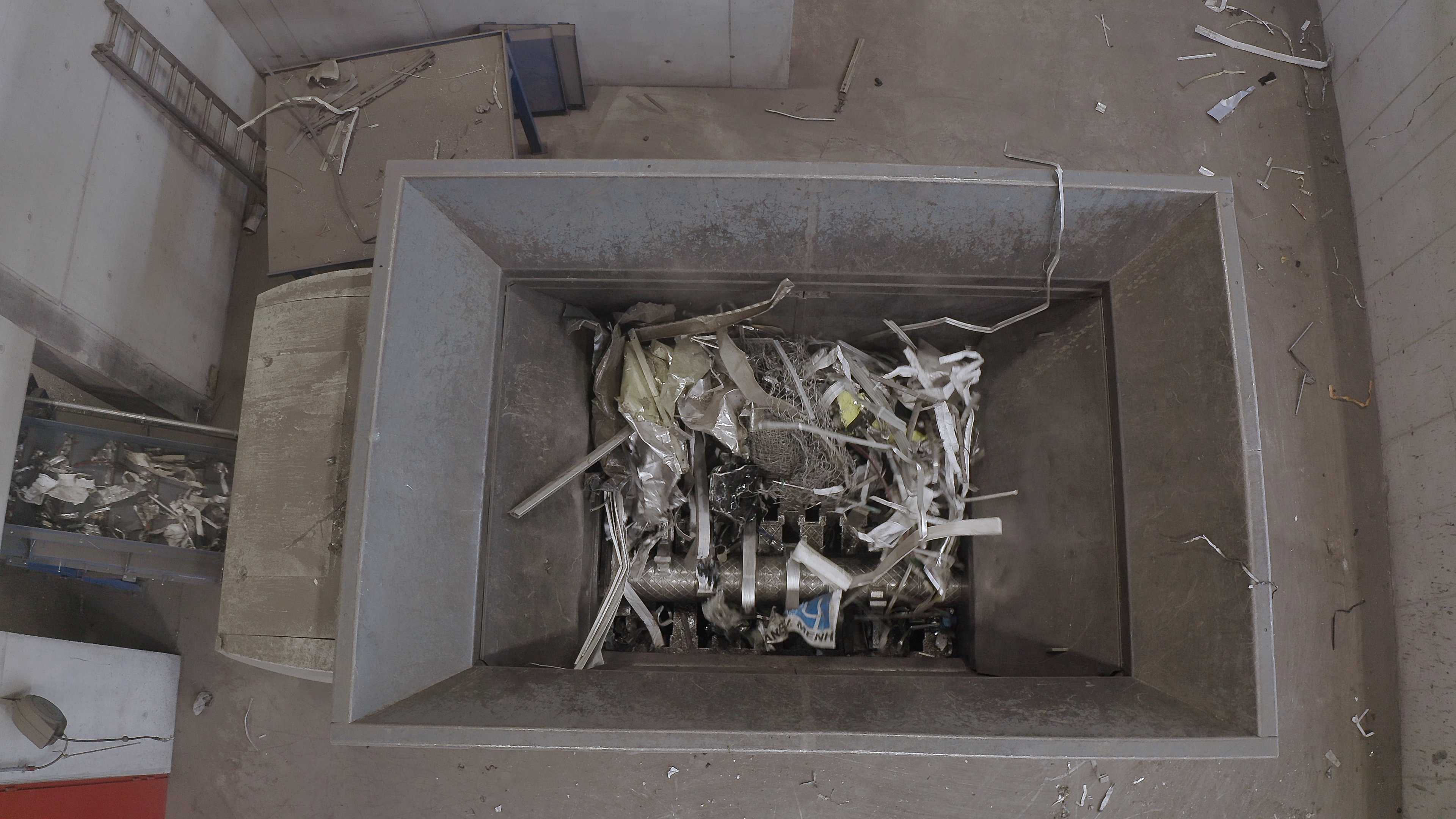
What motivated Schaufler to look for a new pre-shredding solution was the fact that the demands of its clients, mostly smelting works and foundries, are becoming tougher all the time with regard to higher quality and purity. The recycling company wanted a machine for the pre-shredding of NF and FE scraps. Their main criteria were energy efficiency, ease of cleaning, and outstanding performance capacity.
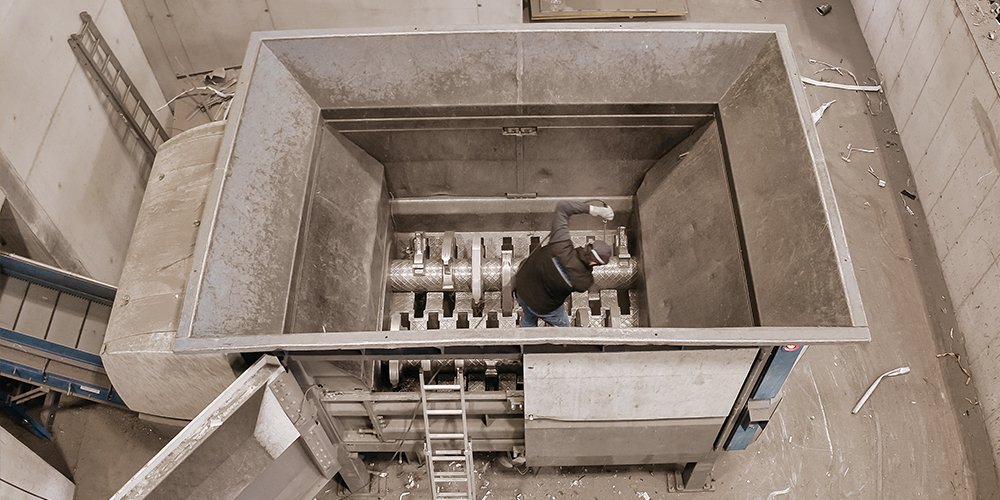
With UNTHA’s ZR2400W, the company chose the 2-shaft shredder with the lowest lifecycle costing (LCC) in its class. The recycling company had the opportunity to test shredders from different manufacturers on site, focusing on two areas in particular: ease of cleaning, which is a big factor for NF scrap, and low energy consumption, i.e. the specific energy input in kW/h per tonne. From a series of tests using four units in total, the UNTHA ZR2400W shredder emerged as the clear winner because of its superior performance in both these areas.
The high-performance pre-shredder with the energy-efficient UNTHA Eco Power Drive is ideal for high throughputs as well as high-volume waste and recyclables that are difficult to shred. The robust, high-resistance machine is designed for multi-shift, continuous operation. The quick-change table system and the streamlined construction ensure a high level of plant availability. The powerful, slow-running ripper-cutter system is extremely resistant towards non-shreddables. The cutting shafts run independently of one another, thereby ensuring perfect material breakdown for sorting plants.
We were surprised at the fantastic results with regard to energy input in particular. Compared to other manufacturers, we are talking about energy savings worth 70,000 Euro a year as a result of using the ZR!
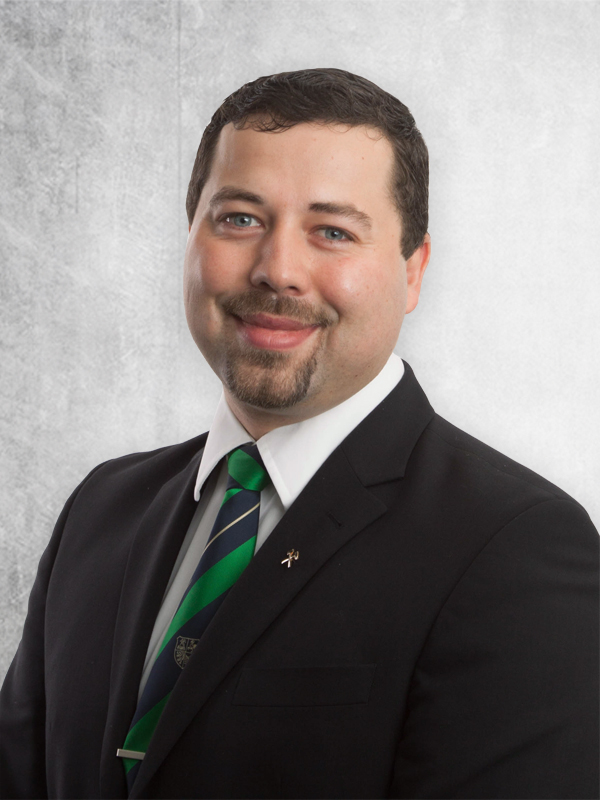
Hubert A. Schwarz
Head of Processing and Process Development
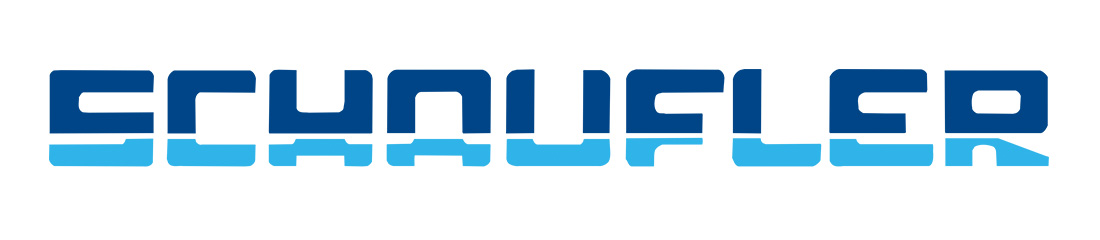
Schaufler had already worked successfully with UNTHA in the past – an XR3000C has been in operation at Schaufler since July 2019. Three main points were essential for the purchasing decision: First, versatility, i.e. the fact that the unit can shred both large, coarse NF metals and composites. Secondly, cleaning the unit is fast, easy, and efficient, which is important due to the fact that a range of different materials are shredded on site. Thirdly, the specific energy input in kilowatt hours per tonne is very low.
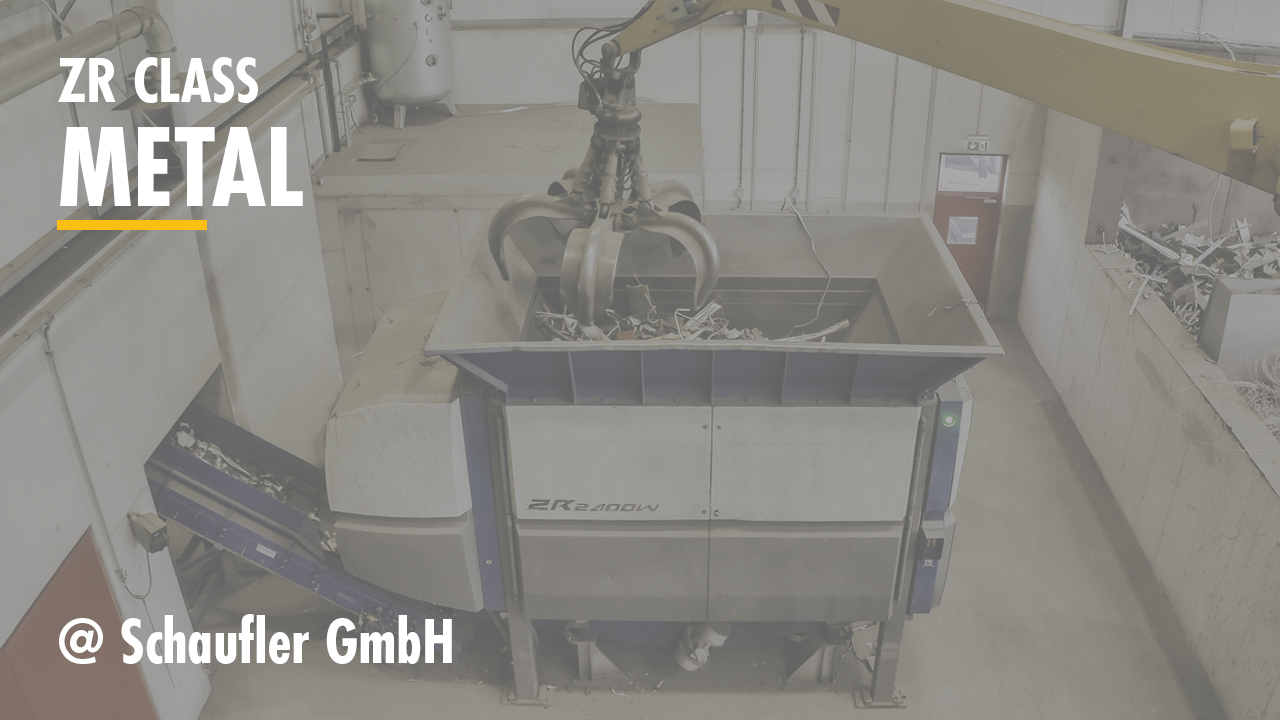
Interview with Hubert Schwarz