Agricultural film, hard plastics and waste wood – shredded with the RC cutting system
Schenker Industrie- und Städtereinigungs GmbH recycles up to 150,000 tons of material every year – including (agricultural) film, hard plastics and waste wood. A large proportion of this waste is shredded with the UNTHA XR3000RC mobil-e. The output material is then sent for material or thermal recycling. With the help of UNTHA's technology, Schenker is helping to save raw materials and reduce CO2 emissions.
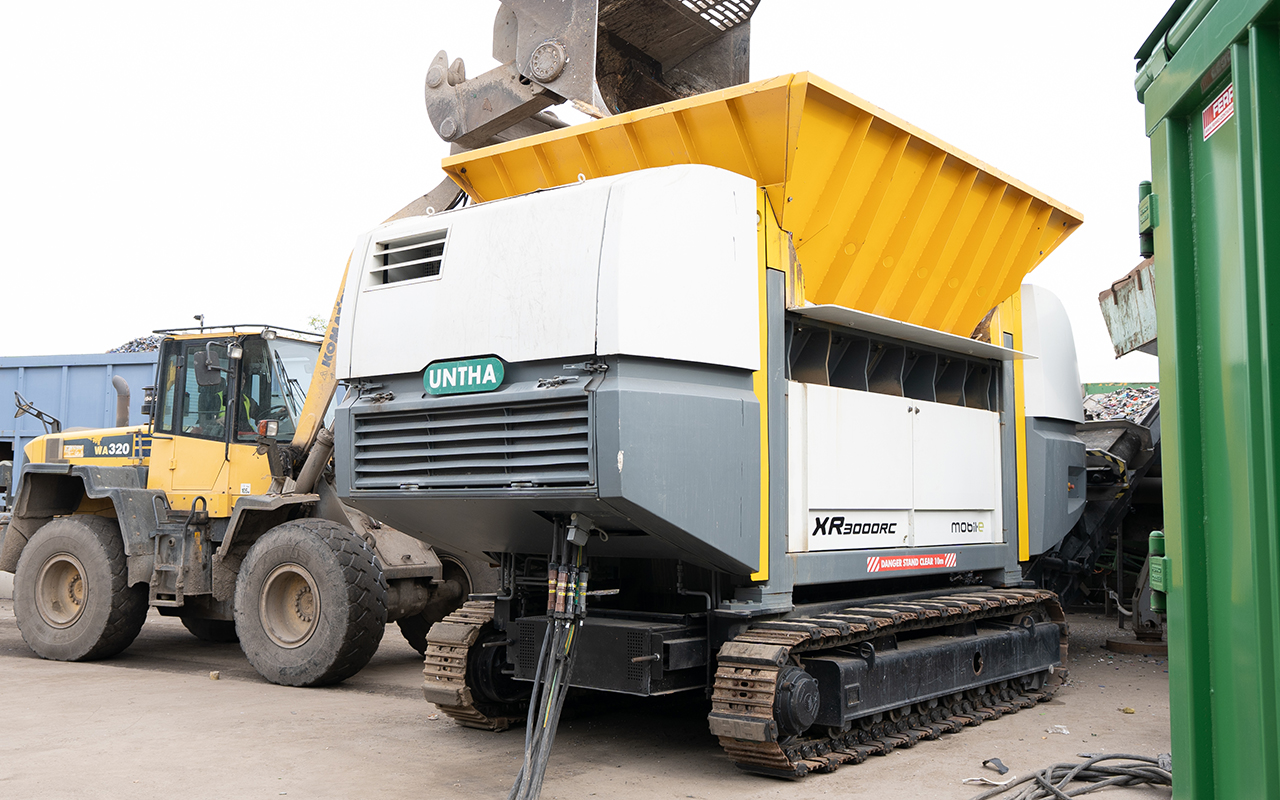
"The UNTHA XR3000RC mobil-e combines all the features we need for shredding different materials: Thanks to the RC cutting system, the infeed performance is optimal even with difficult materials, and the output is always of consistent quality. At the same time, the shredder is energy-efficient and low-maintenance," says Thomas Schenker, Managing Director of Schenker Industrie- und Städtereinigungs GmbH.
Recycling and RDF production
For the optimal recycling and reuse of hard plastics, (agricultural) films, waste wood and other materials, it is important to shred them to a homogeneous particle size. However, hard plastics and films in particular are very tough and often contain metal parts. These properties make them more difficult to process. Schenker was therefore looking for a shredder with a cutting system that ensures optimum material intake, is insensitive to impurities and at the same time produces a uniform output material. Homogeneity plays a decisive role, especially for the subsequent process steps - sorting, washing - and recycling as raw material or RDF.
UNTHA XR3000RC mobil-e
"We have already used various shredders in our company history. Over time, you learn which machine features are important for shredding specific materials. From my experience, I can say that the UNTHA XR3000RC mobil-e combines all the relevant features and is therefore ideally suited for shredding plastics, films and other materials," says Thomas Schenker.
The XR is a powerful single-shaft shredder for coarse, medium and fine shredding of different materials. Depending on the perforated screen used, grain sizes of 100 to 300 mm can be achieved. With its unique tooth shape, the RC cutting system draws in material optimally and ensures that the output material is consistently homogeneous. Thanks to the automatic material feed, the XR3000RC also does not require a pusher system. The cutting system is also particularly resistant to impurities, so even metal parts are no problem – these are sorted out after the shredding process with the help of a magnetic separator above the discharge conveyor belt. Depending on the material or material composition and the desired granulate size, this shredder can achieve a throughput of up to 70 tons per hour.
The XR3000RC mobil-e is driven electromechanically. The advantages: The motor is particularly energy-efficient, low-emission and comparatively quiet. The shredder can be connected to the power supply quickly and easily with just one connection cable – quick-lock power plug. In conjunction with the crawler-type undercarriage, the shredder can therefore be put into operation at different locations.
Images for download (Reprint free of charge for press purposes, photo credits: UNTHA shredding technology GmbH): https://untha.canto.de/b/QQL5J
Image 1: The UNTHA XR3000RC mobil-e shreds hard plastics, agricultural film and waste wood at Schenker
Image 2+3: The UNTHA XR3000RC mobil-e shreds rigid plastics into a homogeneous granulate