Sustainable and economical: reprocessing of cutting tools
UNTHA stands for reliable shredding technology. To ensure the longest possible product life and unrestricted operation, the Austrian premium manufacturer offers its customers comprehensive services such as the reconditioning of cutting tools of the RS shredders. This service is sustainable and economical: it reduces wear costs by up to 50 percent and extends the life of the shredder.
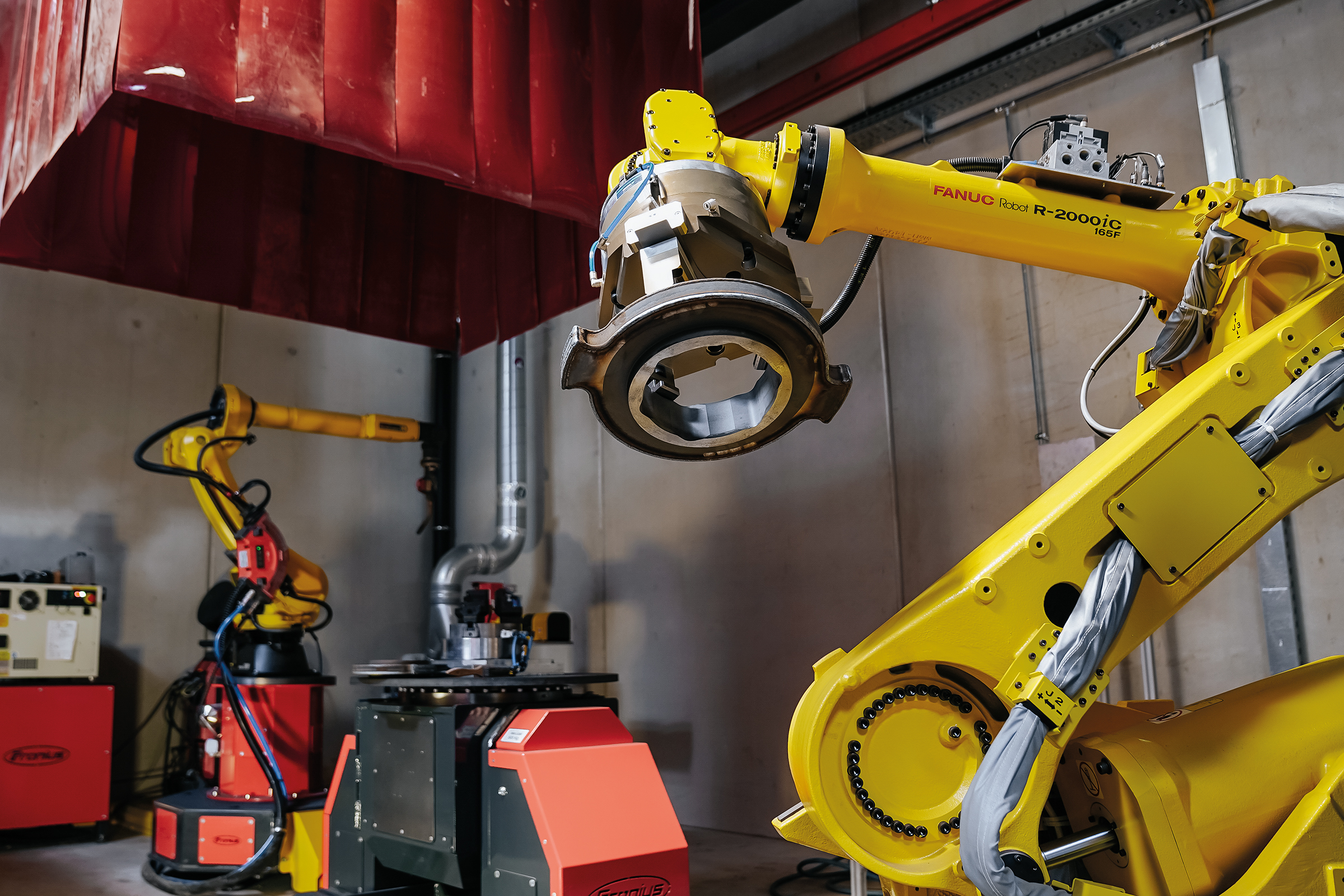
UNTHA's service experts accompany customers throughout the entire product life cycle - from purchase, installation and commissioning to possible service cases. One measure that contributes significantly to maintaining the efficiency of the shredders is the welding on of the cutting discs. At the company's location in Kuchl near Salzburg, a separate department was created for this purpose and extensive investments were made in a CNC system for reconditioning the RS cutting discs.
The robust RS shredders are mainly used in industrial recycling applications. The more demanding the material to be shredded, the faster wear becomes visible on the cutting discs. The consequences are declining throughput performance, decreasing quality of the output material and an increase in power consumption. All this is reflected in rising wear and operating costs.
Measures to reduce wear costs
At UNTHA, the focus is always on customer benefit: "We offer our customers a complete all-round service and ensure maximum machine availability. By welding on the cutting discs, we maintain the throughput capacity of the chipper and reduce wear costs by up to 50 percent," explains Bernhard Walkner, Key Account Management at UNTHA.
Based on the material to be shredded and the planned operating hours, an appropriate reconditioning interval can be determined. After a certain running time, the cutting unit is removed and sent to the UNTHA Service Competence Centre. There, the cutting discs are welded and milled to their original dimensions. The professionally reconditioned cutterbar is then reinstalled and shreds like a new cutterbar. This process can be repeated several times, only then will a new cutting unit be necessary. The weld-on service therefore stands for sustainability as well as economic efficiency.
The advantages at a glance
Up to 50 percent cost savings through reconditioning
A cutting unit as good as new with original dimensions thanks to modern CNC machinery
Everything from a single source: from dismantling to welding on and reinstallation of the cutting unit
Multiple reconditioning possible
Qualified advice from our experts
Extension of the machine's service life thanks to permanently optimised shredding process
Fair price-performance ratio
For more information on reducing wear costs and the comprehensive UNTHA services, click here.