References
Thanks to its energy efficiency and the RS cutting system, the stationary UNTHA XR3000RC reliably shreds a wide range of materials. Construction waste and bulky waste are shredded without any problems. The homogeneousoutput material is used as an alternative fuel in the cement industry to reduce the use of fossil fuels or replace them altogether.
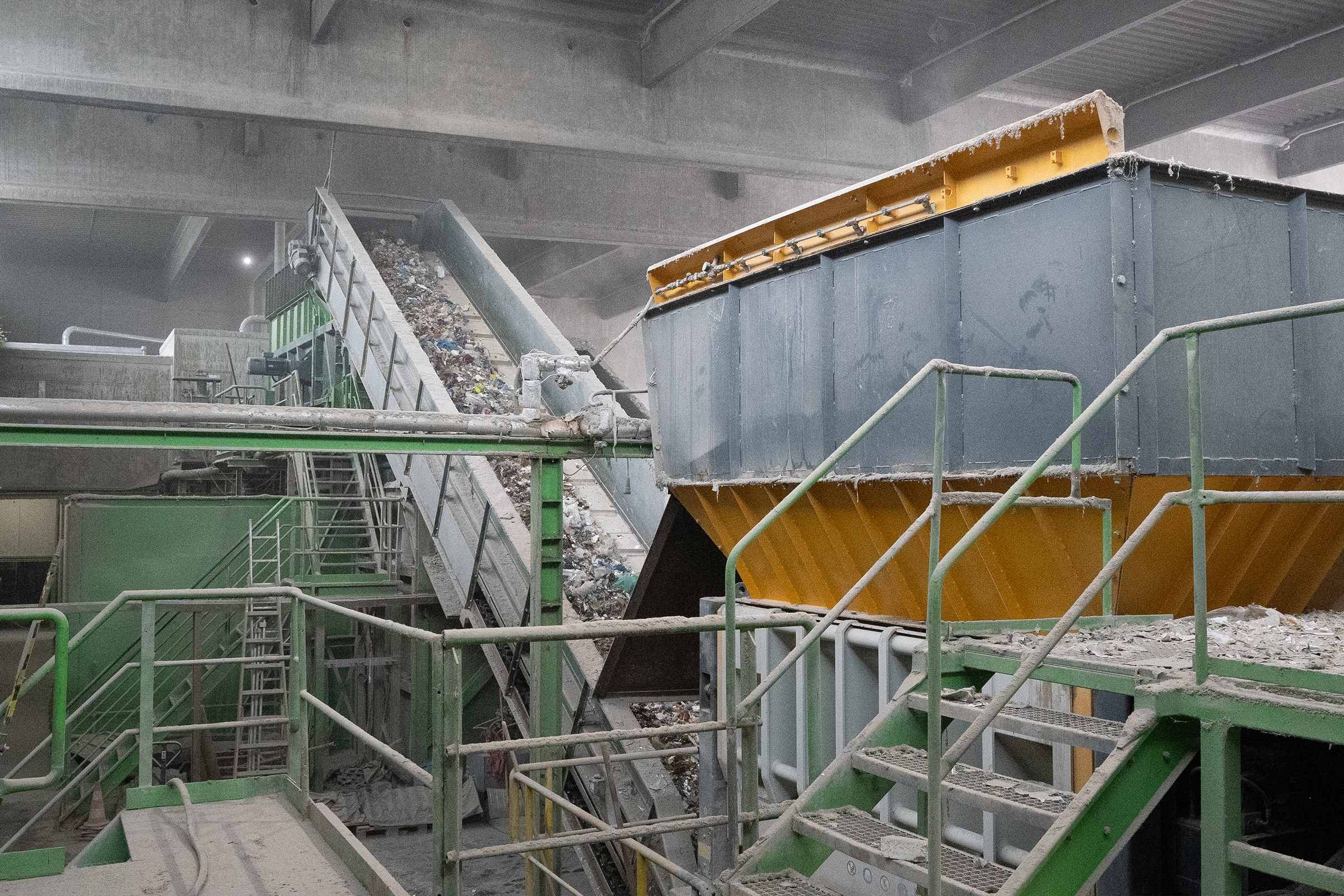
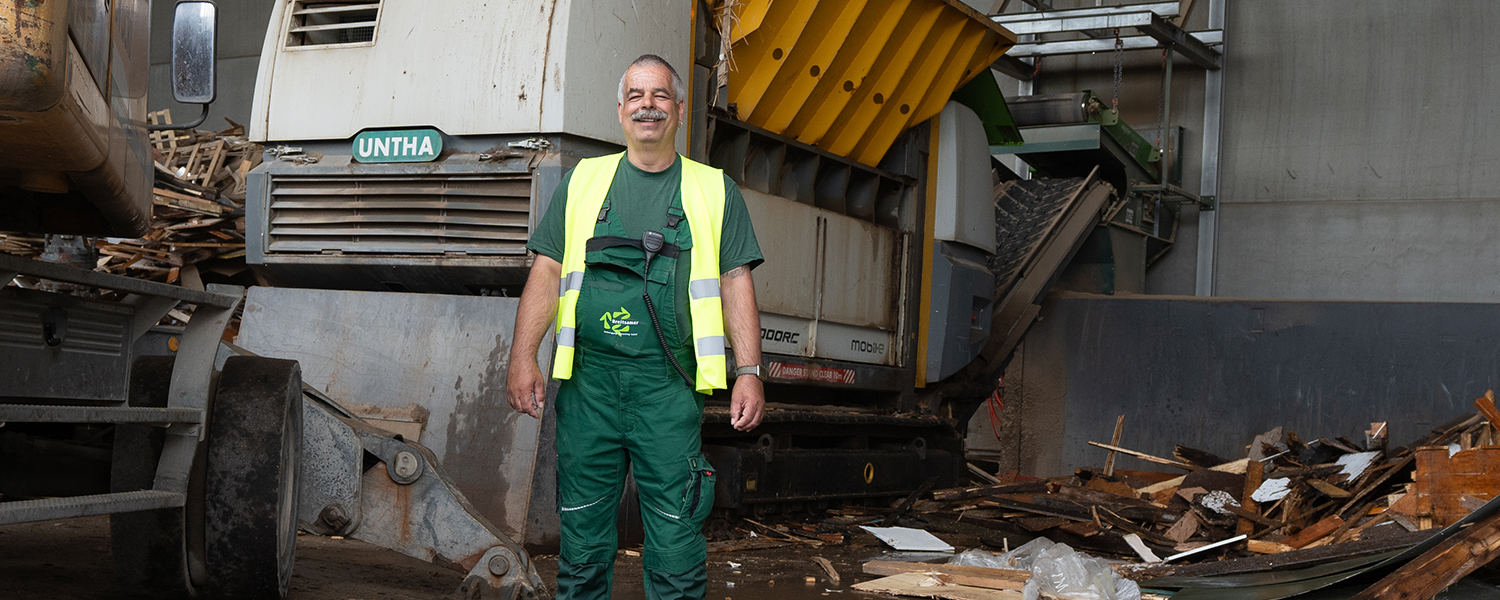
Breitsamer Entsorgung & Recycling GmbH was founded in 1956. The services offered by the company include recycling consulting, sorting of commercial waste, alternative fuel production, waste wood processing and the handling of hazardous waste. At its Munich location, Breitsamer shifts approximately 200,000 tonnes of commercial waste, construction waste and recyclable materials per year. 160 employees, 50 vehicles and state-of-the-art sorting and processing systems ensure that waste and recyclable materials are recycled and/or processed for thermal recovery. The goal is to use 100 percent of available resources, thus making a contribution to the closed-loop economy.
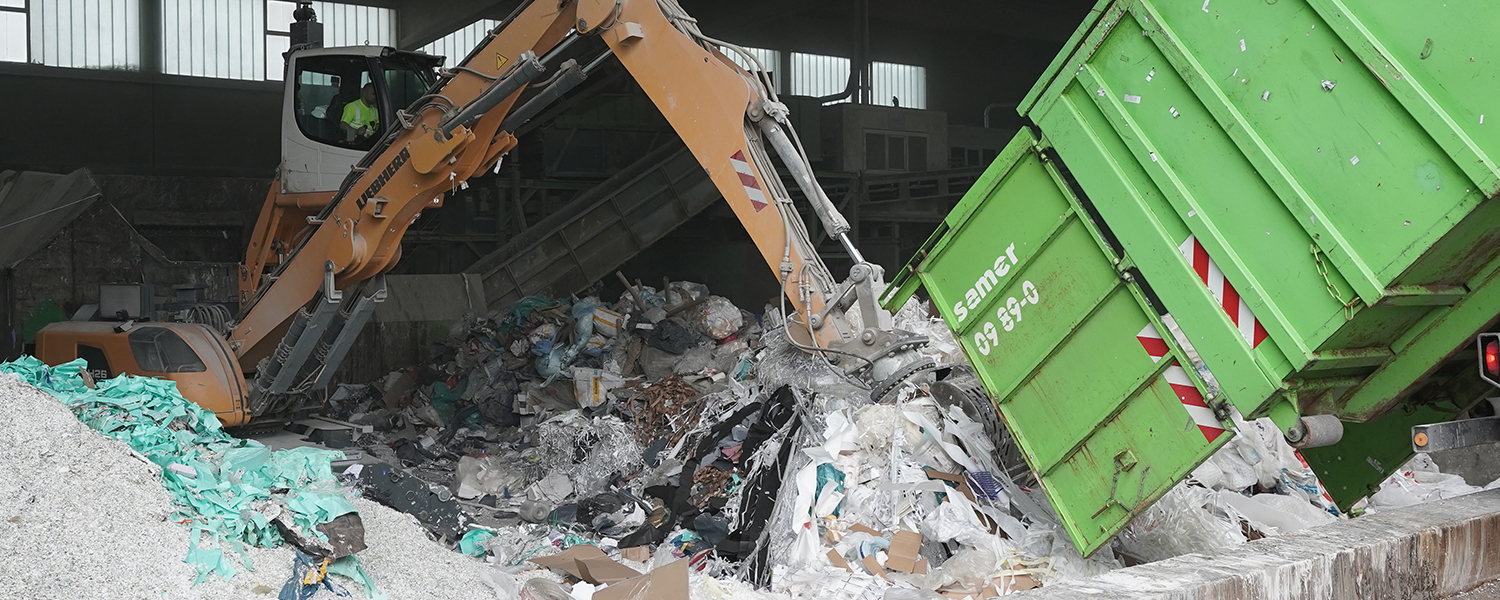
Breitsamer processes construction waste and bulky waste to produce alternative fuel for the cement industry and for heating plants. The company was on the lookout for a suitable shredding solution. Important criteria included energy efficiency, a throughput of approx. 15–20 tonnes per hour, and a homogeneous output material with a grain size of approx.200 mm. A uniform granulate is of crucial importance, in particular for the subsequent processing steps.
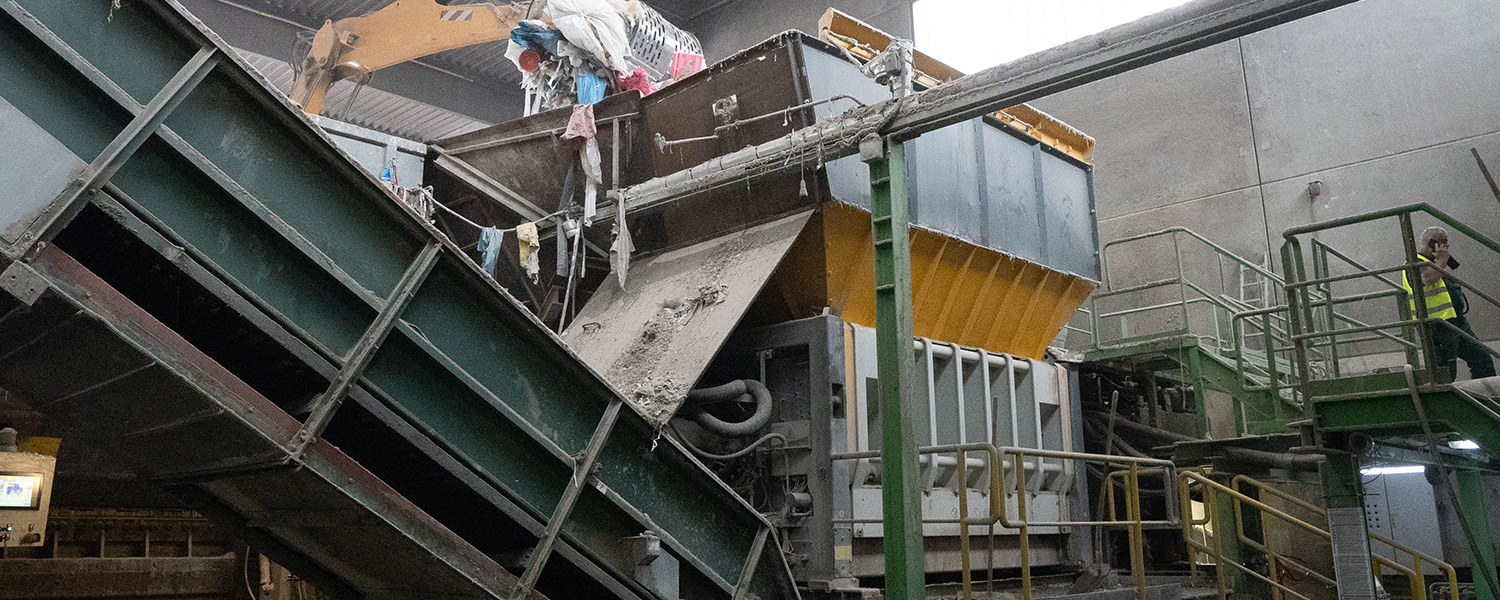
Following a long-term test run, the company opted for a stationary XR3000RC, which shreds approximately 35,000 tonnes of material per year. The integrated screening bars, placed at 155 mm gaps, ensure a highly homogeneous output with an extremely low amount of excessive lengths. This makes the shredded material particularly suitable for the subsequent processing steps and for use as alternative fuel. The RC cutting chamber was specially developed for the pre-shredding of different materials and for throughputs of up to 70 tonnes per hour. The unique tooth shape makes for a highly efficient material feed. Hardfacing of the rotor and stator blades is possible, which means that the lifespan may be extended continuously. The rotor of the XR3000RC runs with a low speed, making the shredder highly energy-efficient and extremely resilient towards non-shreddables.
In our plant, we use the UNTHA XR3000RC as a mobile and stationary shredding solution. The RC cutting chamber allows us to process a range of materials, such as waste wood, mixed construction waste and bulky waste in a reliable and energy-efficient manner.
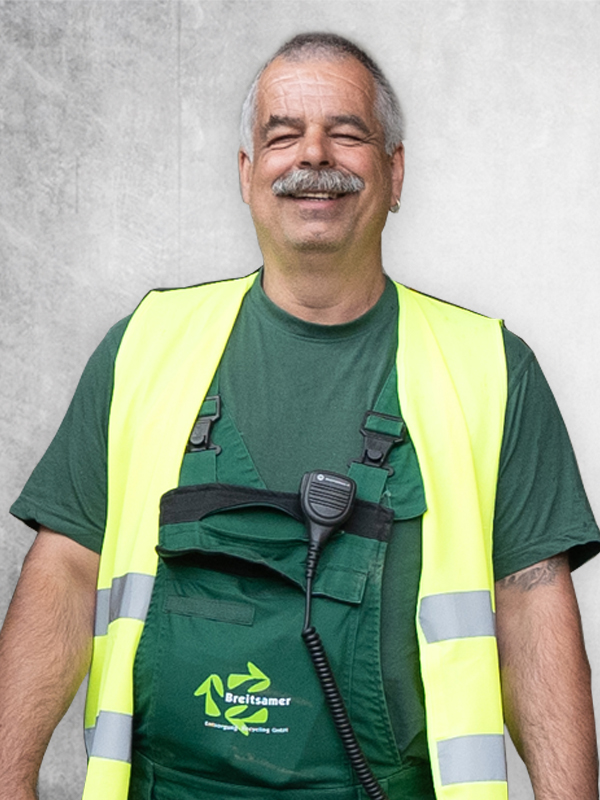
Karlheinz Pfleger
Plant Manager
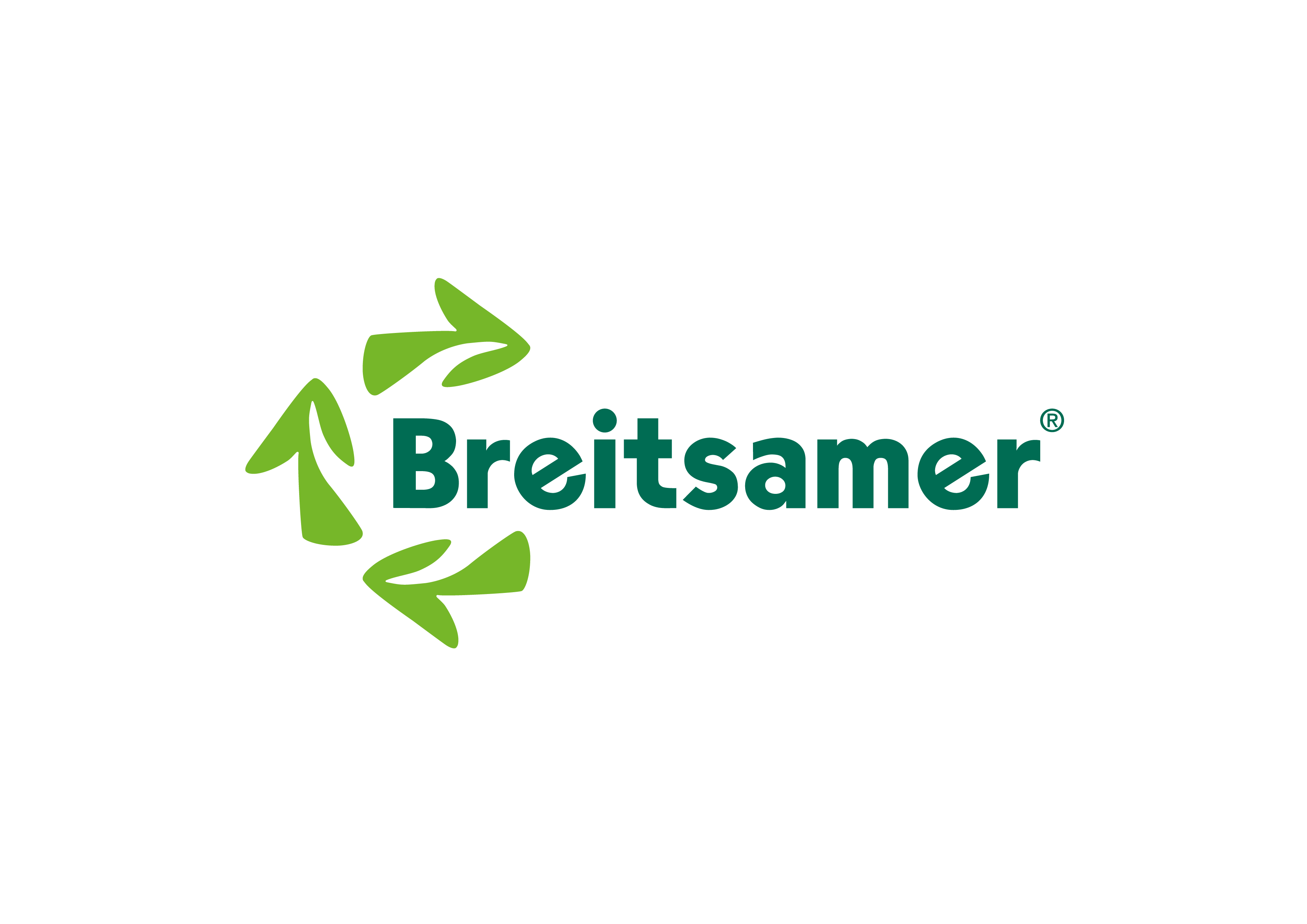
Low electricity consumption, a homogeneous output material and excellent value for money were the decisive criteria for choosing the UNTHA XR3000RC. During the intense test run, the shredder ticked all the boxes. The unit was tested with a range of materials and perforated screens to find the perfect specifications for the individual requirements (grain size/purpose). The RC cutting system and the UNTHA Eco Power Drive turned out to be particularly powerful arguments. Thanks to its water-cooled synchronous motors, the shredder is up to 75 percent more efficient than comparable diesel-operated shredders.
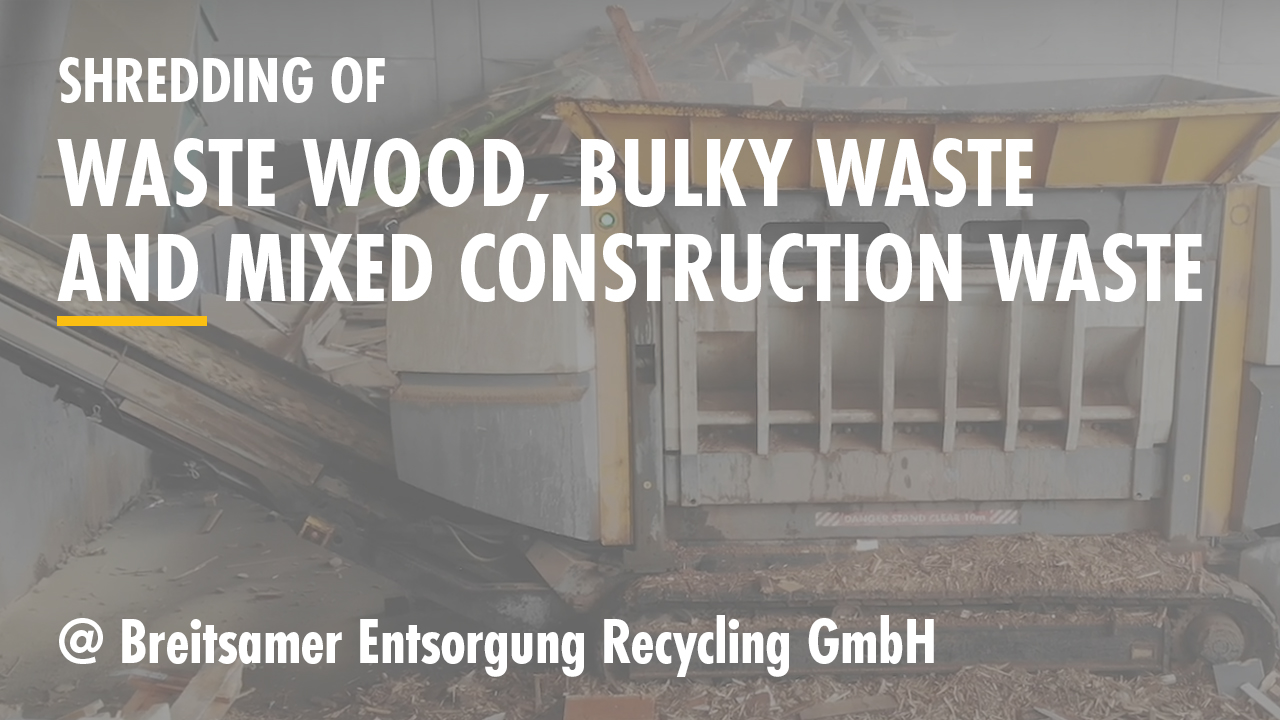