References
The family-run timber wholesaler Scheiffele-Schmiederer KG provides its customers with the entire product range for modern timber construction, including glulam and structural timber, duo beams as well as planed products and fuels. The residual wood produced at the company's own CNC joinery plant at its headquarters in Gundremmingen is chipped with an LR1000 from UNTHA and used to heat the entire site.
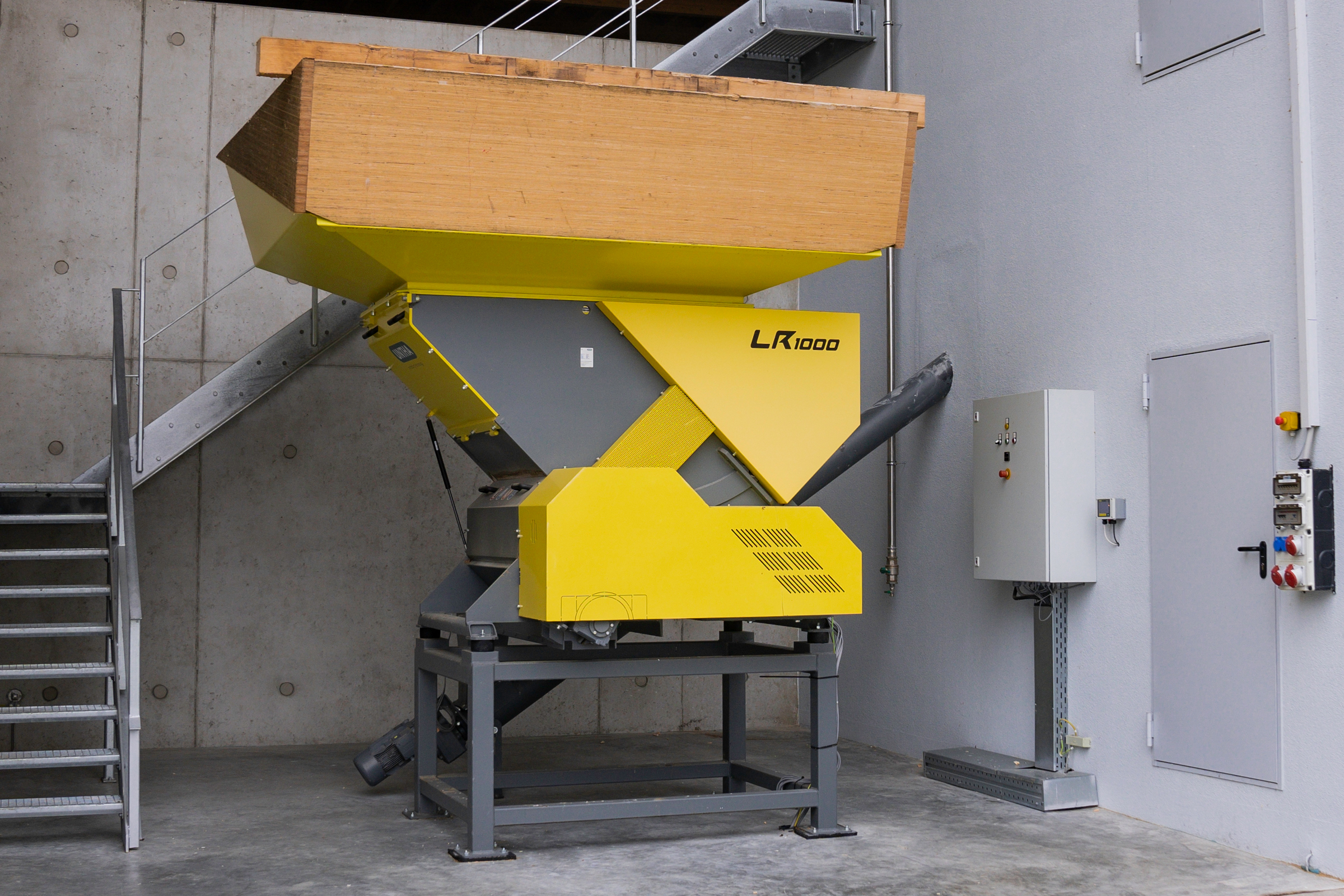
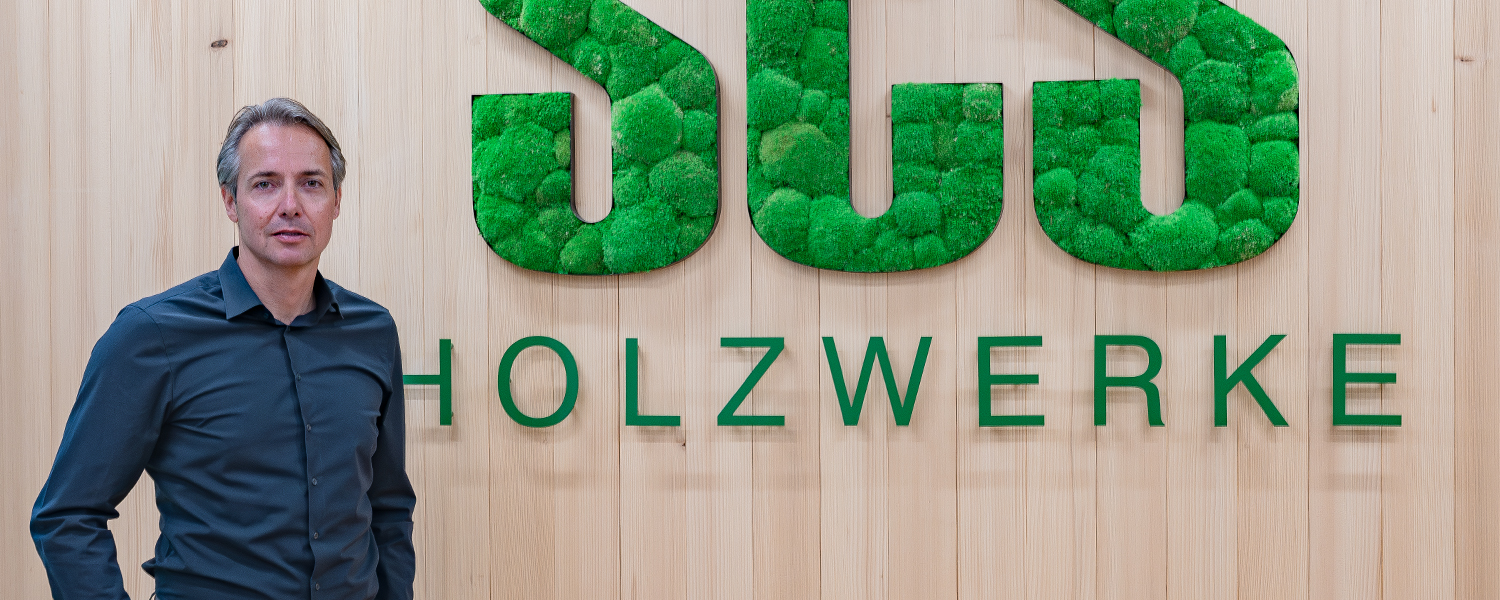
With six locations in Bavaria and Baden-Württemberg, Scheiffele-Schmiederer KG (SCS) is one of the leading family-run timber wholesale and production businesses in southern Germany. SCS has been on the market for more than 180 years and supplies primarily carpentry and timber construction businesses. The range includes, among others, laminated and solid structural timber, Duobalken, planed goods and fuels. The company has almost 200 employees.
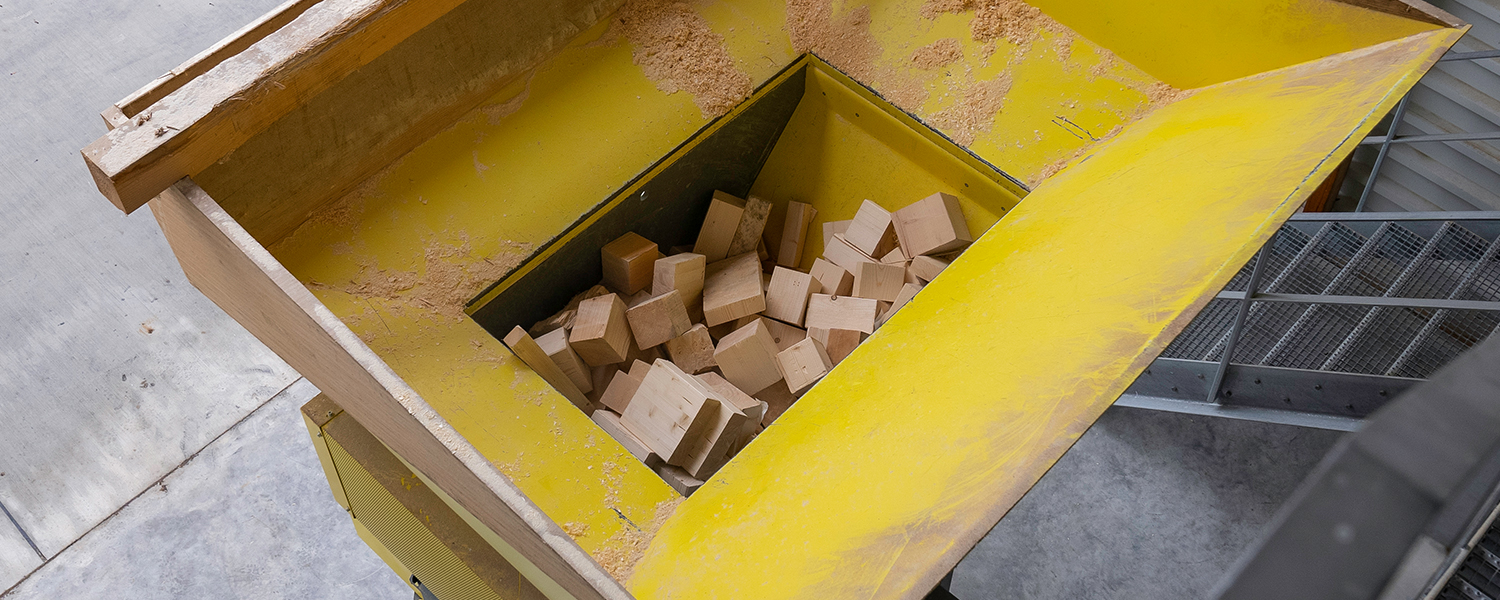
At the Gundremmingen site, SCS processes mostly laminated and solid structural timber made from spruce. The joinery machine produces residual wood sections in a range of sizes, measuring up to 100 x 60 x 24 cm, as well as mill chippings and other residual wood from production. The decisive criteria for selecting a residual wood shredder were its ability to process large, bulky pieces of timber, its energy efficiency and robust design, and the possibility of loading it using a telehandler and large tipping troughs. SCS also wanted the shredder, which would be in permanent operation, to be low maintenance and user-friendly.
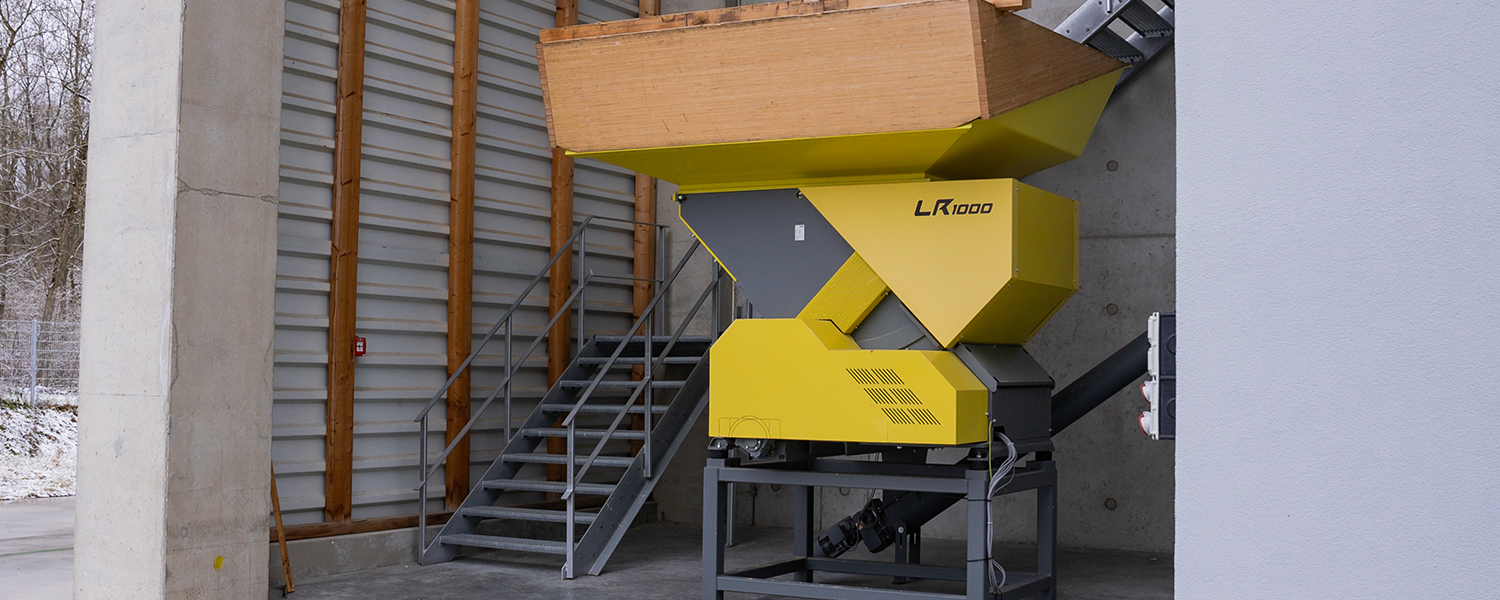
Ultimately, the robust, high-performance LR1000 turned out to be the best choice for SCS. The shredder was designed with a larger, 45° machine casing and a hopper measuring 2.7 metres across. Thanks to the wide feed-in edge, the shredder may be loaded using a telehandler and large-volume tipping troughs. In combination with the fast hydraulics system, the powerful swivelling pusher ensures constant material feed even with bulky residual wood. The result of all these features, together with the reliable cutting system, is the enormous throughput of up to 1,000 kg/h. The power rating of 22 kW makes the shredder particularly energy-efficient. The swivelling pusher works on a wear-free basis, making the LR1000 particularly suitable for intense permanent operation with low maintenance. The wood chips are removed from the side of the shredder and transported to and spread across the wood chip depot by a spiral conveyor. In order to fulfil the ATEX fire and explosion protection regulations, the drive unit of the spiral conveyor was positioned outside the wood chip depot. The control unit for the conveyor section and the monitoring of the bunker fill level were also designed in line with the ATEX regulations.
I would definitely recommend UNTHA to others as I appreciate the expertise and experience that comes from looking after customers in the timber industry for so many years. Then there is also the robust design of the LR1000, which makes this shredder so long-lasting and sustainable.
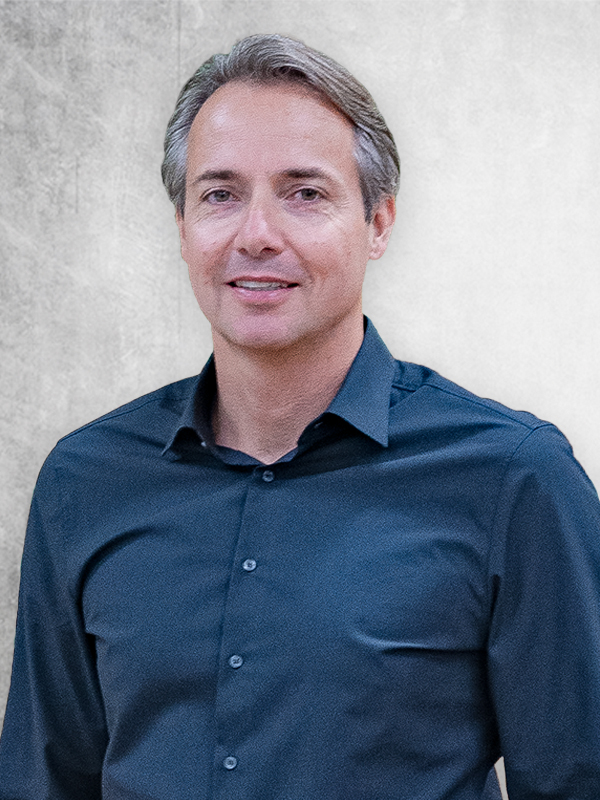
Karl Schmiederer
Managing Partner
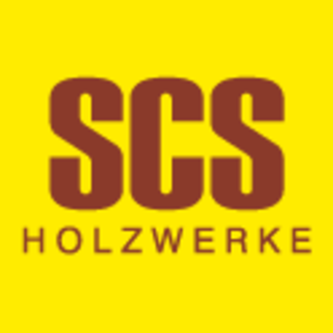
UNTHA supplied SCS with a bespoke, complete solution, consisting of the shredder and its conveyor technology. The concept was developed in close cooperation between the two companies. All the components were perfectly coordinated with one another and the requirements of the wood chip system.For SCS, this shredder solution ticks all the boxes: energy efficiency, a high throughput, and fault-free, user-friendly operation.
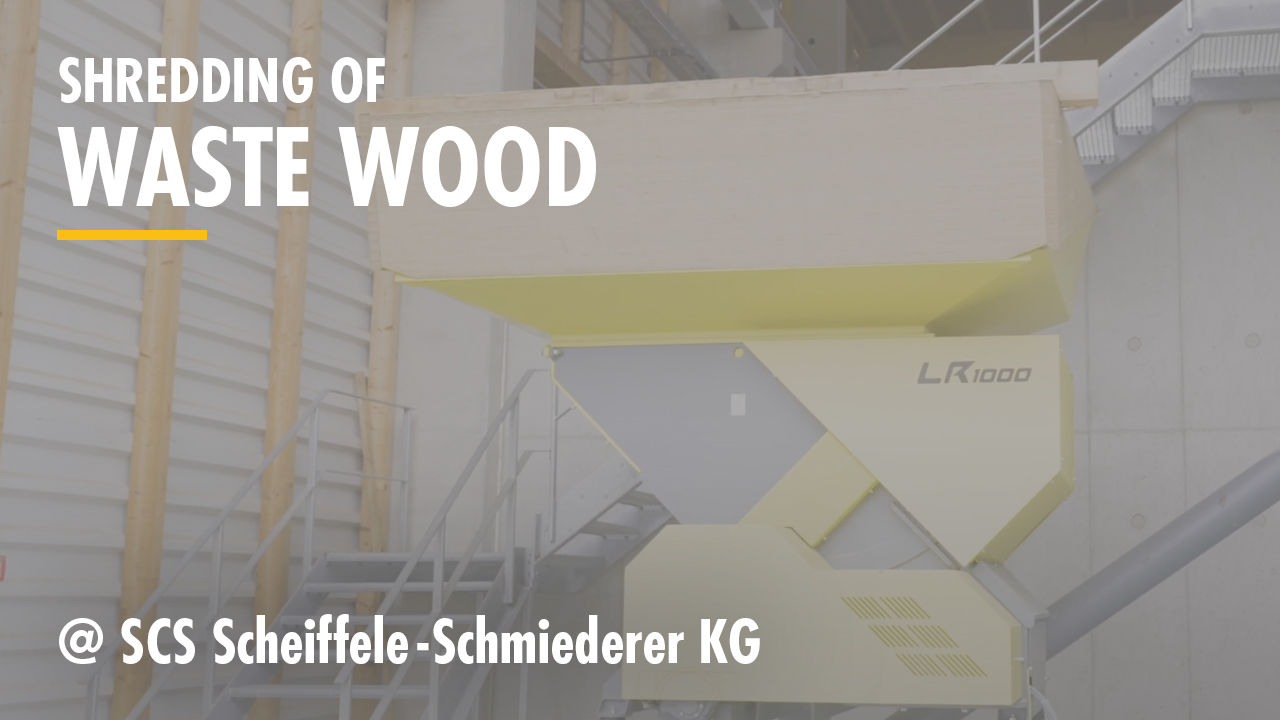