MyUNTHA customer portal - Make your business easier
On MyUNTHA you will find everything you need for your shredder. The customer portal offers you extensive benefits, digital services and an intelligent assistance system. You can also contact UNTHA directly here.
Once you have registered in the portal, you can manage all your shredders, order suitable spare parts and purchase licences for your machines.
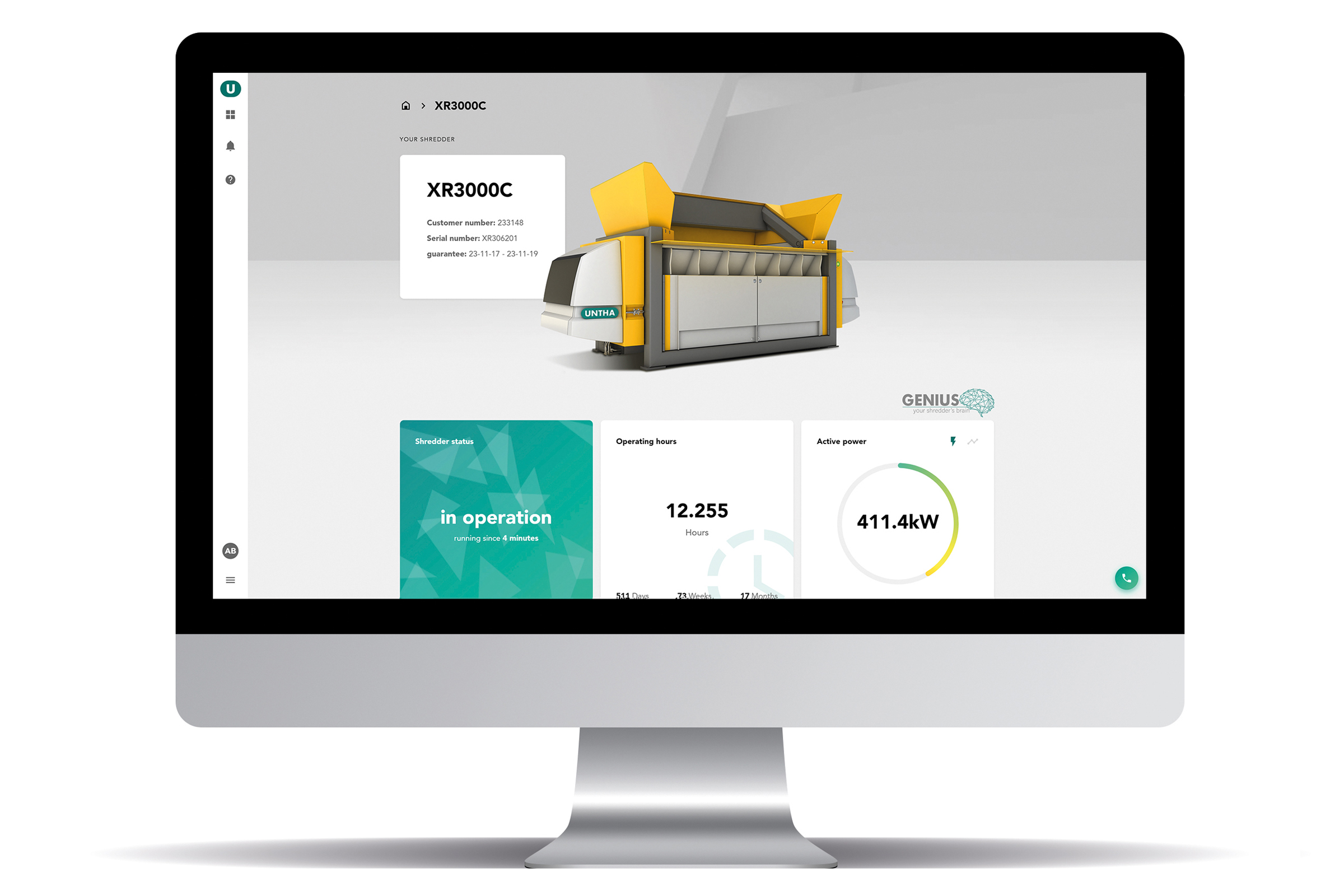
Access to all available documents such as spare parts and service documentation as well as operating instructions for your shredder. It is also possible to access video instructions and service image galleries
Order the required spare parts, consumables and accessories conveniently and without long waiting times
Overview of your customer data and authorisations, which you can change and expand at any time
You register once in the MyUNTHA customer portal and have access to all your UNTHA data: Information about your shredders, automatic notifications in the event of deviations, operating data and the web shop for accessories and spare parts. With MyUNTHA, we support you in your daily work and handling of UNTHA shredders, true to the motto "make your business easier".
Register now and test all features without any costs.
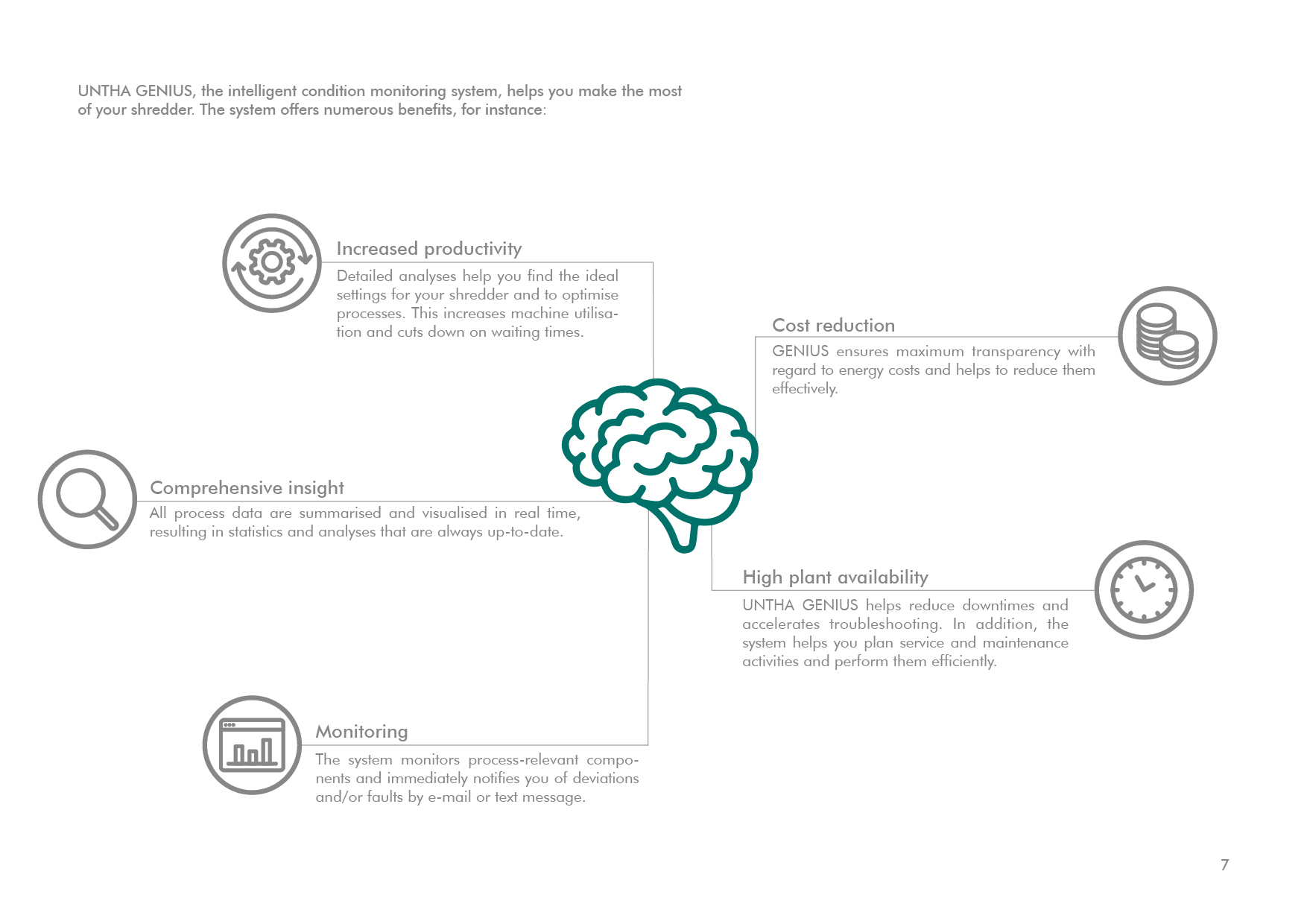
UNTHA GENIUS is an intelligent condition monitoring tool for your shredder. With the help of reliable sensor technology, the operation of your machine is monitored on an ongoing basis. UNTHA GENIUS processes your data in real time, alerts you of any deviations and delivers analyses and decision support. The reports are delivered automatically, via e-mail, either on a daily or a weekly basis. On the dashboard, the machine status and the process data are shown. You may also access the complete machine documentation. In case of deviations or faults, you will be informed immediately. In the Data Explorer, you have the option of drawing up detailed analyses of process values, for instance over a period of several days or weeks. These may then be used as support for optimisation.
The UNTHA GENIUS assistance system automatically informs our employees by e-mail or text message as soon as the shredder can be loaded again. We can easily manage the notifications and adjust settings via MyUNTHA. This smart function is now an integral part of our internal processes and helps us to save time and money and make our day-to-day work easier.
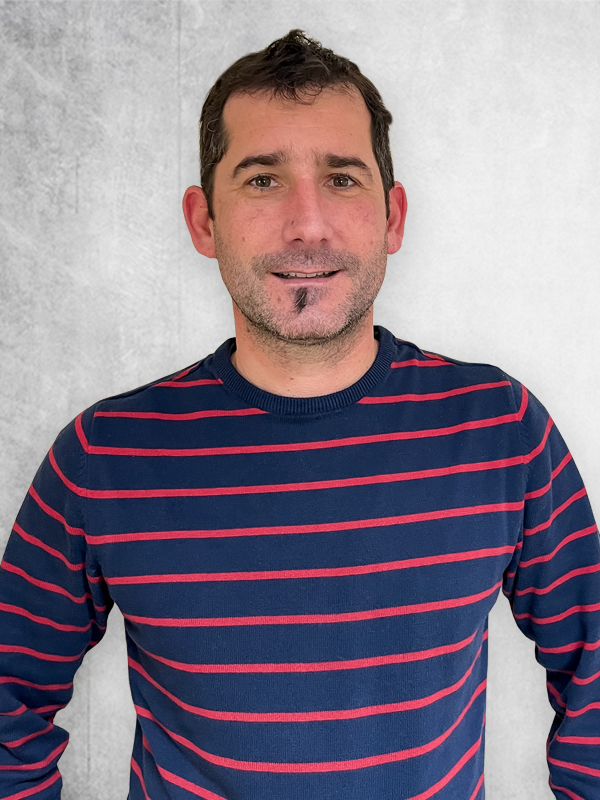
Markus Quirchmair
Deputy Head of Commodity Manipulation
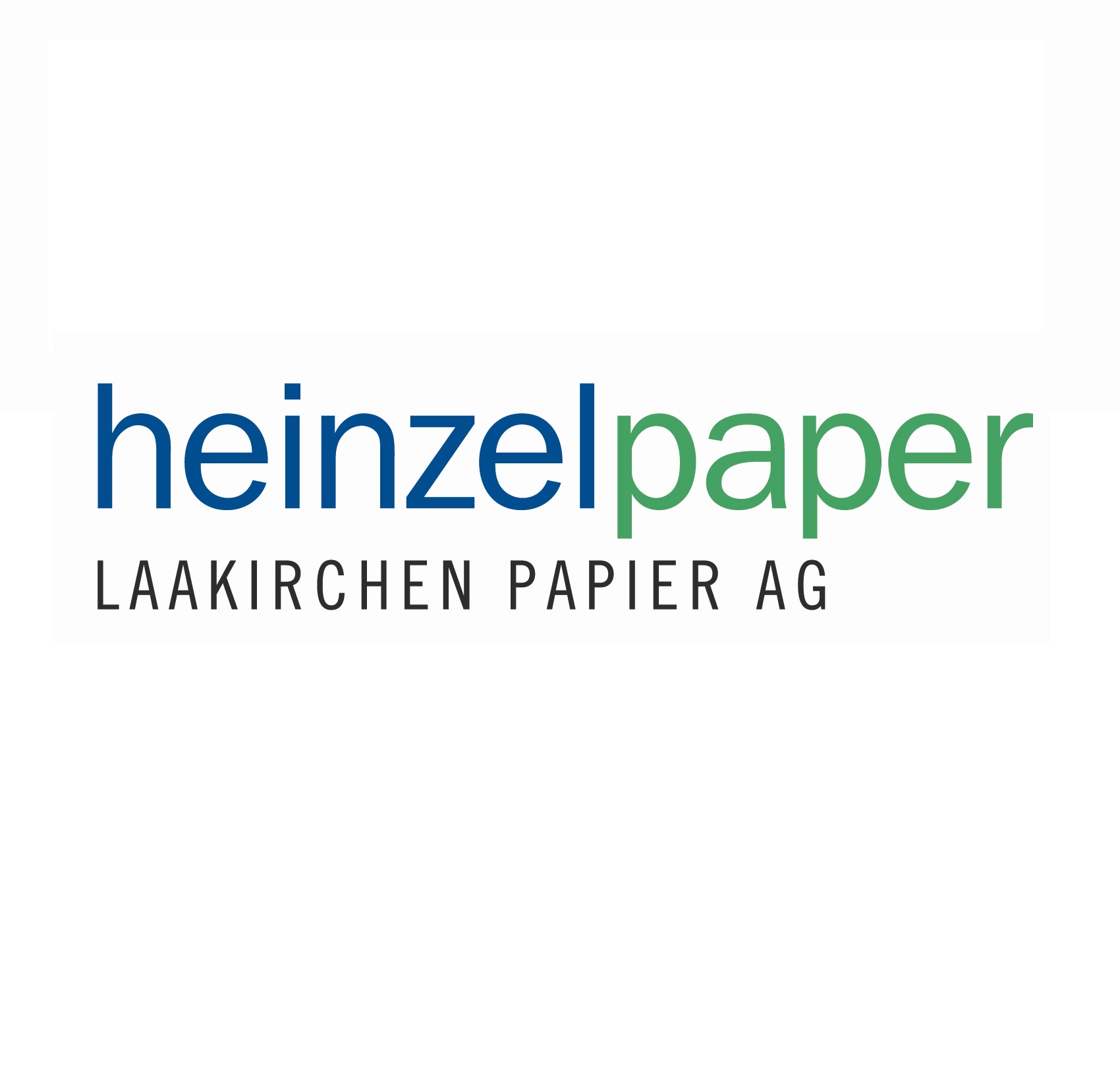
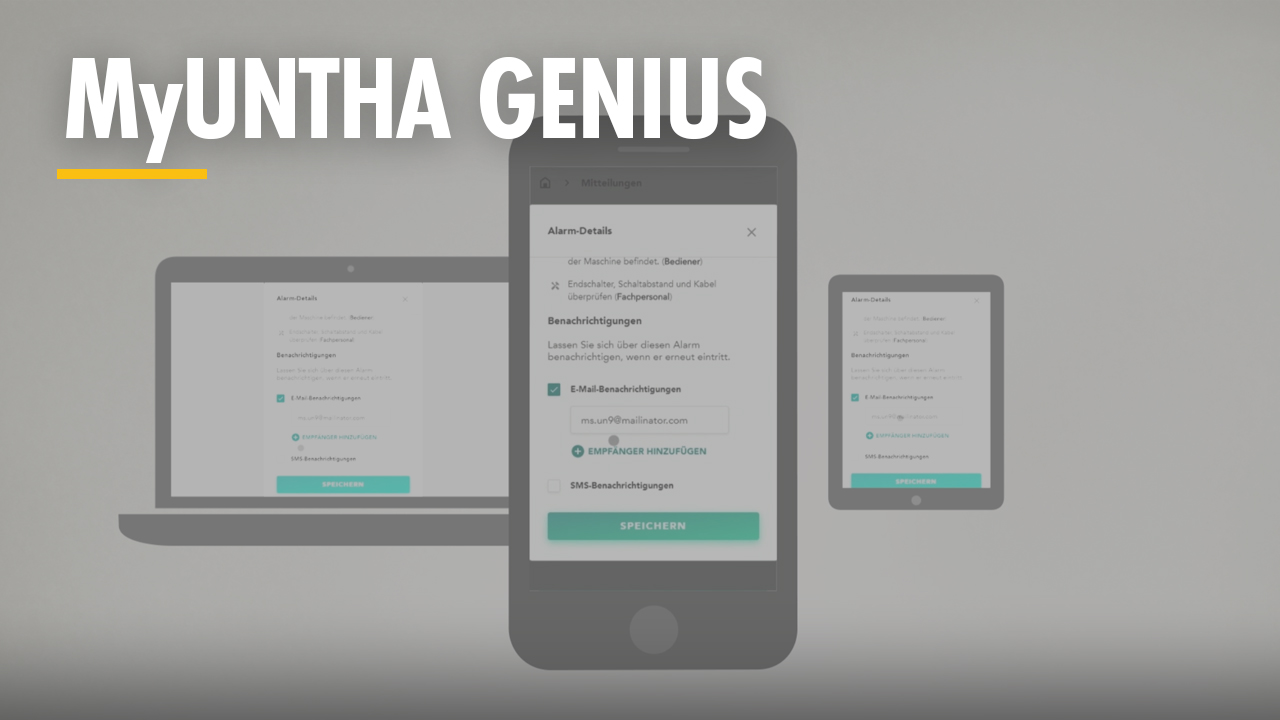
UNTHA GENIUS, the intelligent condition monitoring system, helps you make the most of your shredder. The system offers numerous benefits, for instance:
Increased productivity: Detailed analyses help you find the ideal settings for your shredder and to optimise processes. This increases machine utilisation and cuts down on waiting times.
Comprehensive insight: All process data are summarised and visualised in real time, resulting in statistics and analyses that are always up-to-date.
Monitoring: The system monitors process-relevant components and immediately notifies you of deviations and/or faults by e-mail or text message.
Cost reduction: GENIUS ensures maximum transparency with regard to energy costs and helps to reduce them effectively.
High plant availability: UNTHA GENIUS helps reduce downtimes and accelerates troubleshooting. In addition, the system helps you plan service and maintenance activities and perform them efficiently.
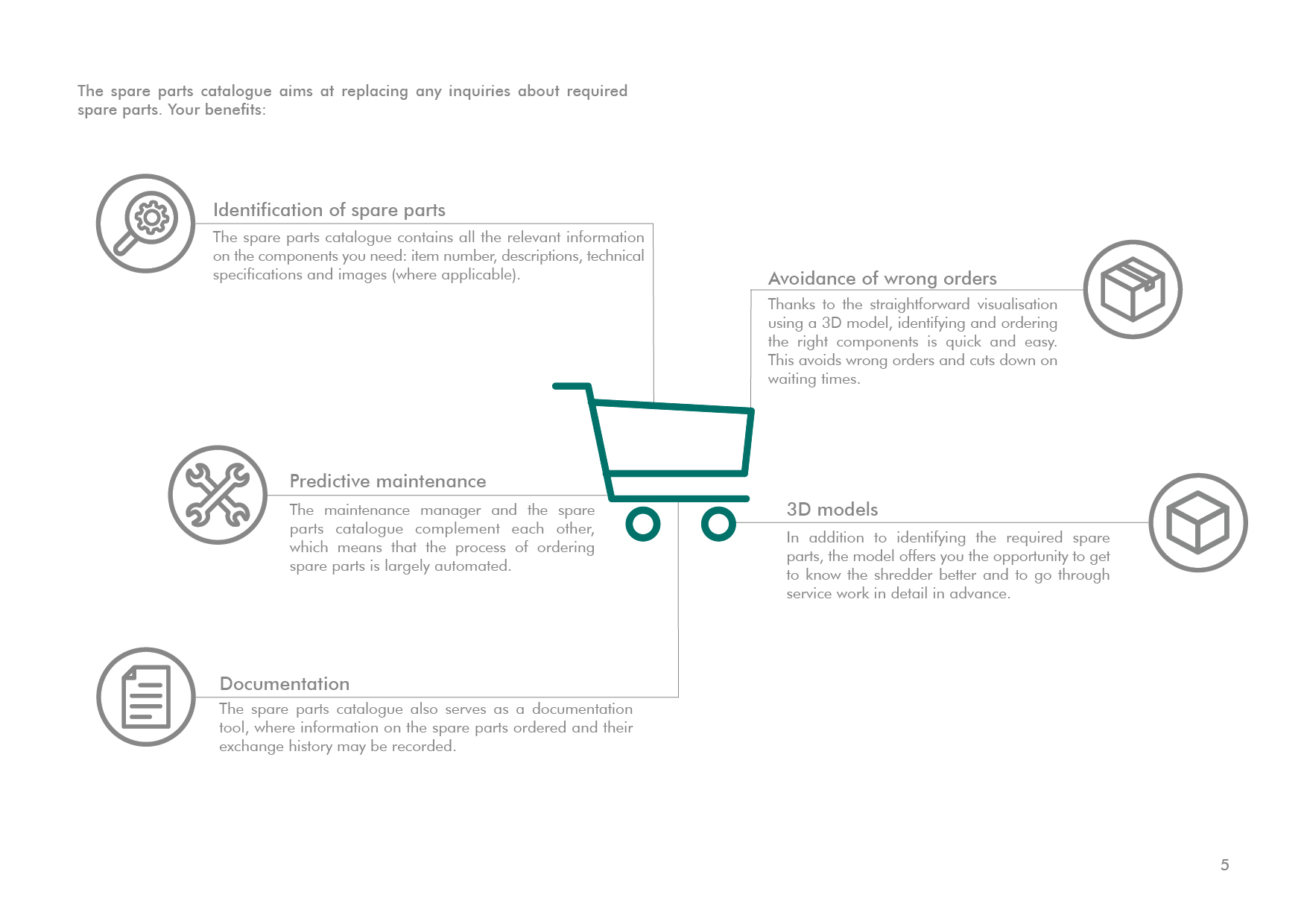
UNTHA shredder consists of a multitude of individual parts. High-stress components are especially subject to natural wear. To make it as easy as possible to find the spare parts you need, the spare parts catalogue provides you with a 3D model of your shredder. This contains all the information you need for identifying individual components and finding the right wear components and spare parts. The parts may be ordered from the integrated online shop with just a few clicks.
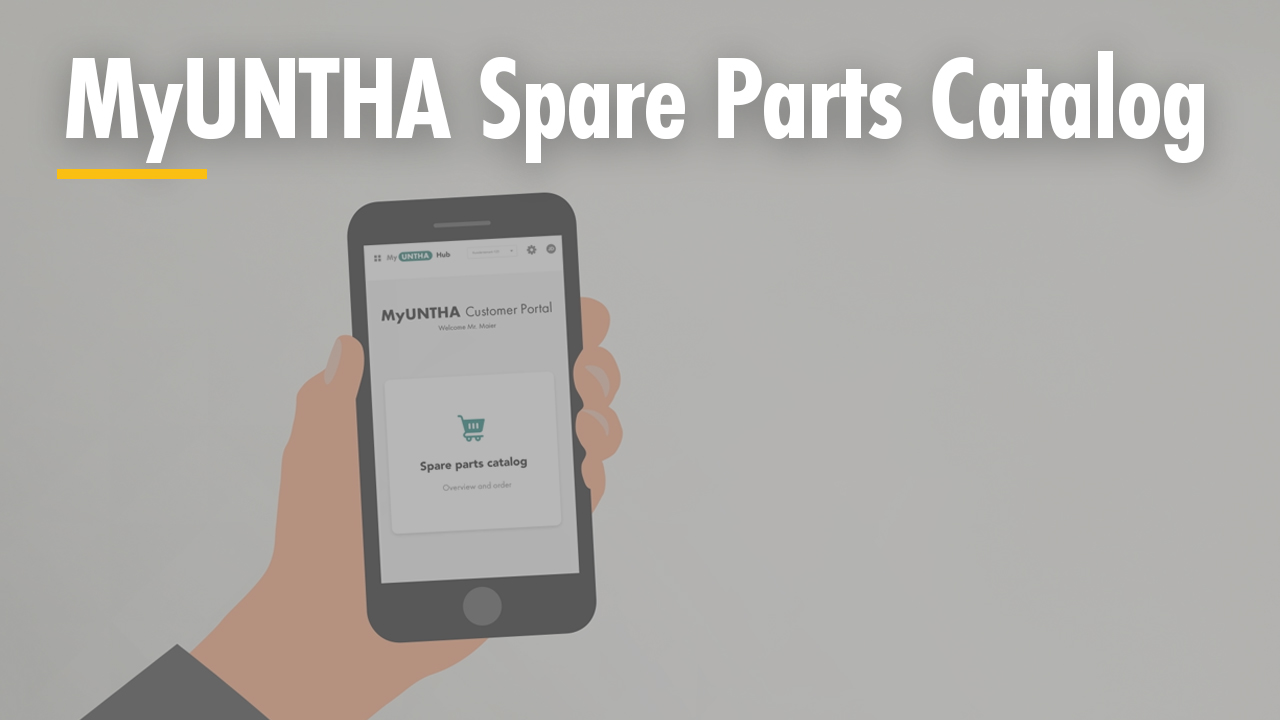
You can use the spare parts catalogue & online shop to process all enquiries about the spare parts you need. This results in the following advantages, among others:
3D models: Find the right parts visually.
Detailed information: Part numbers, technical specifications and more.
Service instructions: Assistance for the replacement of spare parts.
Avoid incorrect orders: Clear presentation and easy ordering.
Planning reliability: Fast delivery reduces waiting times.
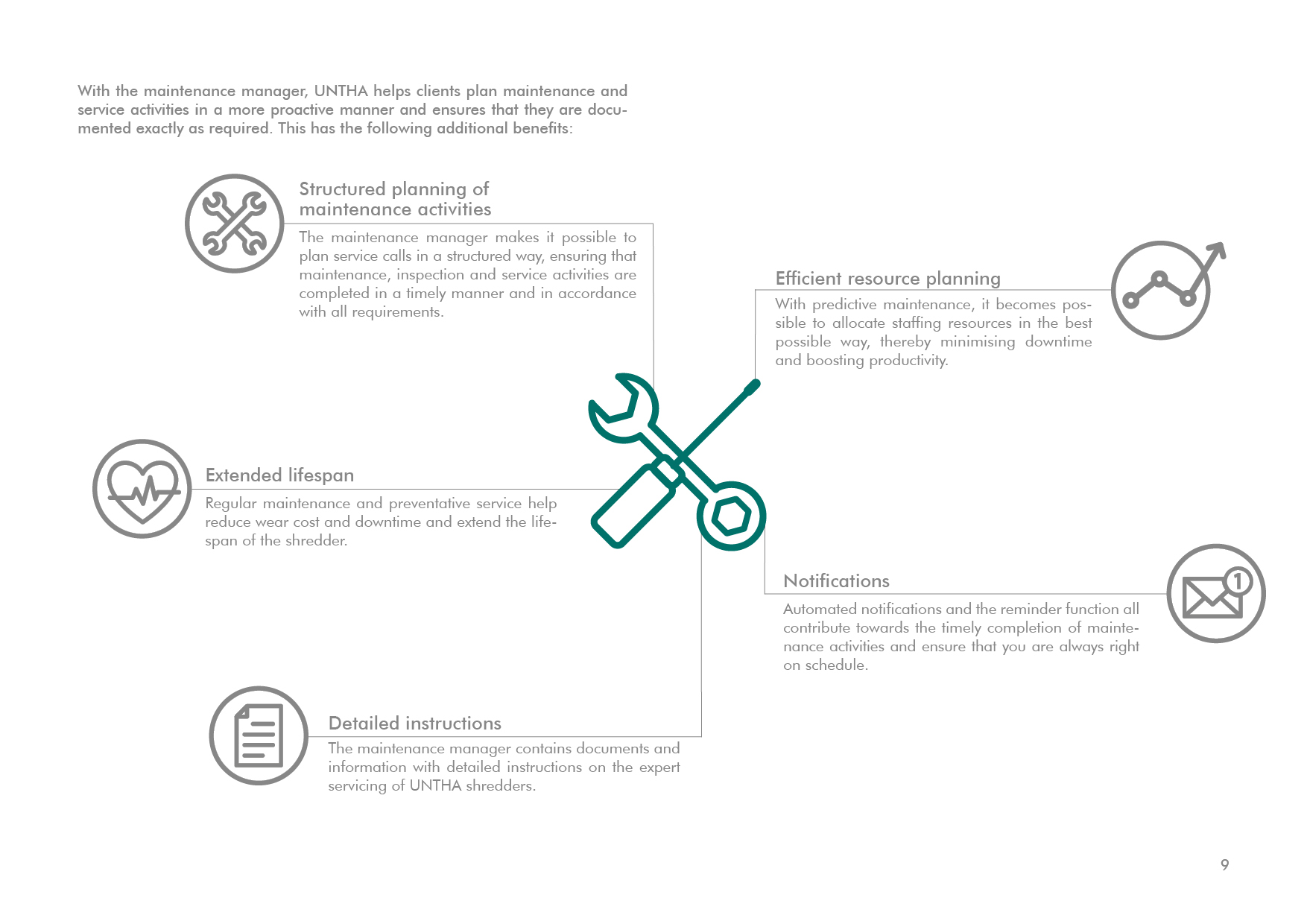
The maintenance manager supports you with planning and carrying out regular maintenance and inspection activities, as well as preventative maintenance. The system informs you in good time and helps you find the right window for carrying out maintenance works. This way, you can plan for them in your workflows and avoid excessive downtime. Regular maintenance helps increase your shredder’s lifespan and ensures its reliability, thus contributing to keeping operating costs to a minimum. The maintenance manager also provides you with any instructions you will need. The performed activities are documented and archived there, and the integrated logbook supports traceability and serves as evidence in case of warranty claims.
The maintenance manager in MyUNTHA makes it much easier for us to plan and carry out maintenance work. Thanks to the detailed instructions, we save a lot of time and can ensure that everything runs smoothly. We also have clean digital documentation in the platform that all authorized users can access at any time. This also allows us to dispense with paper maintenance plans.
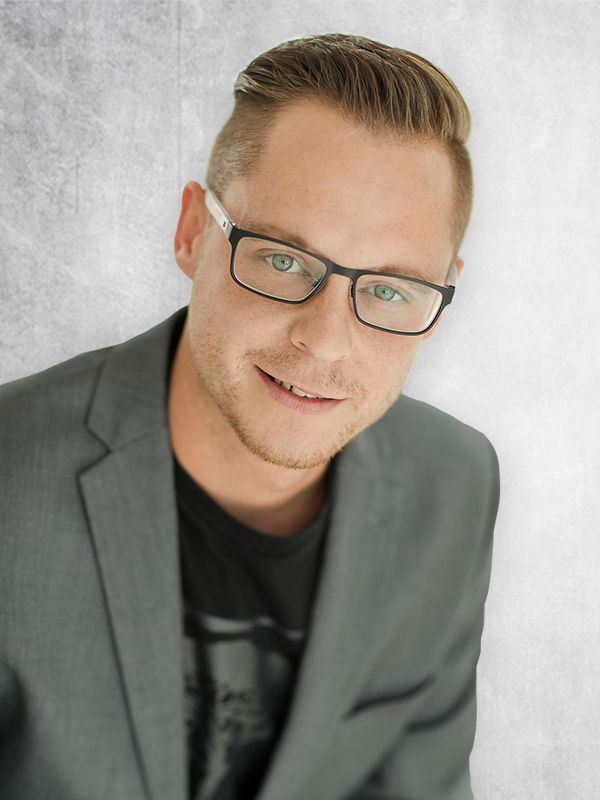
André Riemer
Operations manager
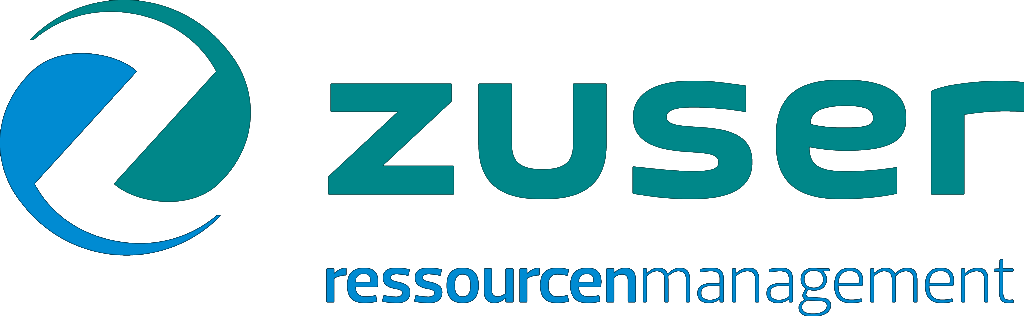
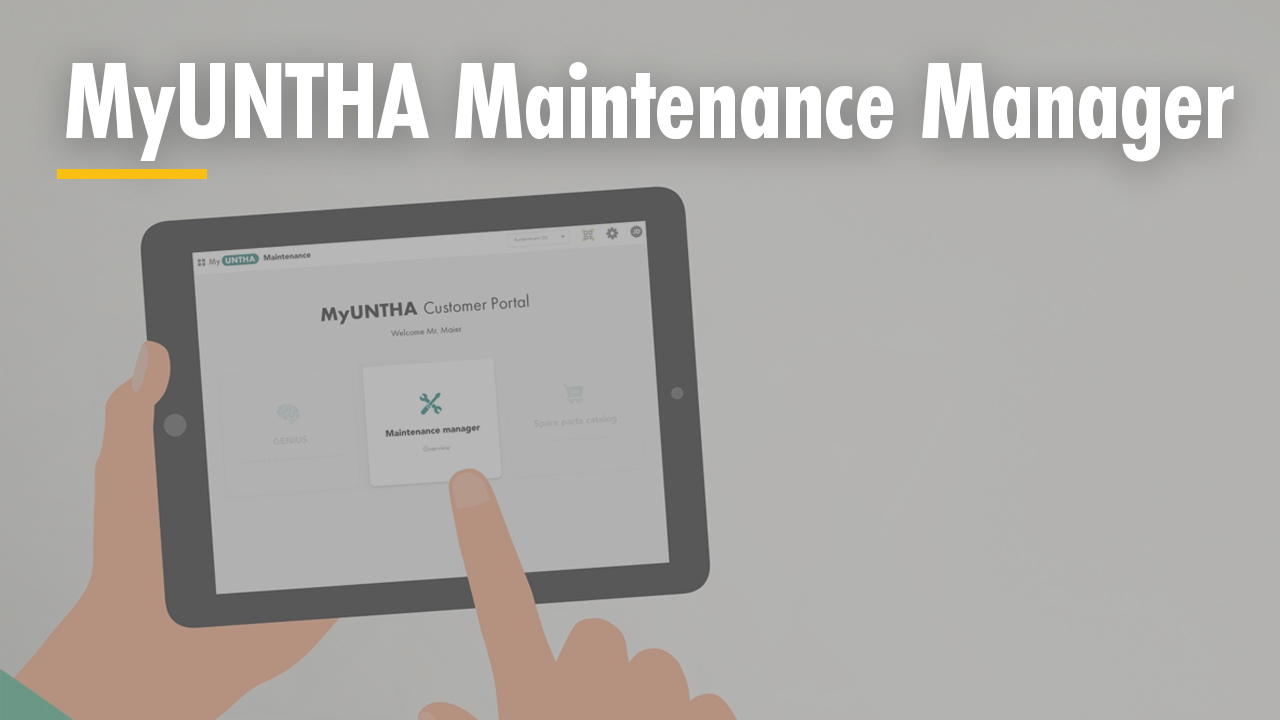
With the maintenance manager, UNTHA helps clients plan maintenance and service activities in a more proactive manner and ensures that they are documented exactly as required. This has the following additional benefits:
Structured planning of maintenance activities: The maintenance manager makes it possible to plan service calls in a structured way, ensuring that maintenance, inspection and service activities are completed in a timely manner and in accordance with all requirements.
Extended lifespan: Regular maintenance and preventative service help reduce wear cost and downtime and extend the lifespan of the shredder.
Detailed instructions: The maintenance manager contains documents and information with detailed instructions on the expert servicing of UNTHA shredders.
Efficient resource planning: With predictive maintenance, it becomes possible to allocate staffing resources in the best possible way, thereby minimising downtime and boosting productivity.
Notifications: Automated notifications and the reminder function all contribute towards the timely completion of maintenance activities and ensure that you are always right on schedule.
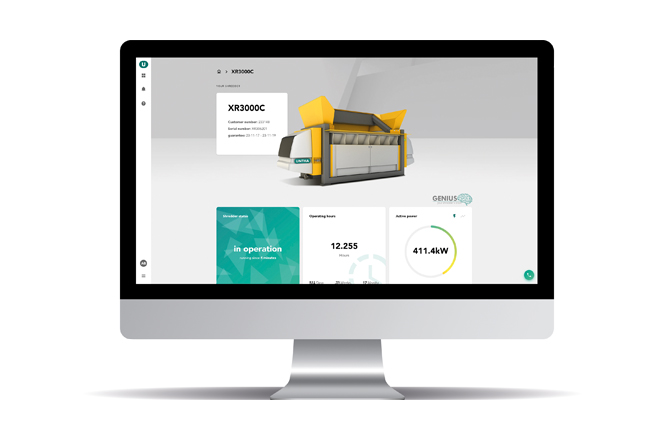
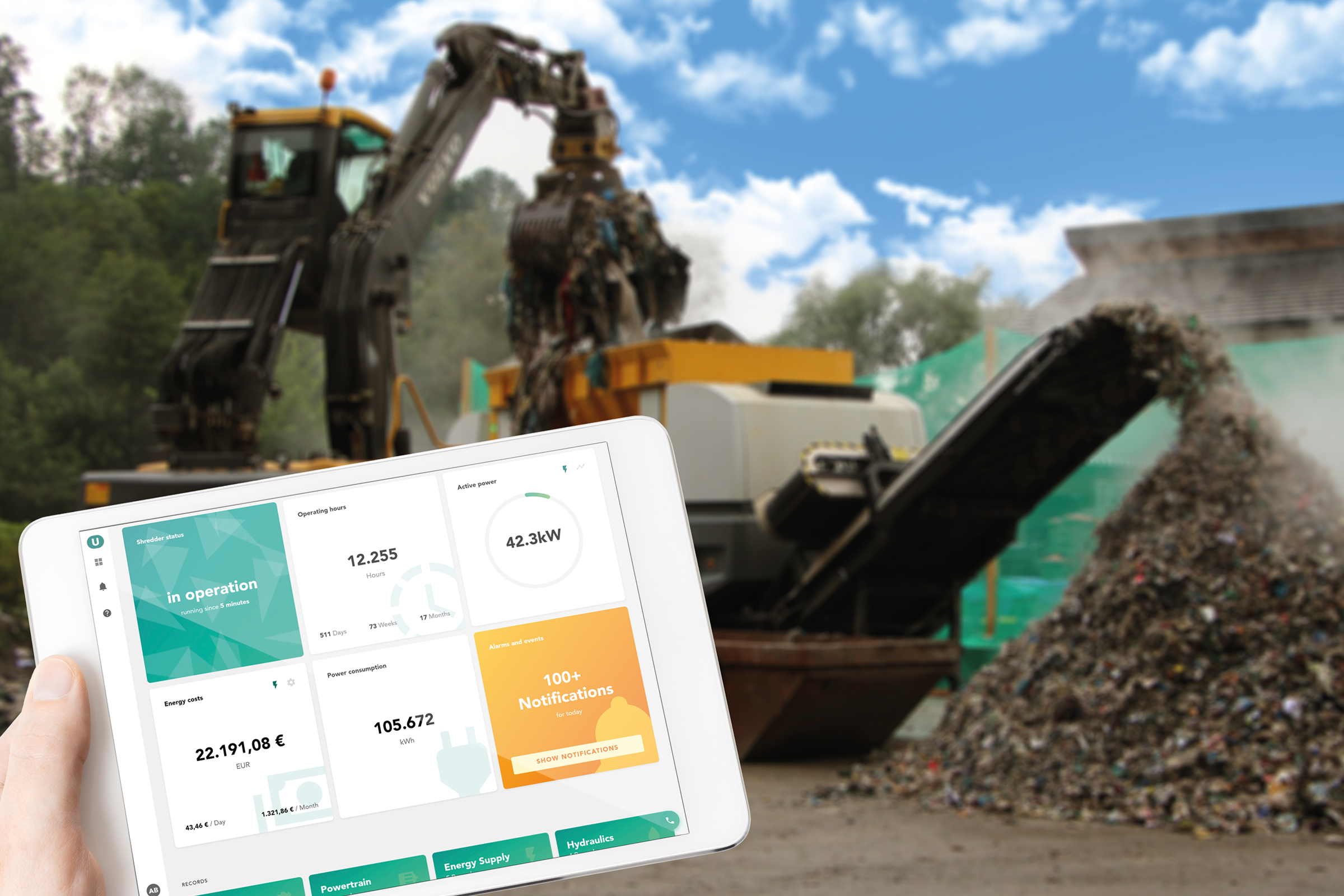
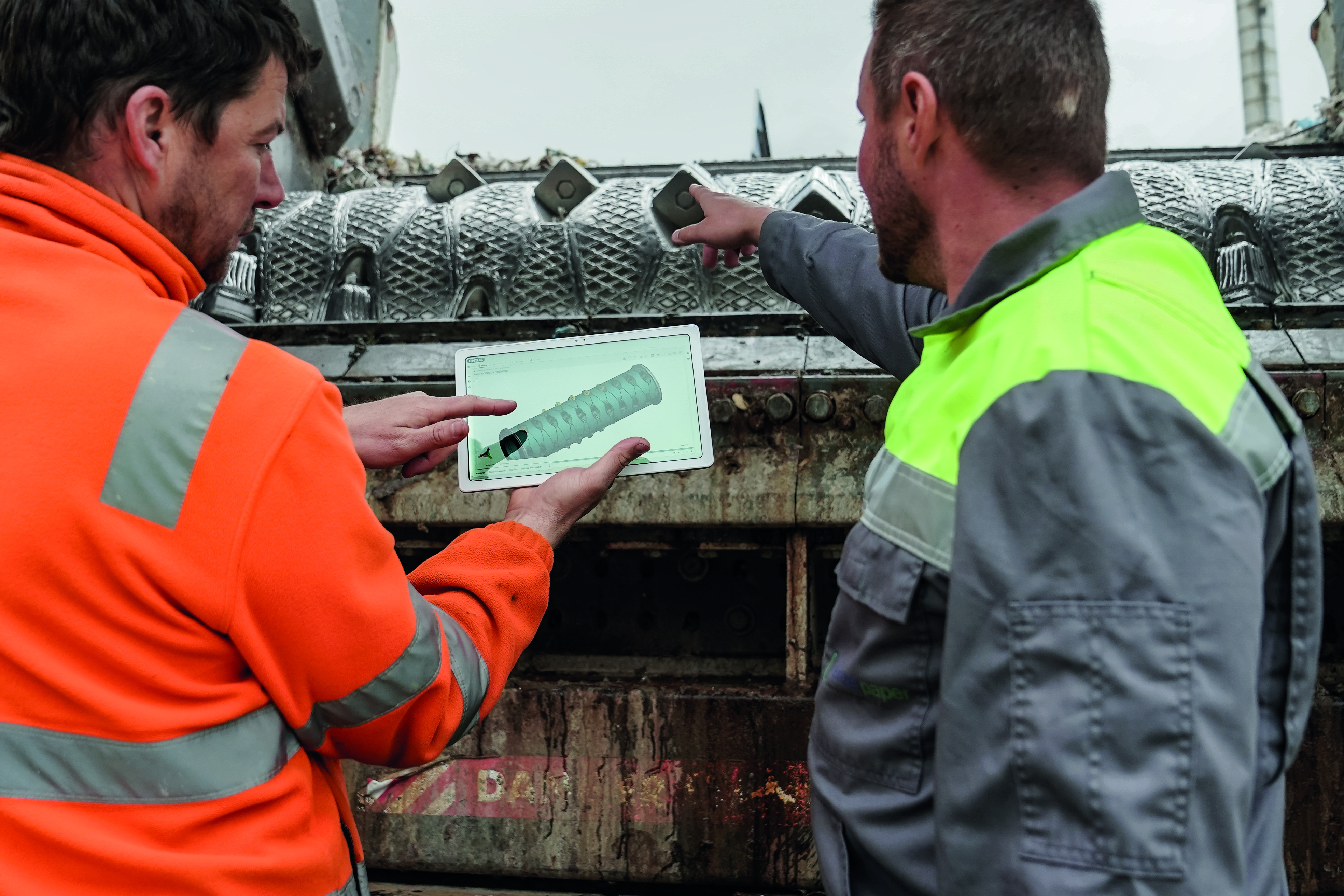
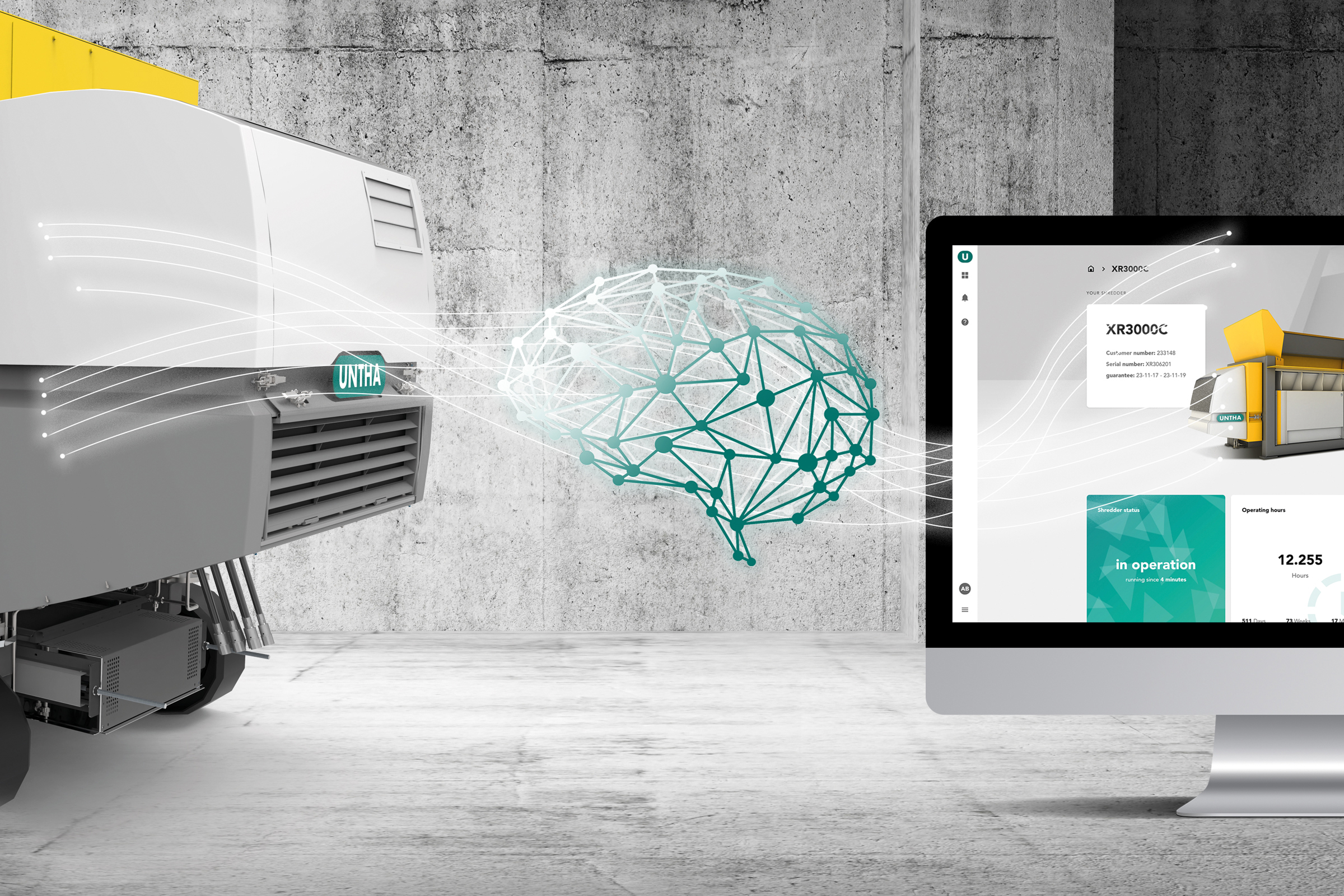
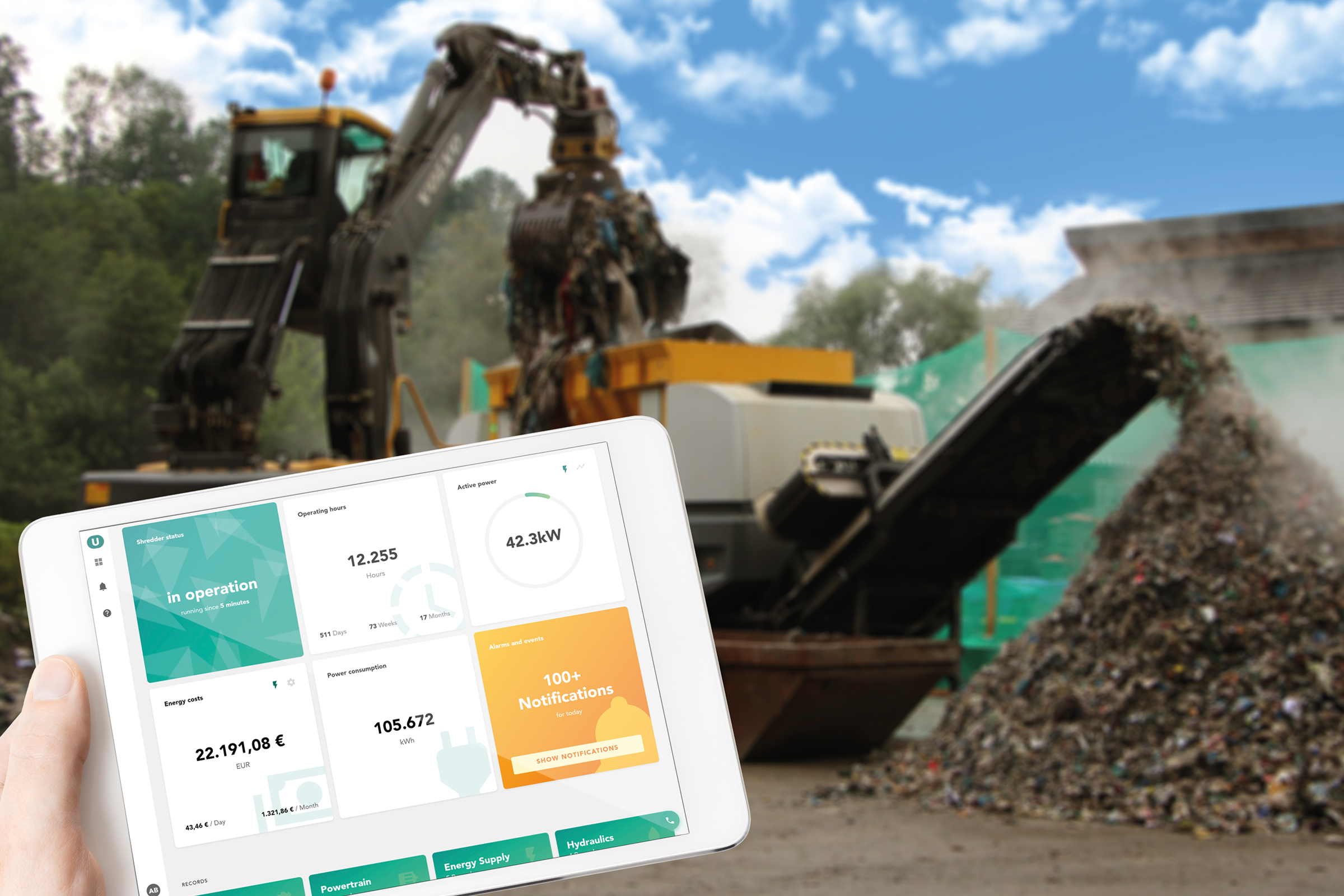
MyUNTHA is a customer portal that can be accessed via any Internet-enabled device (smartphone, tablet, notebook, etc.) at the following address: www.myuntha.com/login.
You register once in the MyUNTHA customer portal and have access to all your UNTHA data: Information about your shredders, automatic notifications in the event of deviations, operating data and the web shop for accessories and spare parts. With MyUNTHA, we support you in your daily work and handling of UNTHA shredders, true to the motto "make your business easier".
Register now and test all features without any costs.