Zuser Ressourcenmanagement relies on innovative technologies to reduce CO2 emissions
Environmental protection and the reduction of CO2 emissions are core issues for the Zuser Group. At the Zuser Ressourcenmanagement GmbH site in Peggau, Styria, extensive investments have been made to make the company even more sustainable: large-scale photovoltaic systems, e-mobility and energy-efficient shredding technology. Zuser uses UNTHA shredders to produce high-quality refuse derived fuel – the use of which saves fossil fuels.
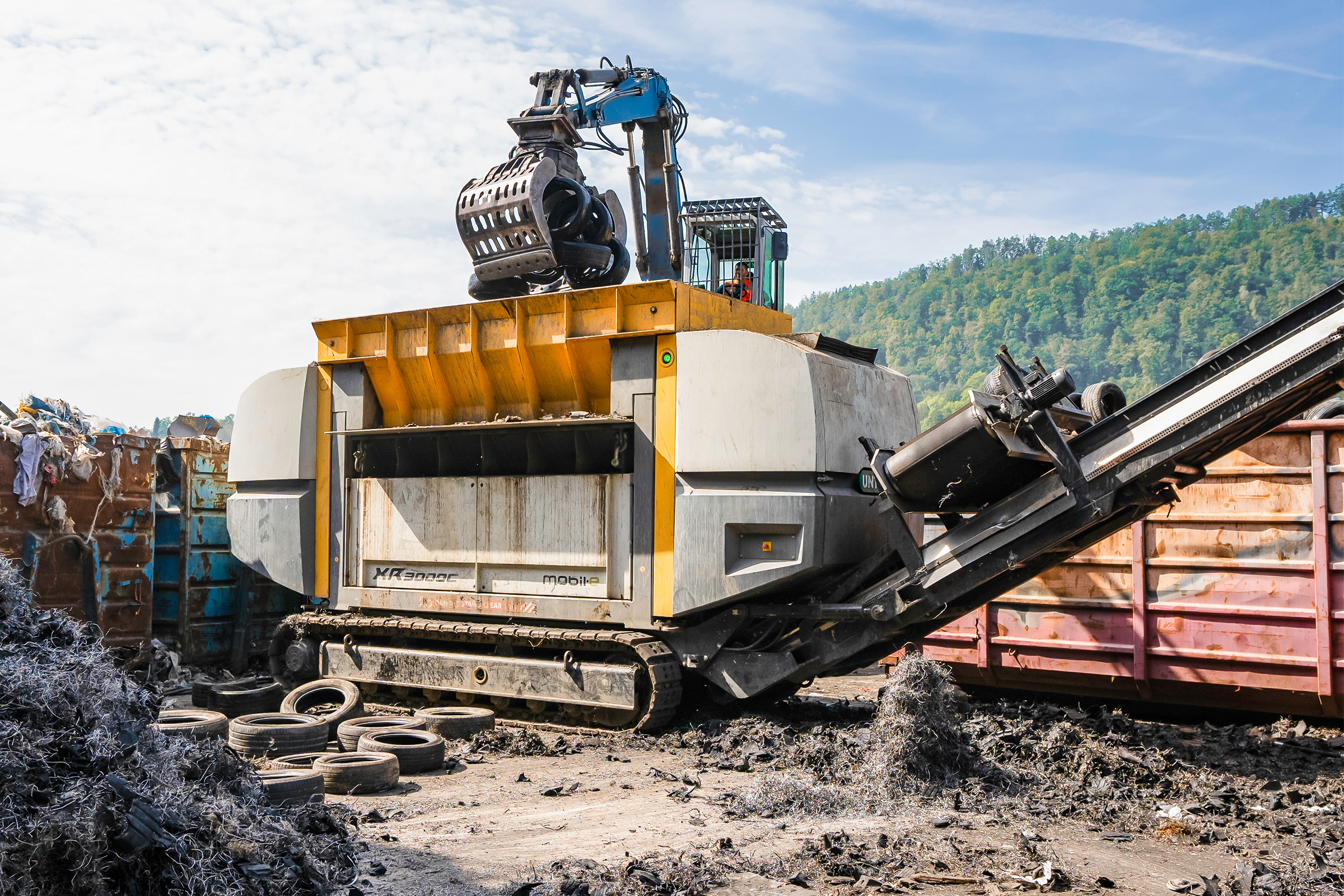
Zuser Ressourcenmanagement GmbH produces over 100,000 tons of substitute fuels (RDF) with a high energy content and degree of purity every year. The materials processed include commercial waste, lightweight packaging, used tires and rubber. Another focus is material recycling. The company sorts high-quality plastics such as PET and films as well as ferrous and non-ferrous metals from the waste and ensures that they are returned to the material cycle. The waste materials are processed using two UNTHA shredders: "The UNTHA XR3000RC mobil-e and XR3000C mobil-e shredders are energy-efficient, ensure high throughput rates and a homogeneous source material. They can be used flexibly: thanks to different perforated screens and sieve bars, they are suitable for shredding various materials. Thanks to the electric crawler-type undercarriage, the shredders can be moved to different locations and connected with just one plug," says André Riemer, Head of Processing Technology at Zuser Ressourcenmanagement GmbH, about the two UNTHA shredders.
Efficient shredding technology
Zuser Ressourcenmanagement has been relying on UNTHA for years. The selection criteria for the latest shredders for the site in Peggau included Energy efficiency, electric drive, high throughput and a homogeneous source material. Materials such as lightweight packaging and commercial waste as well as used tires and rubber are processed. The XR model series from UNTHA is ideally suited to these applications: single-shaft shredders with a particularly high throughput rate and an economical drive. The low-speed UNTHA Eco Power Drive consumes up to 75 percent less energy than comparable diesel-powered shredders. A magnetic separator above the discharge conveyor sorts out metals, which are then recycled. Thanks to the electrically powered crawler-type undercarriage, the shredder can also be used at other locations on the company premises, ensuring 100% system availability. The cutting units and the perforated screens and bars used differ depending on the material and recycling purpose:
RC cutting system (Ripper-Cutter):
Coarse shredding of various materials, such as commercial waste and lightweight packaging.
The special tooth shape ensures optimum feed of the material. This eliminates the need for an additional pressure system and the cutting chamber is larger, enabling higher throughput rates (up to 70 t/h).
Depending on the perforated screen used, fraction sizes between 90 and 300 mm are possible.
C cutting system (Cutter):
Perfect for single-step processing of challenging materials, such as used tires and rubber, to a fraction size of 45 to 130 mm – depending on the perforated screen used.
Up to four rows of knives ensure high throughput rates.
The cutting plates are reversible and can be reused up to four times.
Images for download (Reprint free of charge for press purposes, photo credits: UNTHA shredding technology GmbH): https://untha.canto.de/b/O1AQ3
Image 1-3: The UNTHA XR3000RC mobil-e shreds around 18 tons of lightweight packaging and commercial waste per hour at Zuser Ressourcenmanagement
Image 4: Tire shredding with a UNTHA XR3000C mobil-e: up to 10 tons of material are shredded per hour