References
Karl Karletshofer GmbH, based in Neu-Ulm/Bavaria, is one of southern Germany's leading medium-sized companies in the trade and storage of ferrous and electronic scrap and non-ferrous metals. Among other things, the company supplies primary and secondary smelting plants with high-quality processed metals and, through its work, contributes to returning raw materials to the material cycle.
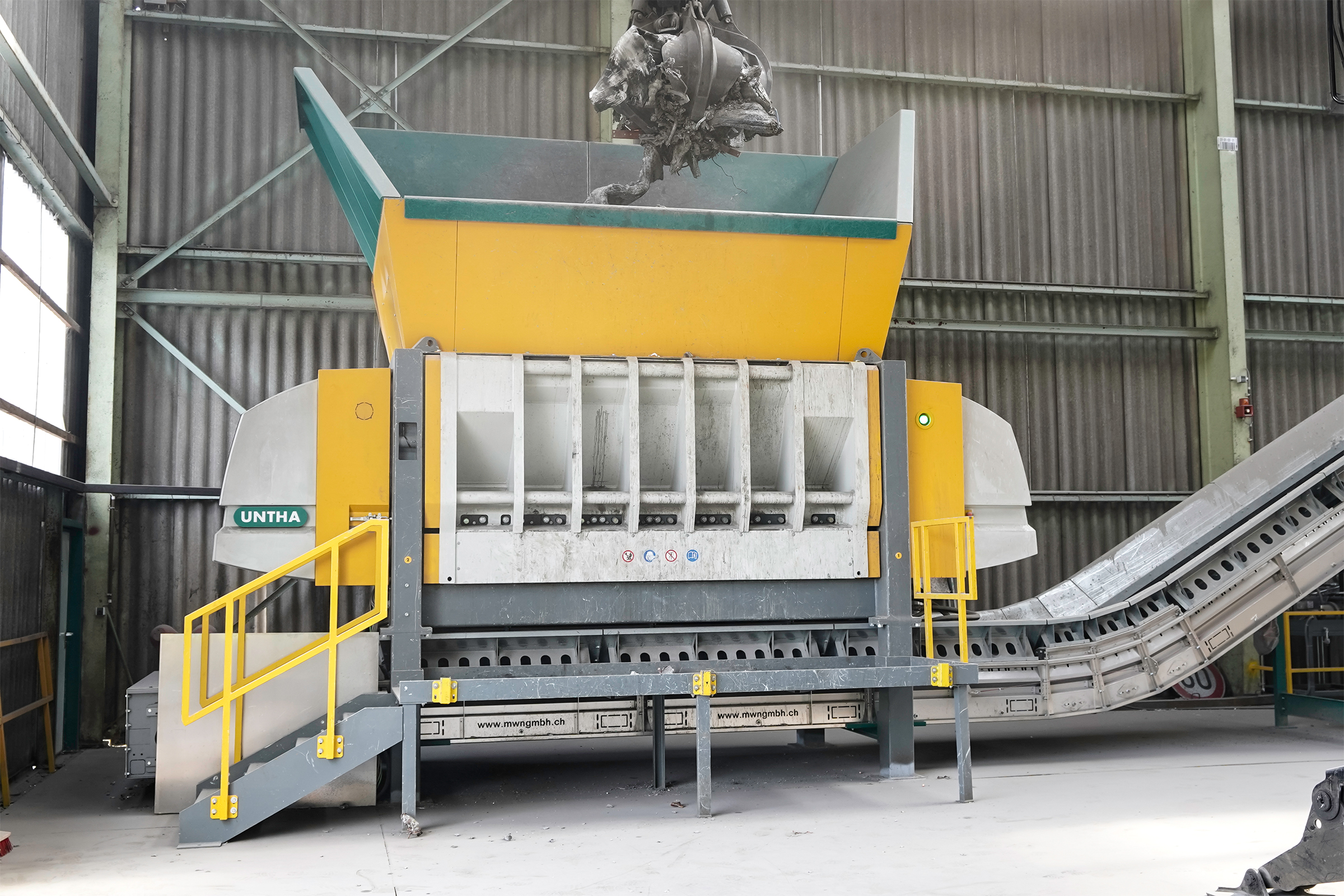
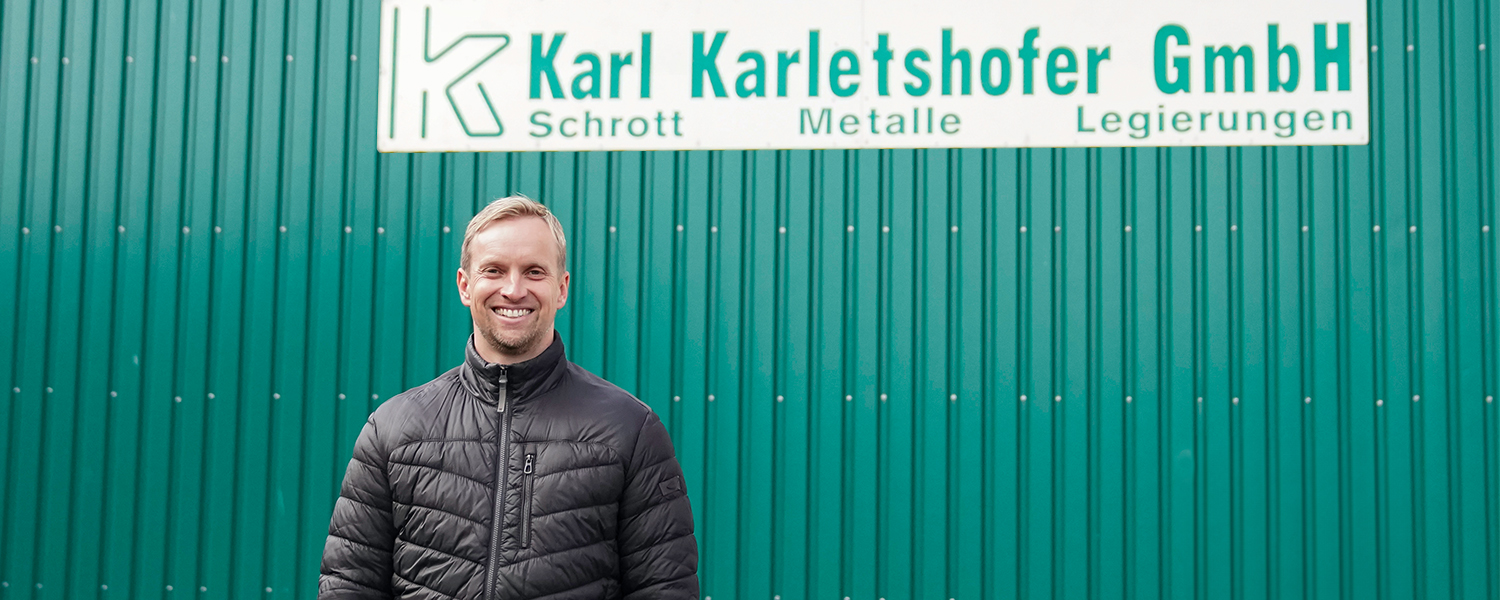
As one of southern Germany's leading metal wholesalers, Karl Karletshofer GmbH specialises in the processing of ferrous scrap, various metals from production plants and the wholesale trade, as well as electronic scrap. The aim is to process these materials accordingly in order to provide processing companies with pure raw materials for recycling.
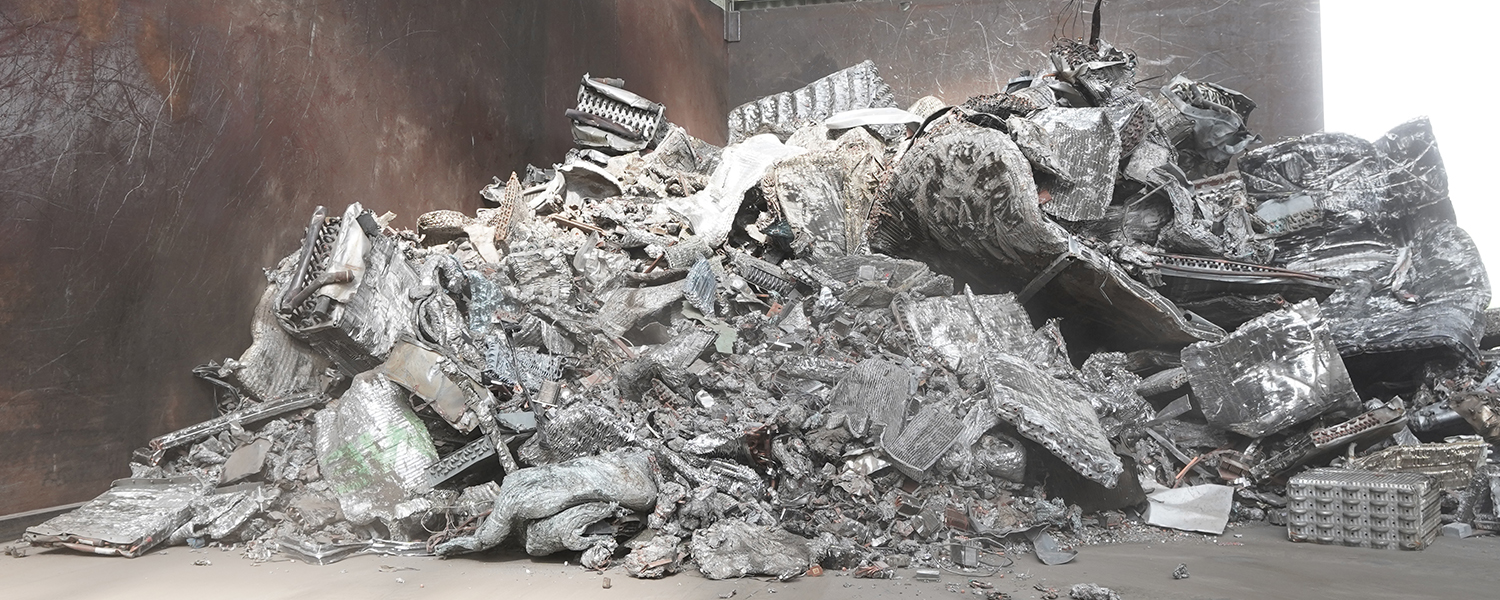
At Karl Karletshofer GmbH, metals of different types are shredded and then separated into different material streams using a sorting system. This required a shredder that would always produce a homogeneous and easily sortable output material, even with materials of different compositions. Particularly relevant criteria were therefore the customisability of the shredder to the material and an energy-efficient drive.
REQUIREMENTS
Good material disintegration
Energy efficiency
Adjustable cutting gap
Homogeneous output material
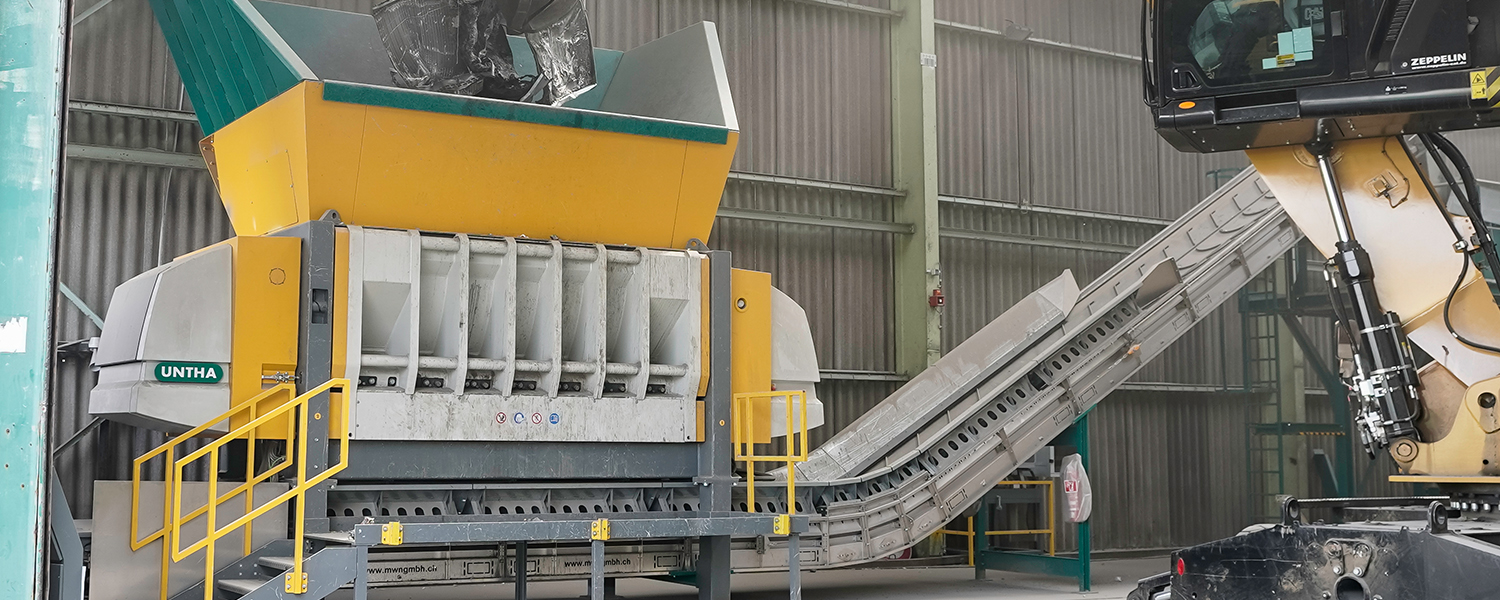
A UNTHA XR3000C is in operation at Karl Karletshofer GmbH. This single-shaft shredder is driven by a water-cooled synchronous motor, the UNTHA Eco Power Drive, making it particularly powerful and energy-efficient at the same time. Depending on the material composition, size and thickness, adjustments can be made to the shredder: The cutting gap and operating programme can be set individually, and different perforated screens can be replaced using a quick-change system. This ensures that the material is always shredded to the desired granulate size and that processes run efficiently. Two rows of knives in conjunction with the 130 mm perforated screen ensure that metal parts are shredded to a fraction size of approx. 130 mm. The throughput rate is around 6-12 tonnes per hour – depending on the input material.
Thanks to the UNTHA XR3000C, we were able to add another service to our portfolio: by reliably shredding different metals, we can provide our customers with pure raw materials that are ideal for recycling.
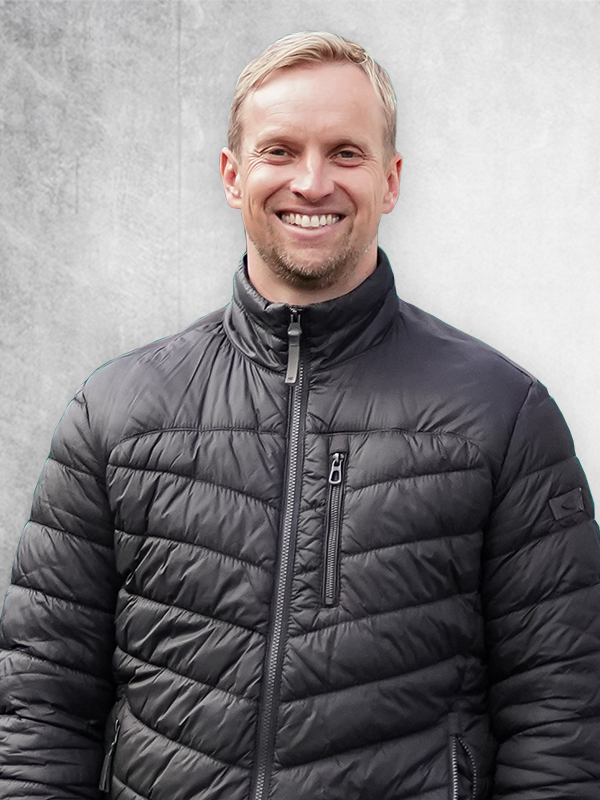
Clemens Karletshofer
Managing Director
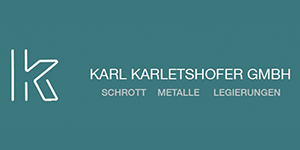
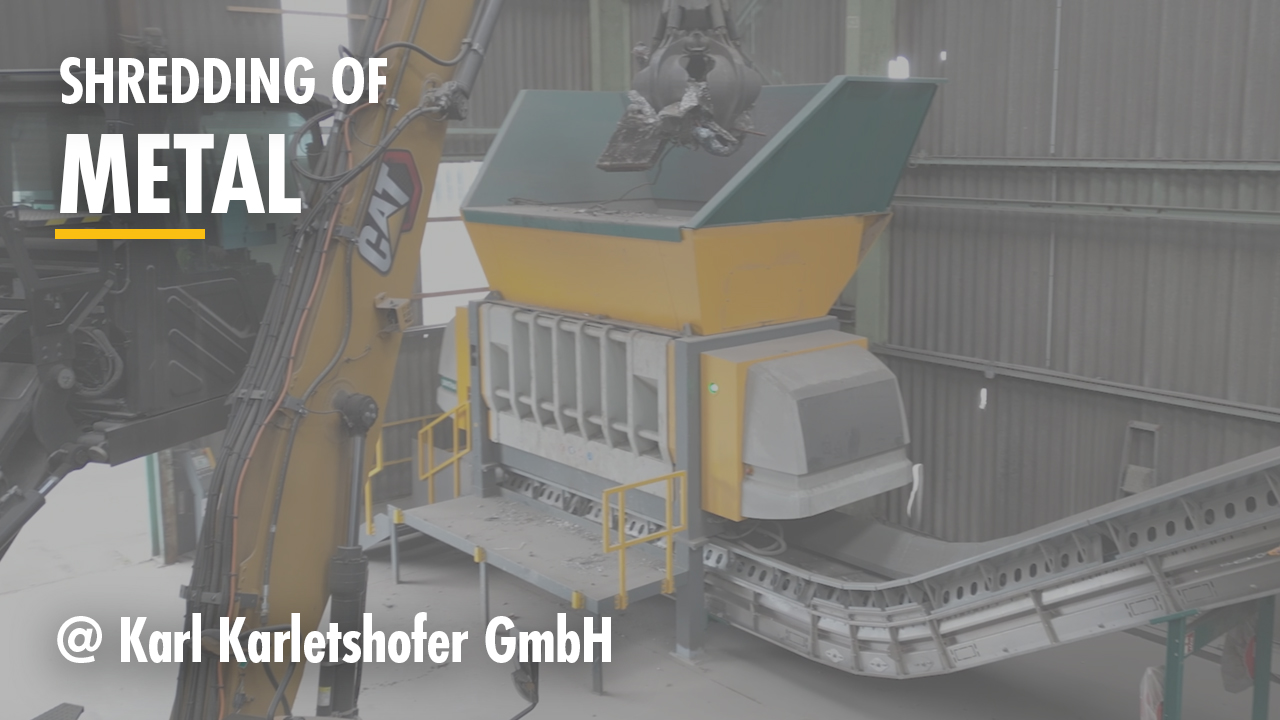