References
Laakirchen Papier AG is part of the internationally active Heinzel Group and one of Europe’s leading manufacturers of environmentally friendly publication and packaging paper, with an annual production volume of more than 780,000 tonnes. The company sets great store by using natural resources responsibly: Its production facilities reuse 800,000 tonnes of wastepaper a year, and any other waste is recycled or used for thermal recovery.
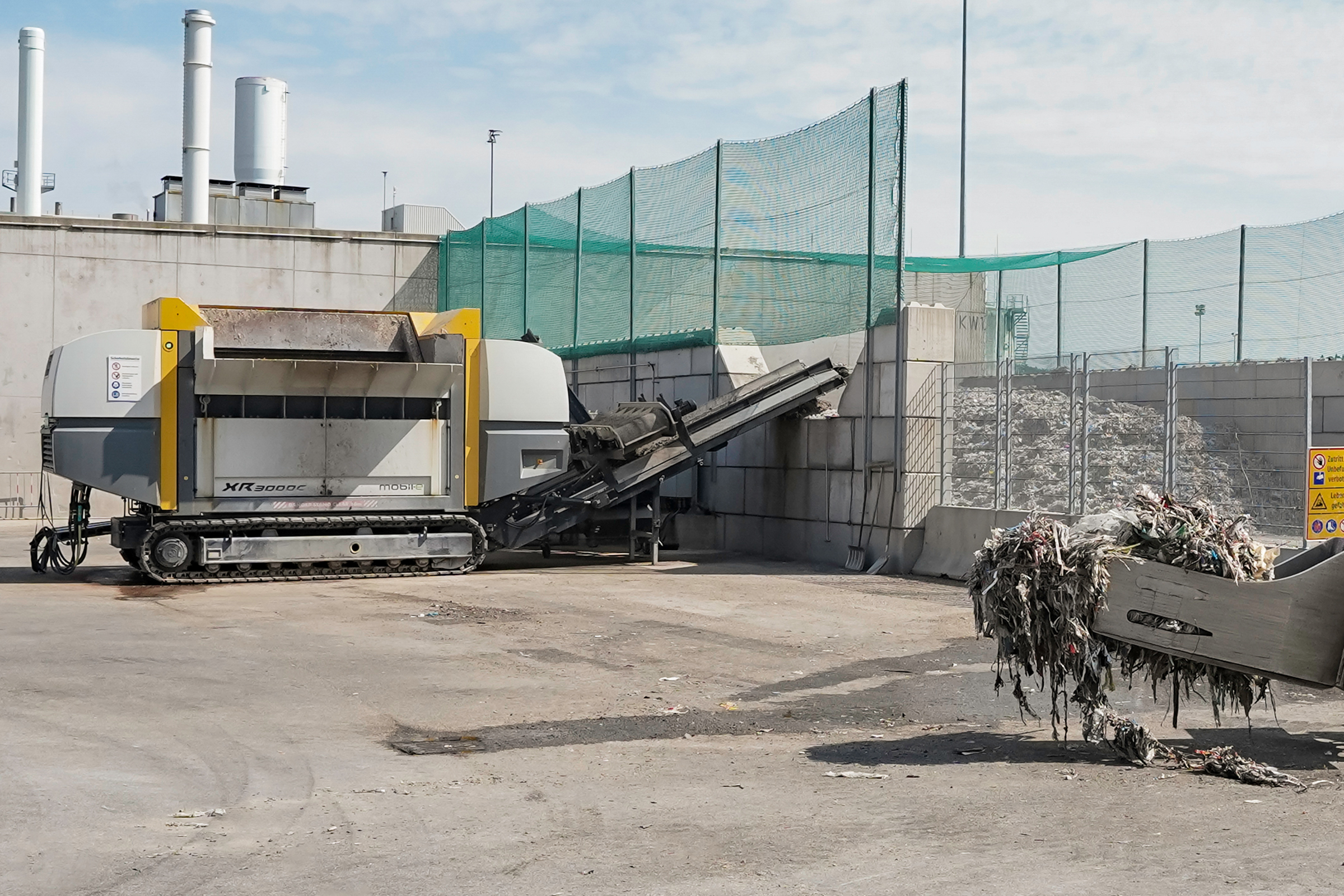
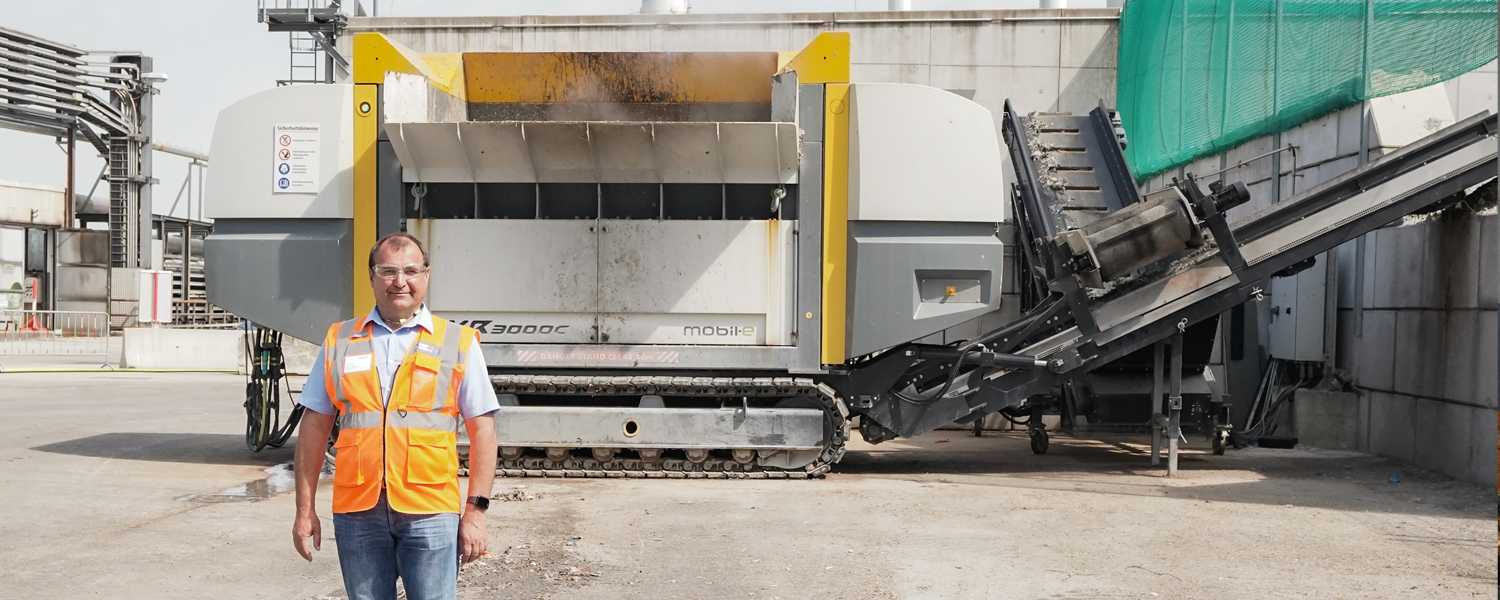
Laakirchen Papier AG is part of the internationally active Heinzel Group and one of Europe’s leading manufacturers of publication and packaging paper. The site in Laakirchen/Upper Austria has 400 employees and produces up to 780,000 tonnes of environmentally friendly publication and packaging paper a year, made exclusively of recycled fibres. The company sets great store by handling resources responsibly and ensures that production waste is used for material or thermal recovery.
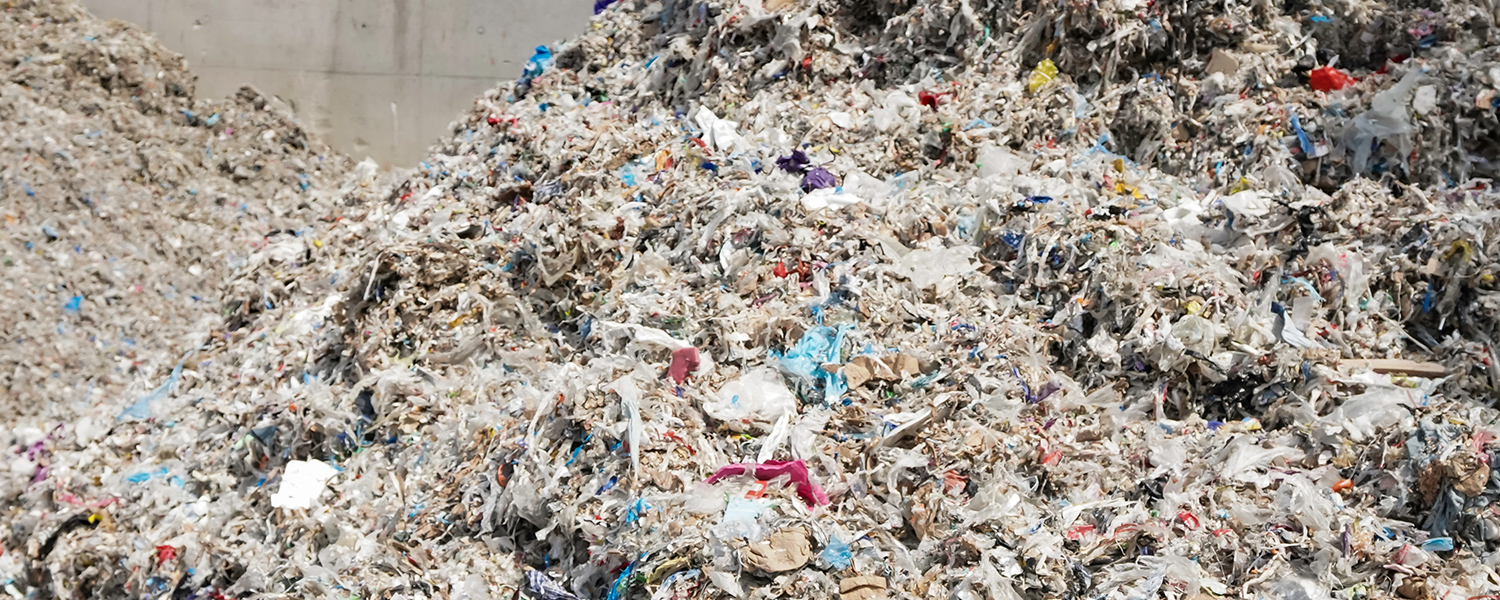
Laakirchen Papier AG produces 25 tonnes of pulper ropes every day. The ropes are four to seven metres long, with a diameter of up to 70 centimetres. They consist of long wires, around which plastic elements (foils, stickers), small metal parts (staples and paper clips) as well as textiles (threads from book-binding) have wound themselves. Due to their shape and consistency, they are difficult to process. To use the materials contained in pulper ropes for recycling and thermal processing, they need to be shredded and separated.
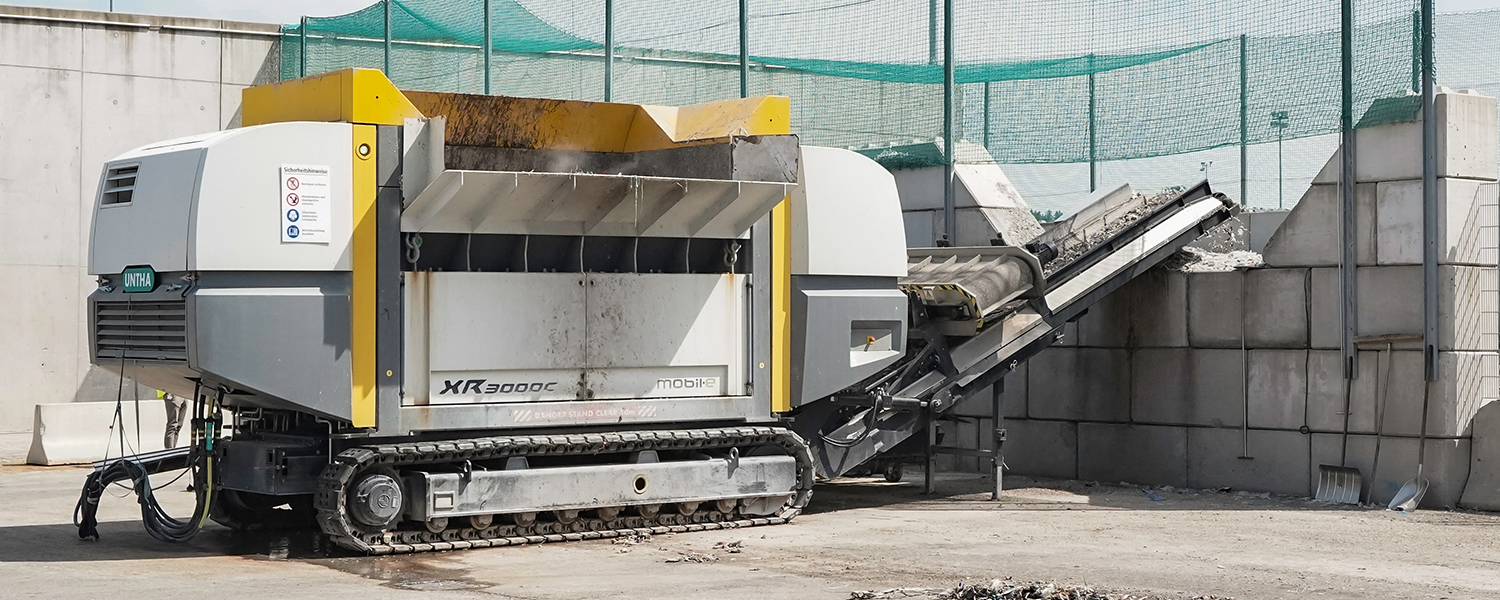
After an on-site trial run of several weeks, Laakirchen Papier AG opted for the UNTHA XR3000C mobil-e. Thanks to its innovative UNTHA Eco Power Drive, this model is particularly energy-efficient, shredding pulper ropes into a homogeneous granulate in a single-step process. The slow-running cutting unit is particularly resistant towards non-shreddables and requires little maintenance. The fully automated pusher systems ensures continuous material feed. Using the C cutting system, the XR shreds pulper ropes down to a fraction size of 25–300 mm. With an overbelt magnet, metal parts are pulled out from the granulate. The separated materials may then be used for recycling (metal) as well as for thermal recovery (plastics, textiles).
The UNTHA XR3000C mobil-e fulfils all our expectations. The shredder is energy-efficient and powerful at the same time. The output is extremely well-suited for material and thermal recovery, enabling us to make commercial use of the waste we produce. This helps us to pursue our goals in terms of sustainability and conservation of resources.
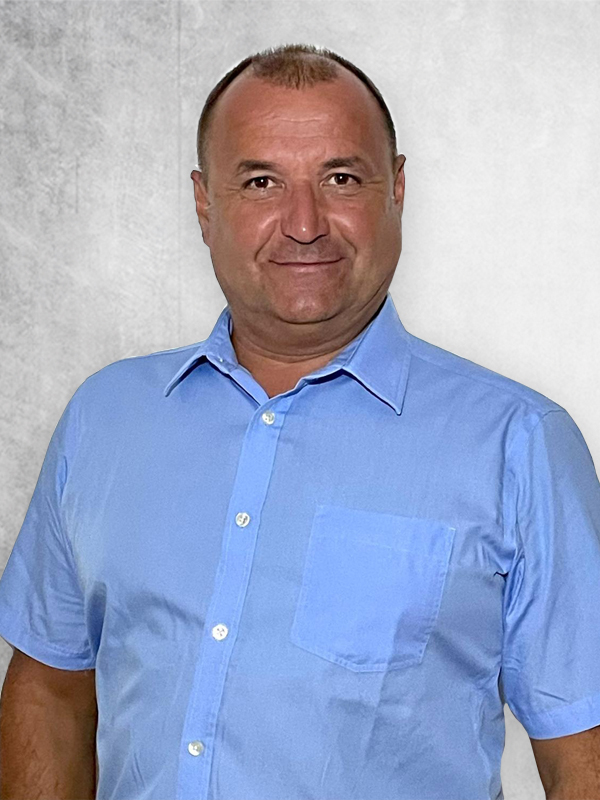
Johann Stadlmayr
Project manager
During the on-site trial run, the many benefits of the XR3000C mobil-e were confirmed. The shredder fulfils all the requirements of the company: It shreds pulper ropes in a fast and efficient way, the resulting granulate is homogeneous and perfectly suited for metal recycling and thermal recovery. Thanks to the crawler-type undercarriage, the shredder may be positioned anywhere on site. The UNTHA Genius intelligent monitoring system enables the real-time monitoring and optimisation of all features, significantly reducing maintenance requirements. The UNTHA advisory competence and extensive range of services were also pivotal factors.
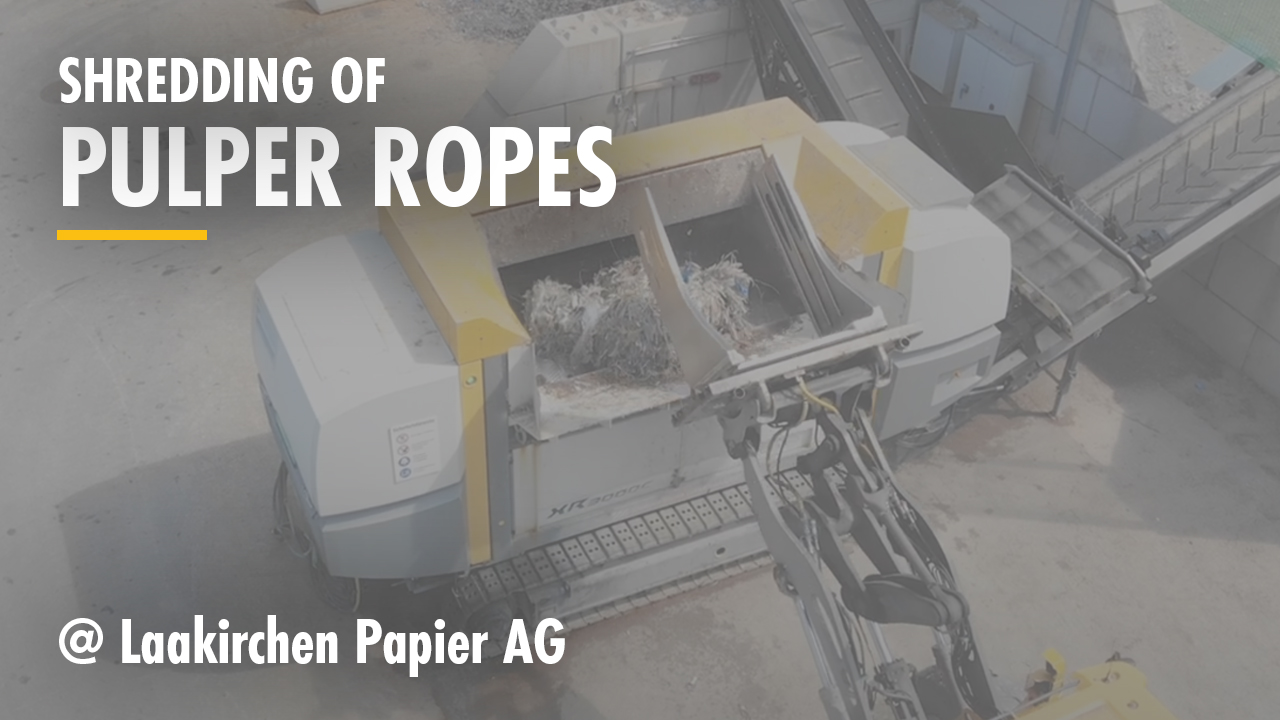