Karl Karletshofer GmbH expands service portfolio with UNTHA XR3000C
The reprocessing or recycling of metals saves energy and CO2 emissions compared to the extraction of new raw materials. In order to maximise the efficiency of metal processing, Karl Karletshofer GmbH relies on an innovative recycling line – starting with a powerful and energy-efficient UNTHA shredder, model XR3000C.
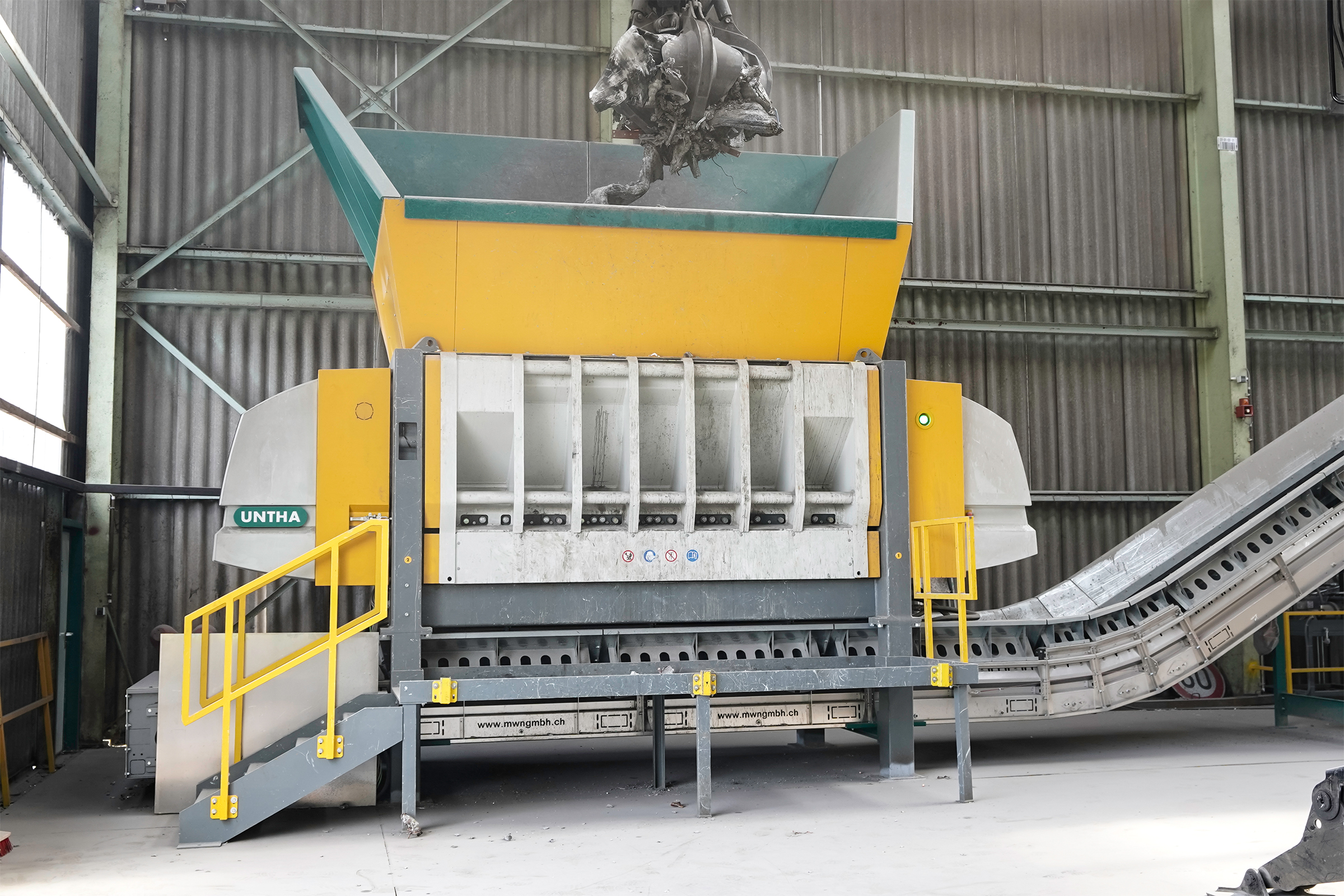
Karl Karletshofer GmbH has been active in the trade and storage of ferrous scrap, non-ferrous metals and electronic scrap for more than five decades. To round off its service portfolio, a shredding and sorting system has now been put into operation, starting with a UNTHA XR3000C. With this system, the company can now shred and sort aluminium, copper and zinc sheets, among other materials. The result: unmixed metal fractions that can be recycled as high-quality raw materials.
Processing and recycling metals
Scrap iron, metals from production plants, electronic components, hard discs and circuit boards are processed at Karl Karletshofer GmbH in Neu-Ulm/Germany. The company uses a single-shaft shredder from UNTHA for this purpose: the XR3000C is ideal for recycling material streams with different compositions and can be customised to the respective input material. Depending on the material composition, size and thickness, the shredder's operating programme can be set specifically and different perforated screens can be used. This ensures that the material is always shredded to the desired pellet size and that processes run efficiently. At Karl Karletshofer GmbH, two rows of knives in conjunction with the 130 mm perforated screen ensure that metal parts are shredded to a fraction size of approx. 130 mm. The throughput rate is around 6–12 tonnes per hour – depending on the input material. The shredder is driven by slow-running water-cooled synchronous motors – UNTHA Eco Power Drive - and is therefore particularly powerful and energy-efficient.
"The UNTHA XR3000C ensures optimum shredding of different metals during operation and prepares them optimally for subsequent sorting. The end result is a homogeneous and pure material that we can sell on to our customers as a high-quality raw material. They then return the metals to the material cycle," says Clemens Karletshofer, Managing Director of Karl Karletshofer GmbH.
Test operation as a decision-making aid
UNTHA offers interested parties the opportunity to test shredders intensively. The requirements profile for the shredder is first defined: input material to be shredded (size, composition, etc.), desired output size and throughput rate. Customers can then test the shredder in their own company, with their material and under real conditions, and see for themselves how powerful it is. During this test run, the company is supported by UNTHA's experts in order to achieve the best possible result.
"During a week-long test run at our company, we were able to get a comprehensive picture of the performance of the UNTHA XR3000C. We were able to test the shredder ourselves and received intensive support from UNTHA. After that, the decision was very easy for us," explains Clemens Karletshofer.
Images for download (Reprint free of charge for press purposes, photo credits: UNTHA shredding technology GmbH) https://untha.canto.de/b/S980V
Images 1+2: UNTHA XR3000C at Karl Karletshofer GmbH in Neu-Ulm/Germany
Images 3+4: The UNTHA XR shreds ferrous scrap, metals from production plants, electronic components, solid and printed circuit boards, etc.
Images 5+6: The UNTHA XR3000C is the starting point of a complete system in which metals are shredded and then sorted - the result is unmixed material fractions