References
The UNTHA RS50 and RS60 shredders are part of the processing lines at Bharat Forge Aluminiumtechnik GmbH in Germany. The shredders process aluminium scrap on site and prepare it for a new life cycle.

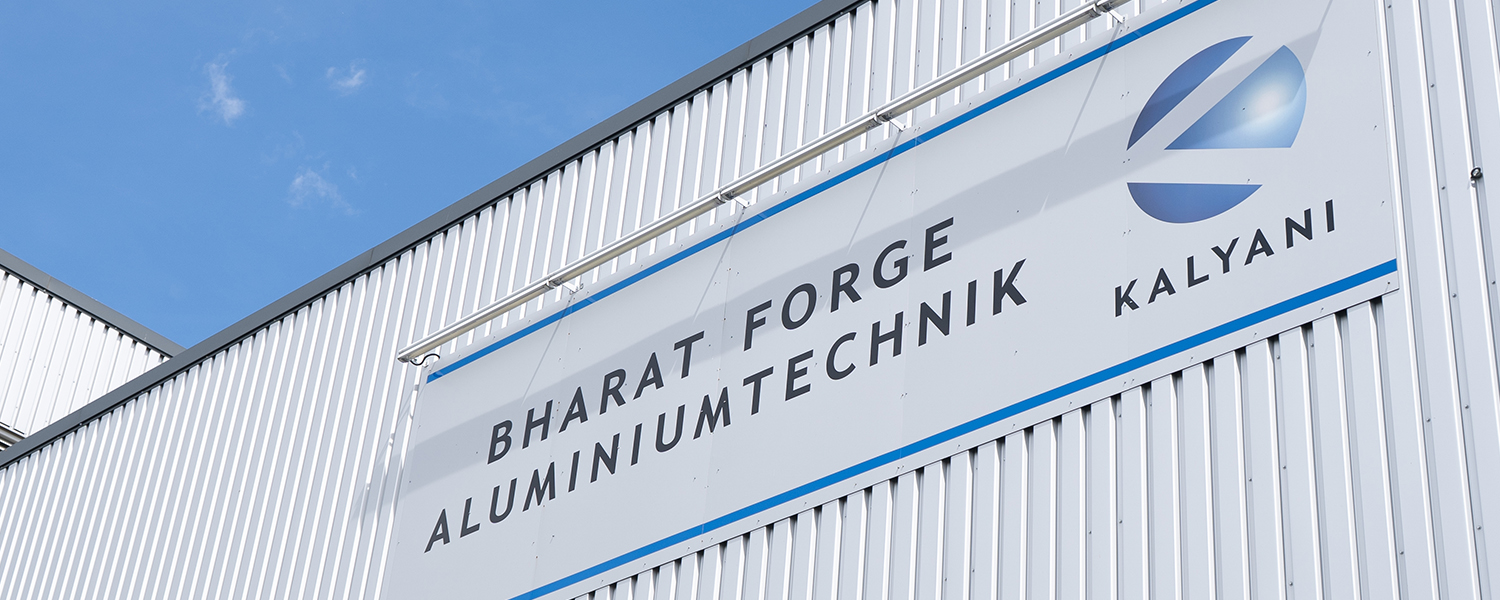
Bharat Forge Aluminiumtechnik GmbH, based in Germany, produces aluminium forging solutions for the automotive industry. The 500 employees primarily manufacture parts for chassis technology. The company is a subsidiary of the internationally active Bharat Forge Limited (BFL) – the market leader in the production of forged parts.
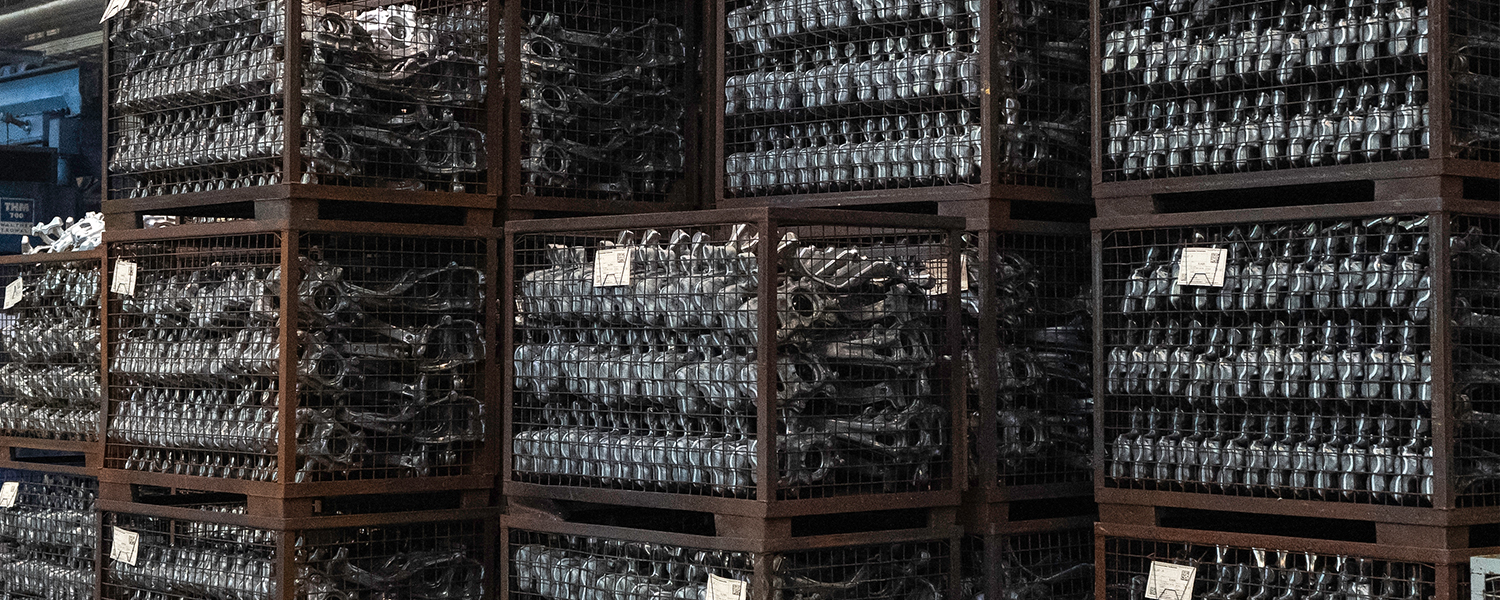
The company recycles pure aluminium, which is heated, pressed and punched out in the production lines. Punching remnants and aluminium burr scrap are melted down again in the company's own foundry and formed into new blanks. In order to process the material accordingly, it must first be shredded. The company is therefore looking for shredders that are suitable for intensive continuous operation and the processing of hot aluminium.
REQUIREMENTS
Robust construction
Heat-resistant cutting unit
Low maintenance effort
Simple placement and integration into the plant
24-hour operation
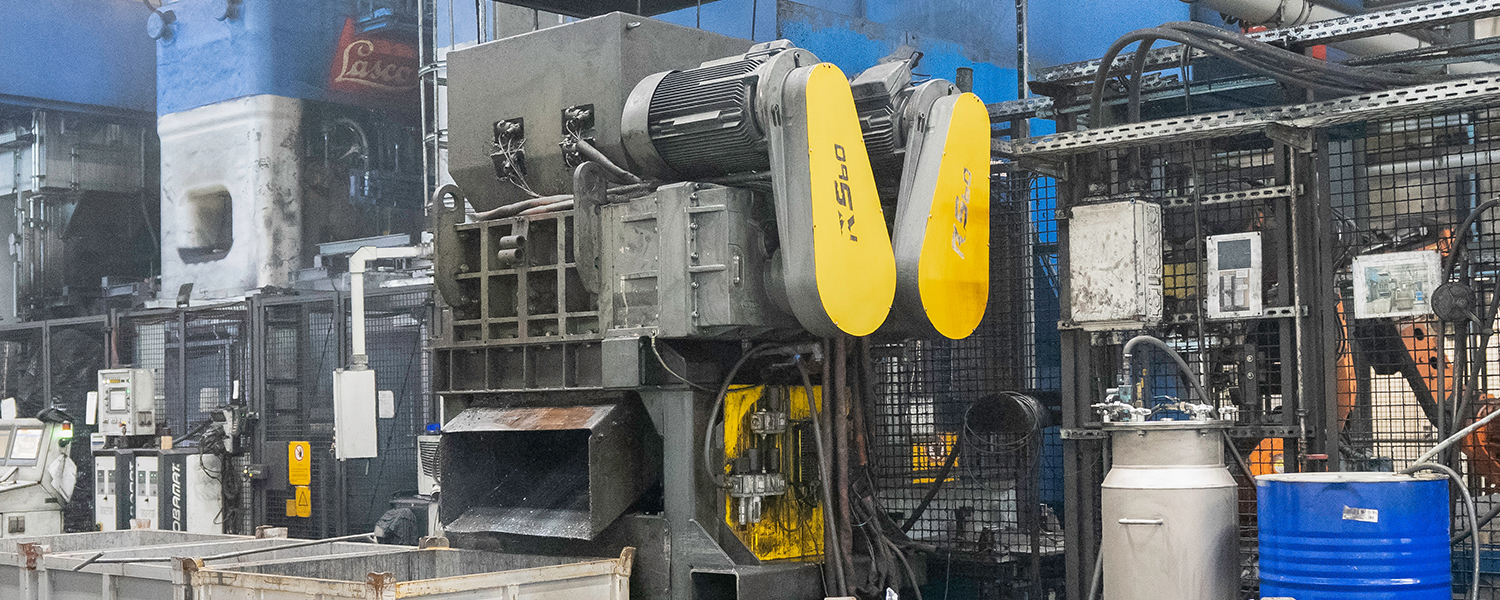
Bharat Forge Aluminiumtechnik GmbH opted for the RS model series from UNTHA. The RS50 and RS60 shredders are used there in two processing lines. The aluminium pieces are approximately 600 mm long and 30 mm thick and are fed into the shredder at a temperature of up to 450 degrees. The cutting unit and the wear plates/inserts are special designs. This prevents wear caused by the hot aluminium. The shredders are also equipped with an automatic central lubrication system.
The processing lines, and therefore also the shredders, are in operation 24 hours a day. To ensure continuous operation and minimise downtime, the company has two UNTHA RS50s and two UNTHA RS60s. This means that the shredders can be removed from the line for upcoming maintenance and replaced with their doubles.
UNTHA carried out two series of tests for and with us to find the perfect shredder for our requirements profile. Firstly, tests were carried out in the technical centre in Austria. And then we were able to test the shredder in our company.
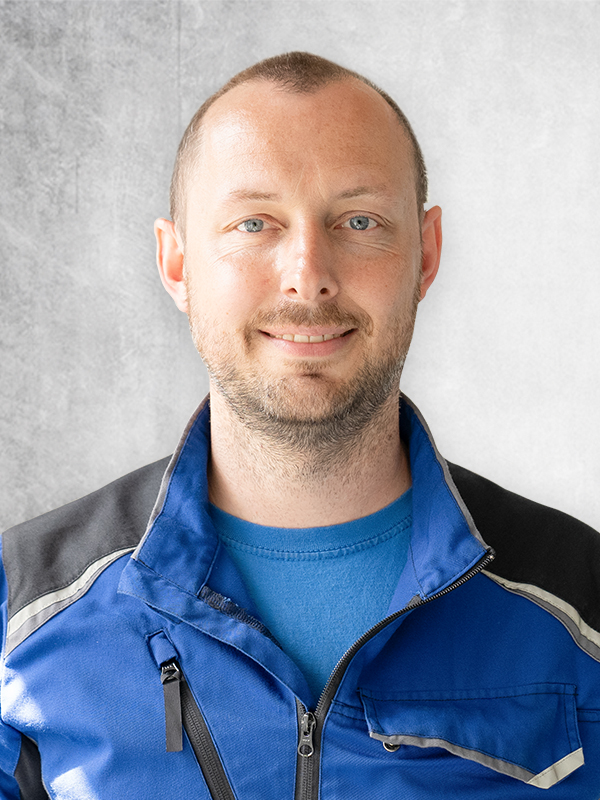
Andy Vogel
Head of Forging at Bharat Forge Aluminiumtechnik GmbH
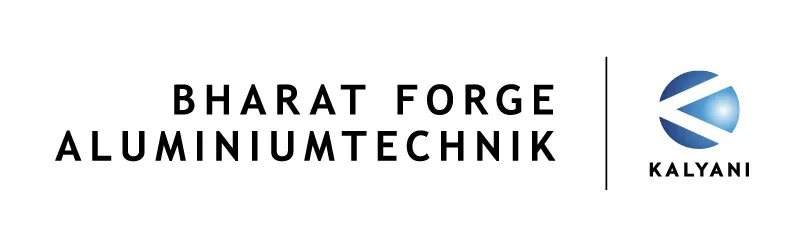
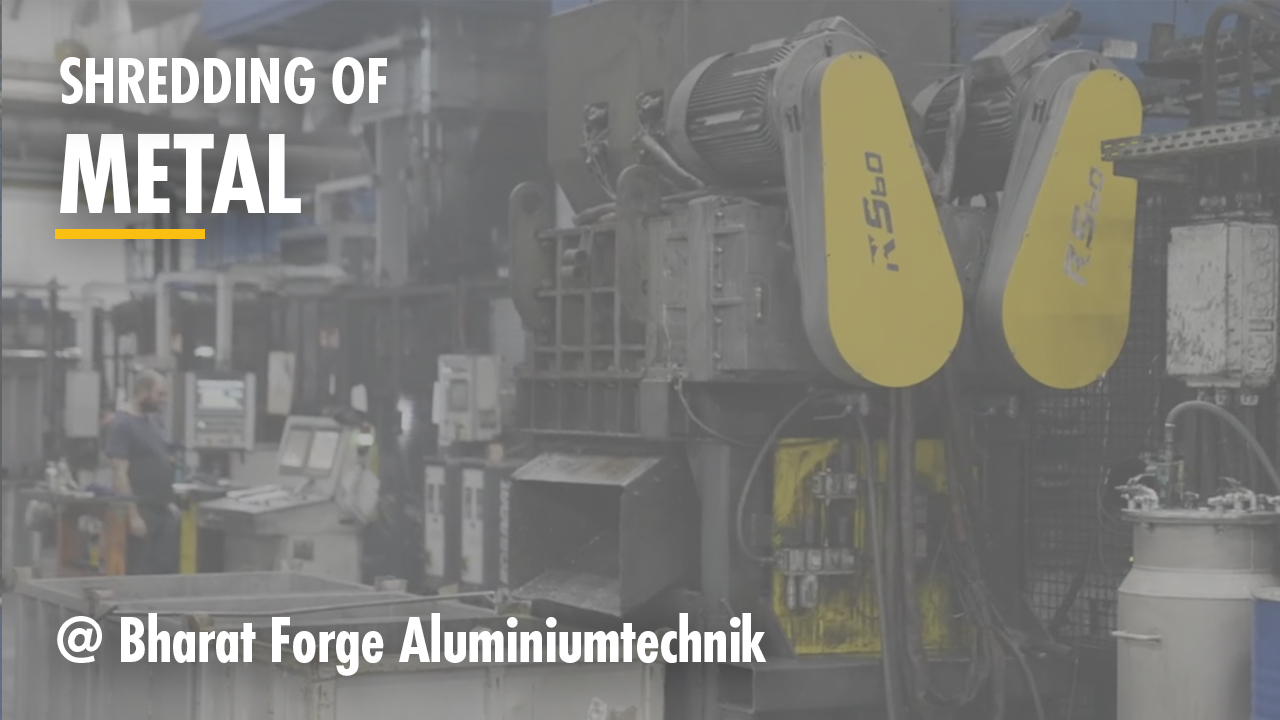