References
At the Pitschl joinery business in South Tyrol, an UNTHA LR700 takes care of all aspects of residual wood processing. The shredder is fed automatically and shreds residual wood into a homogeneous output material quickly and energy-efficiently. This output material is then burnt in the in-house heating plant that supplies the entire site with hot water and energy for heating. In this way, 100 % of the residual wood is used, making the business completely independent in terms of energy production.

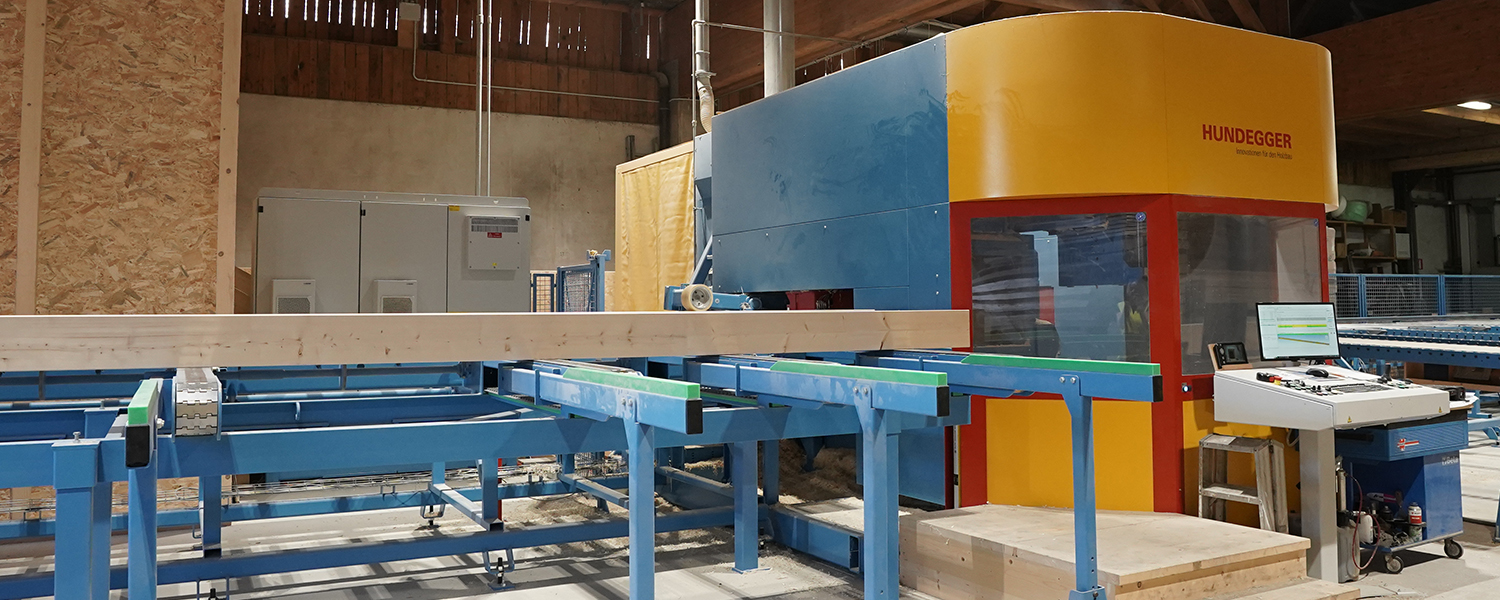
Pitschl GmbH is a joinery and wood processing business based in Aldein/South Tyrol. The family business was founded in 1957 and is today run by Matthias and Christoph Pitschl in the third generation. It currently employs ten people and its product portfolio includes classic joinery work, such as staircases, balconies, roof structures and timber construction, using predominantly regionally sourced spruce and larch wood.
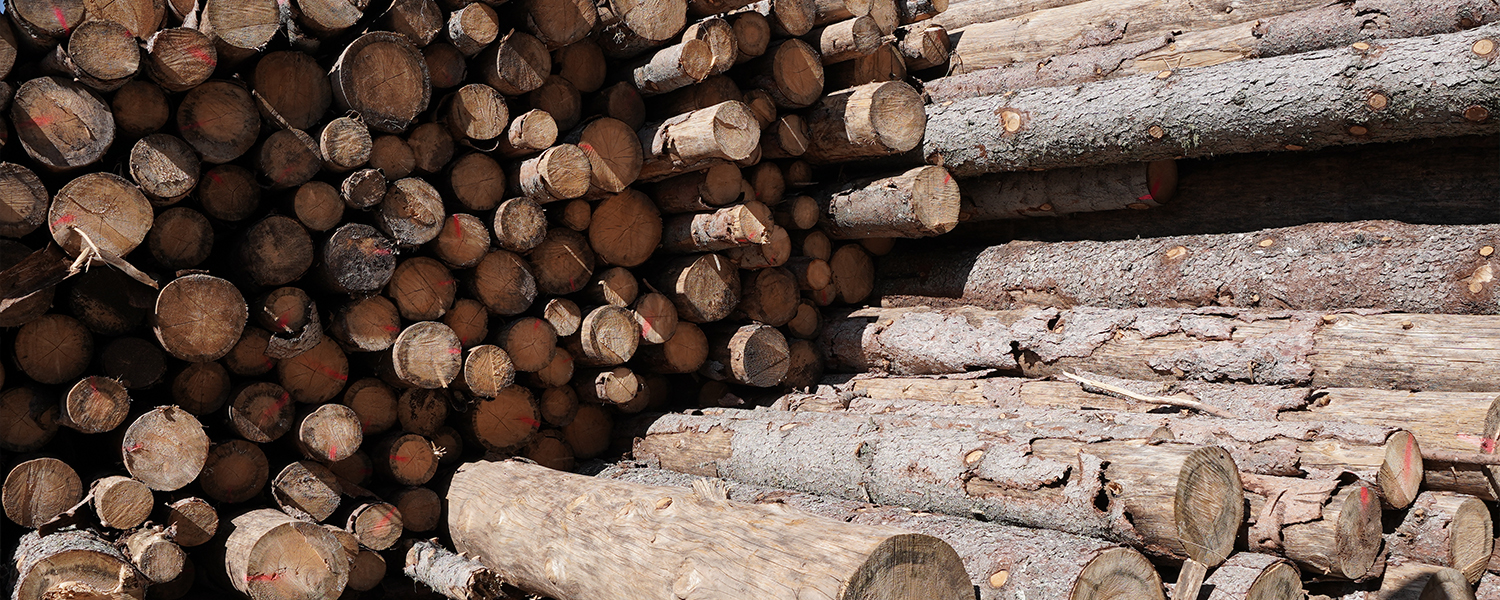
When it came to modernising its production facilities, Pitschl GmbH was first of all on the lookout for a new joinery machine. The goal was to connect and automate workflows in order to make processes more efficient. With this in mind, Pitschl also wanted to purchase a shredder. The business accumulates approx. 3 m³ of residual wood per day: solid timber pieces from the joinery machine, with dimensions of approx. 20 x 20 x 40 m, and residual wood from its building sites. One of the most important requirements for the shredder was the option of linking it to the joinery machine and feeding it automatically.
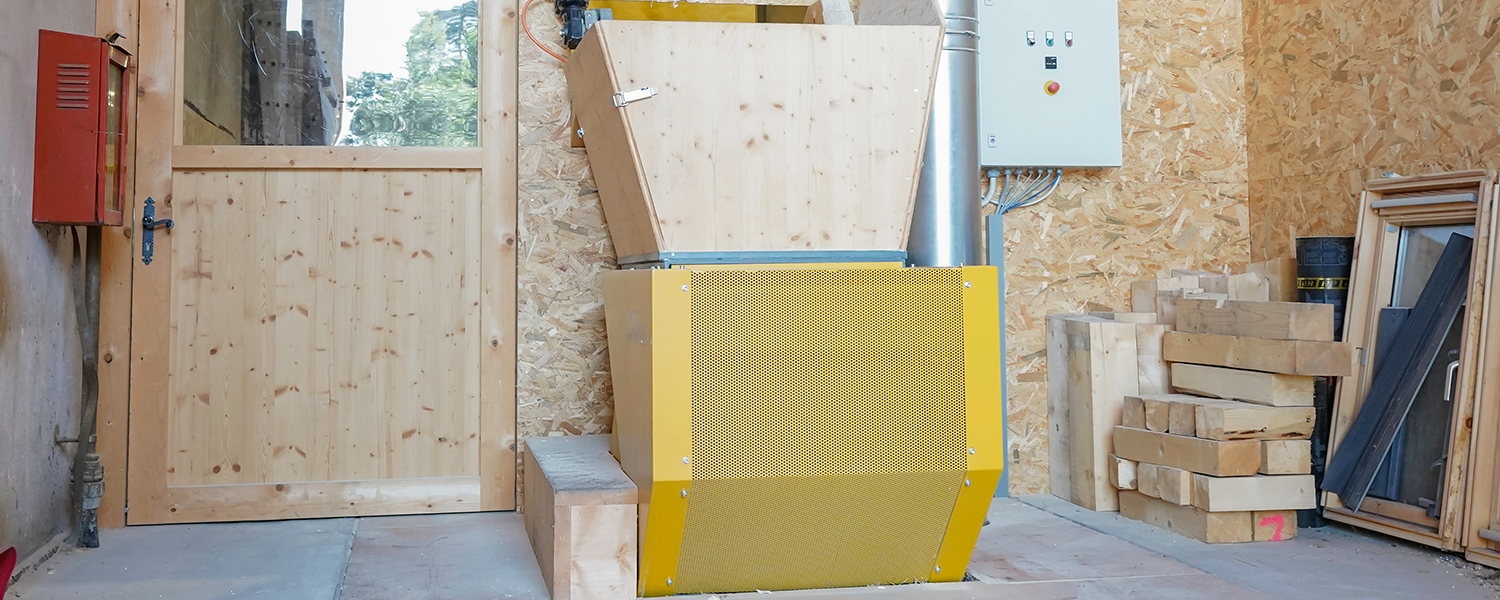
The Hundegger company developed a system solution that consisted of a joinery machine, a conveyor system, an extraction system and a shredder. All these components are linked with one another and monitored electronically. Hundegger recommended an UNTHA shredder, which could be perfectly integrated in the overall system. The UNTHA LR700 is linked to the joinery machine with a conveyor belt, which feeds it with residual wood on an automated basis. However, manual feed-in via the hopper is also possible. As soon as material is fed into the hopper, the shredder starts automatically, and it stops as soon as the hopper is empty. This avoids idle running and saves energy. The hopper is monitored by a camera: when a certain fill level is reached, the conveyor belt stops to prevent overfilling. The shredded material is transported to a silo via an extraction system, and from there to the in-house wood chip heating plant.
I will definitely recommend UNTHA to others. The LR700 shredder fits in perfectly with our system solution, which consists of a joinery machine and conveyor technology. Essentially, we don’t have to worry about the residual wood at all: the shredder is fed automatically by a conveyor belt, shreds the wood into uniform pieces, and the extraction system takes care of the wood chips and transports them to the silo
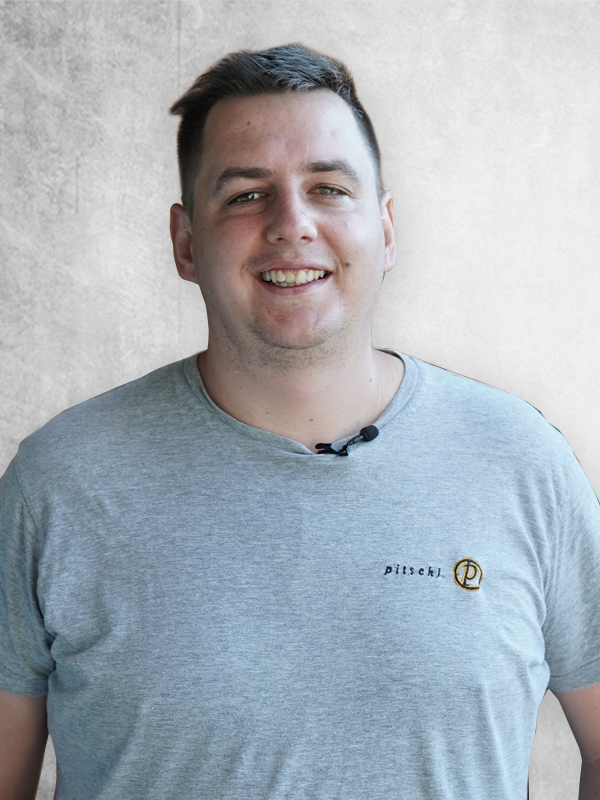
Matthias Pitschl
Managing Director
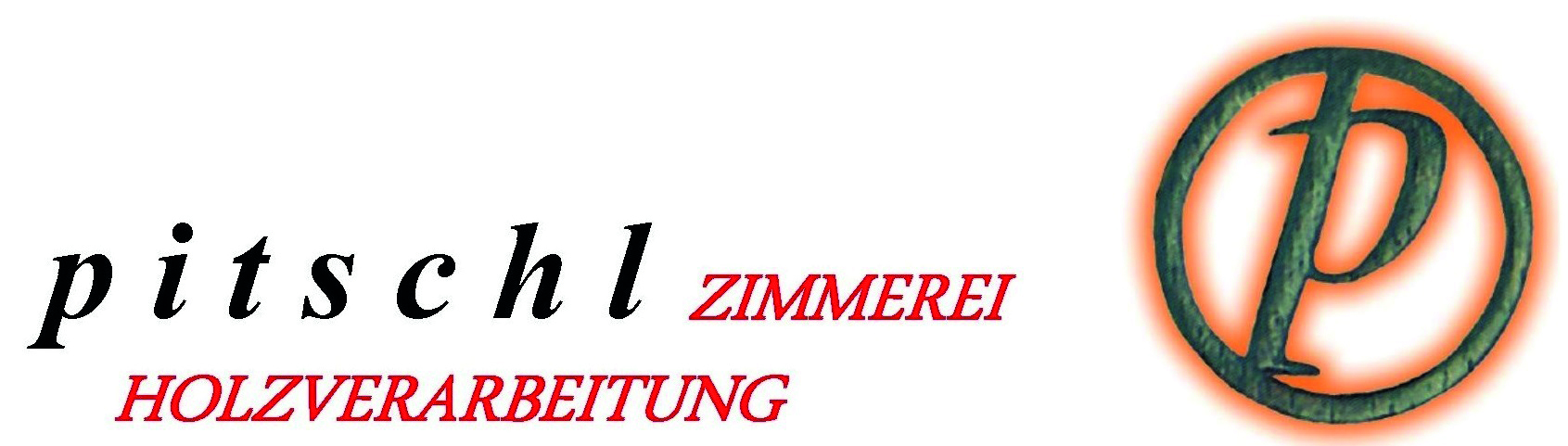
The UNTHA LR700 is ideal for joinery businesses with a low volume of residual wood. Its robust design requires little floor space, which means that it is easy to accommodate even if space is limited. The cutting system is resistant to foreign matter and shreds residual wood of different sizes and consistencies without any problems. The homogeneous output is ideally suited for use in a wood chip heating system. At Pitschl, it is used to supply the entire site - production, drying room, offices and residential building - with heating and hot water.
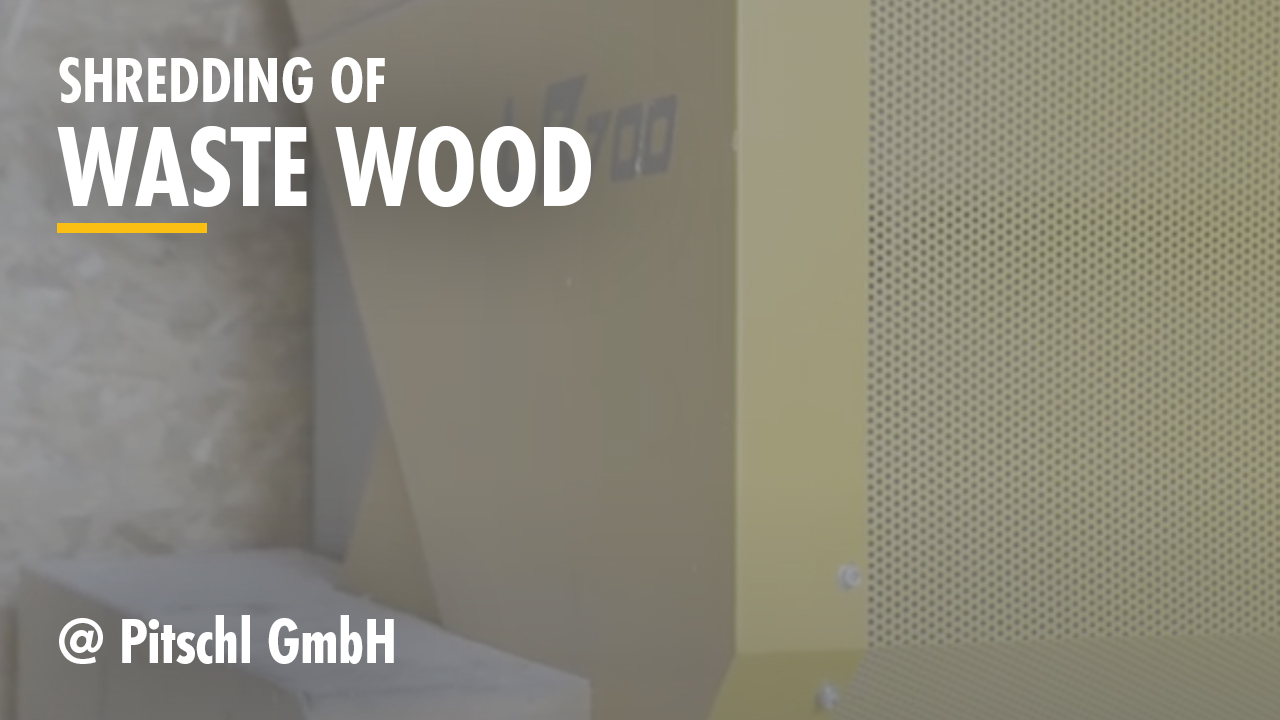