References
The RDG Recycling Group, based in Austria, shreds plastic-metal composites to produce pure plastic granulates that can be recycled and reprocessed into new products. The company's work is supported by an UNTHA shredder – XR3000C mobile-e.
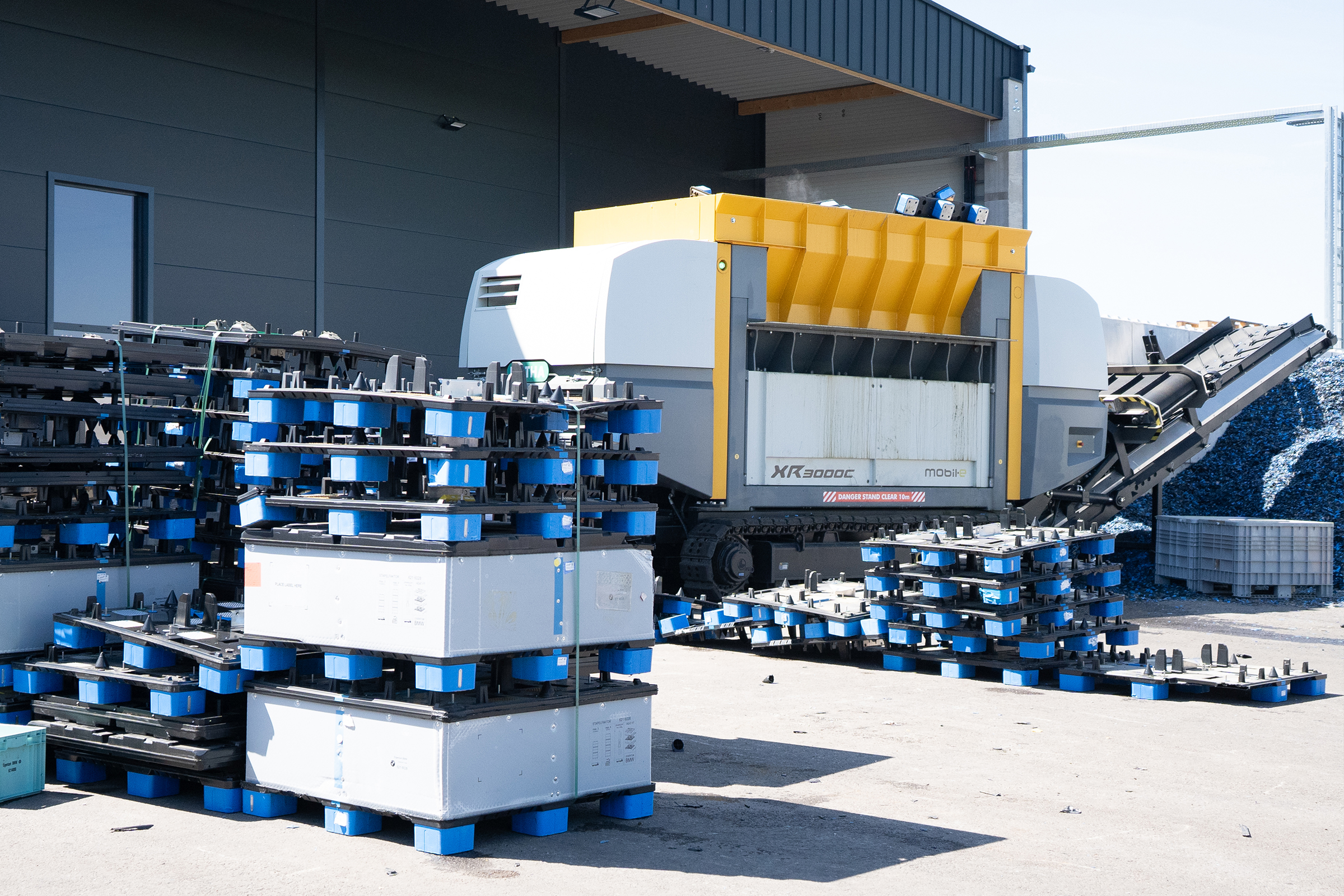
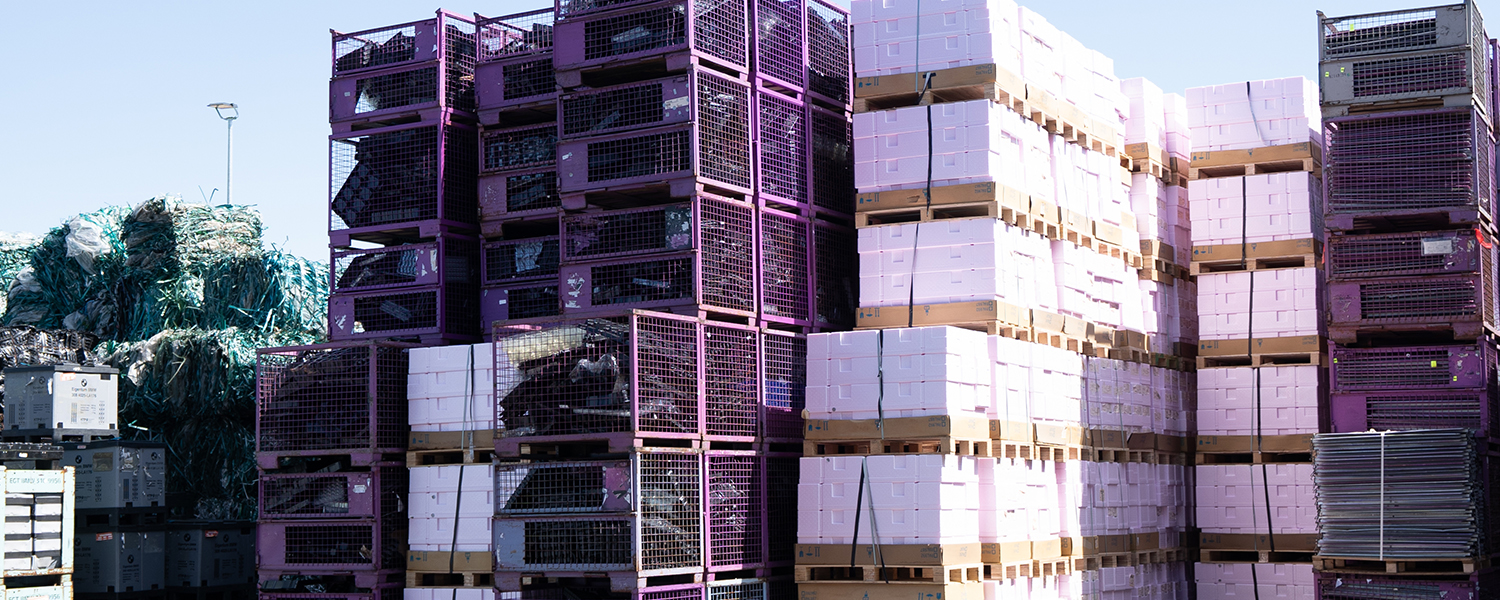
RDG Recycling Group, based in Austria, was founded in 2012. The company focuses on recycling plastics, such as production waste, plastic-metal composites and large-volume post-consumer waste. RDG produces around 16,000 tonnes of granules annually, thus saving 32,000 tonnes of CO2 – making a significant contribution to the circular economy.
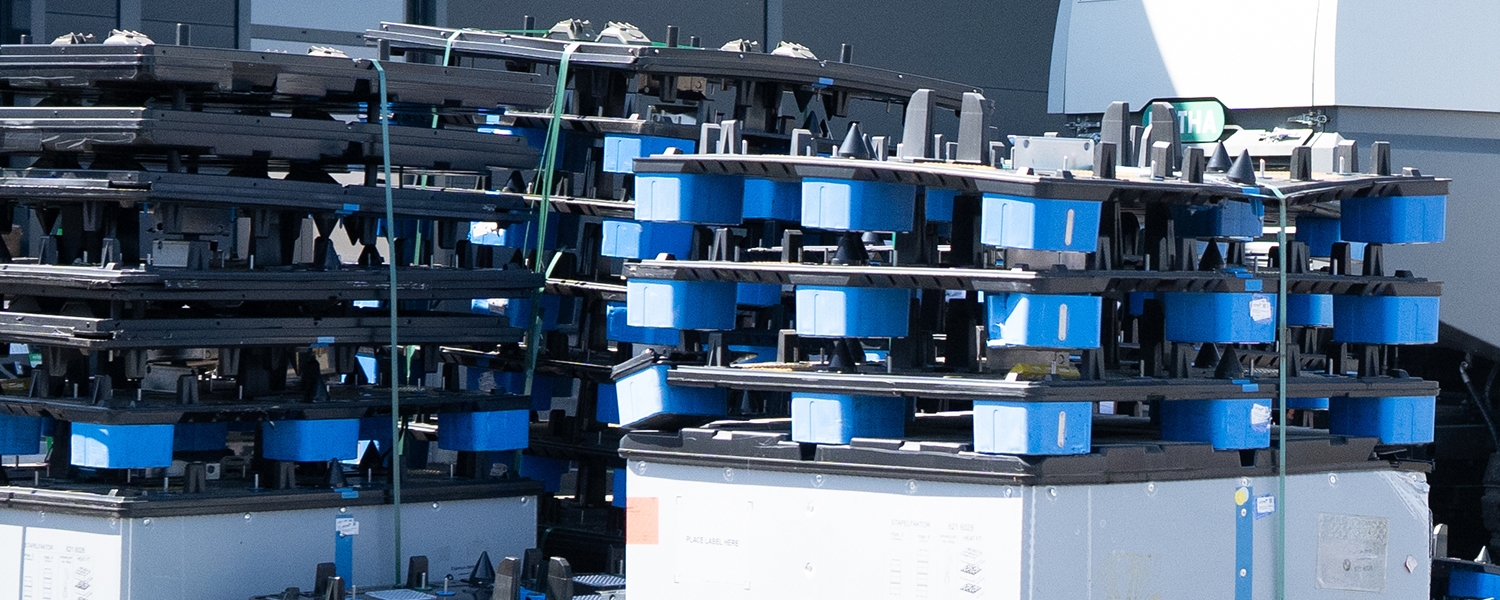
Processing plastics for recycling involves several steps, including pre-shredding, sorting, cleaning and grinding. Since its launch, RDG has primarily processed plastics originating from industry. Over the years, the composition of the materials has become more and more diverse, and pure plastic fractions have become rare. Today, the company often deals with plastic-metal composites.
REQUIREMENTS
Cutter resistant to metals
Energy efficiency
Loading via wheel loader/forklift
Different perforated screens
Quick-change screen system
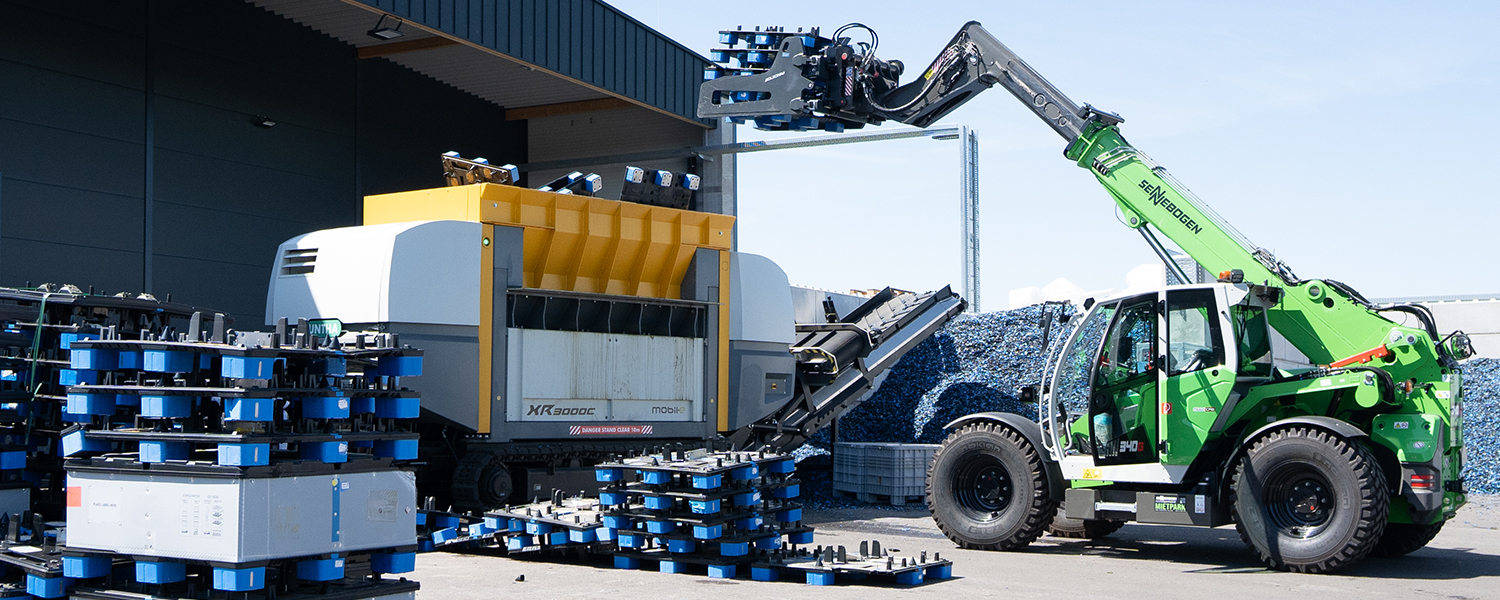
Plastics with metal inclusions/fittings can be easily processed with the UNTHA XR3000C. This shredder has a wide hopper that can be loaded by forklift or wheel loader. The shredder is powered by the UNTHA Eco Power Drive – this energy-efficient direct drive, consisting of high-torque synchronous motors, ensures powerful shredding and is resistant to foreign objects. The speed control is load-dependent and automatically ensures that the torque and speed are adjusted. The material is optimally pre-shredded using the C-cutting system. The 50-mm perforated screen ensures that 90% of the pieces smaller than 40 mm leave the shredder. Depending on the material composition and the desired output size, up to 5 tonnes of material can be shredded per hour. A magnetic separator then removes any metal parts. This is followed by sorting and grinding processes to achieve pure, fine-grained plastic granulate. RDG opted for the mobile version of the XR – this means that the shredder can be moved flexibly.
The composition of materials is becoming more and more diverse, pure plastics are now a rarity. We needed a shredder that could handle plastic-metal composites and came across the UNTHA XR3000C mobil-e. This shredder has completely convinced us.
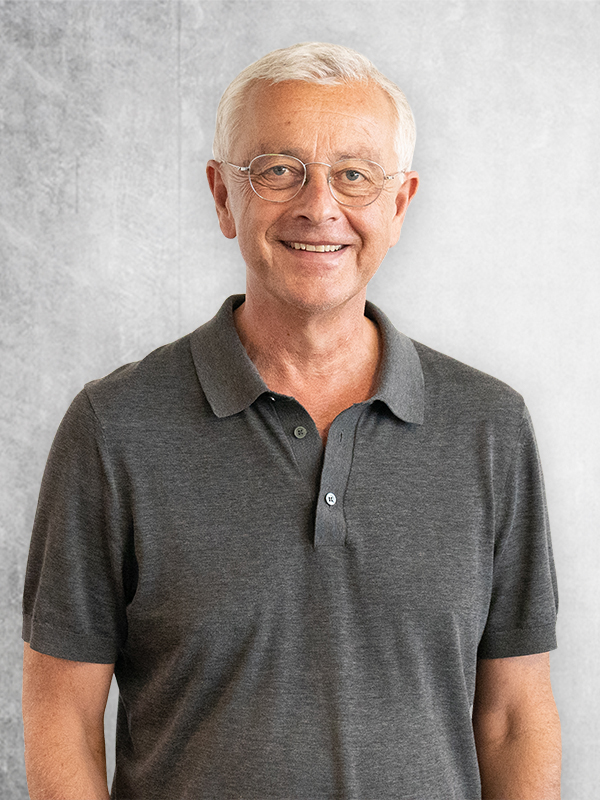
Franz Kobleder
Shareholder and managing director of RDG Recycling Group
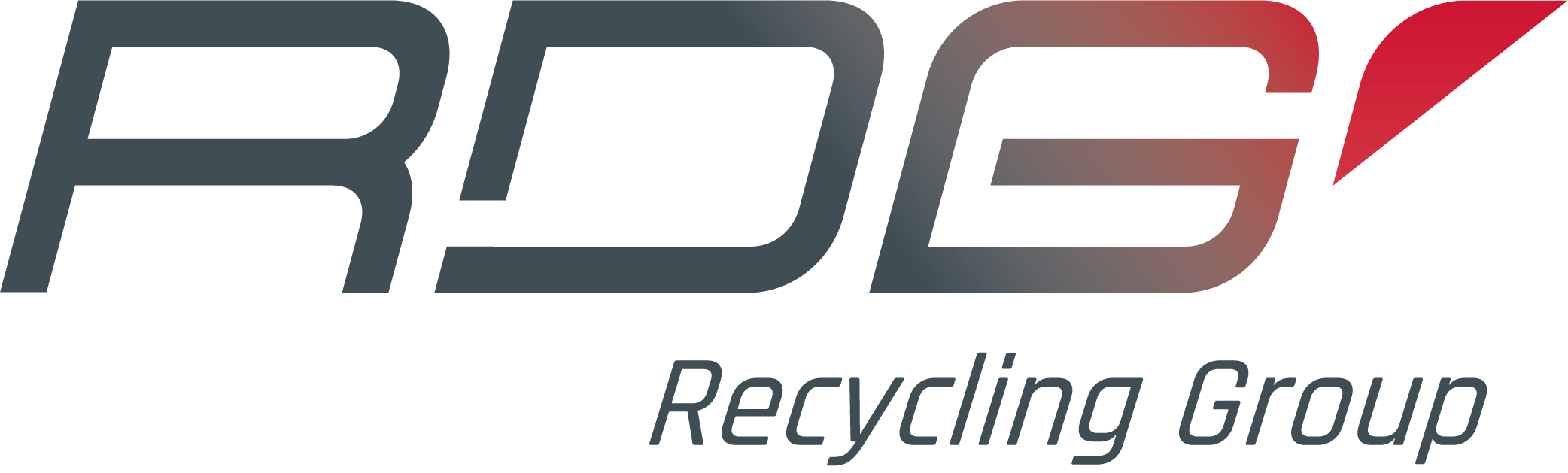