AMAG Ranshofen relies on UNTHA’s expertise for recycling aluminium
Amag Ranshofen is a globally known producer of premium aluminium, cast and rolled products. AMAG Casting, the aluminium recycling branch of the AMAG Group, was looking for a flexible, robust single-shaft shredding solution to add to its existing machinery. The biggest challenge was finding a way to process a wide range of scrap aluminium with a single unit. In the UNTHA XR3000C mobil-e shredder, the company has found its ideal partner.
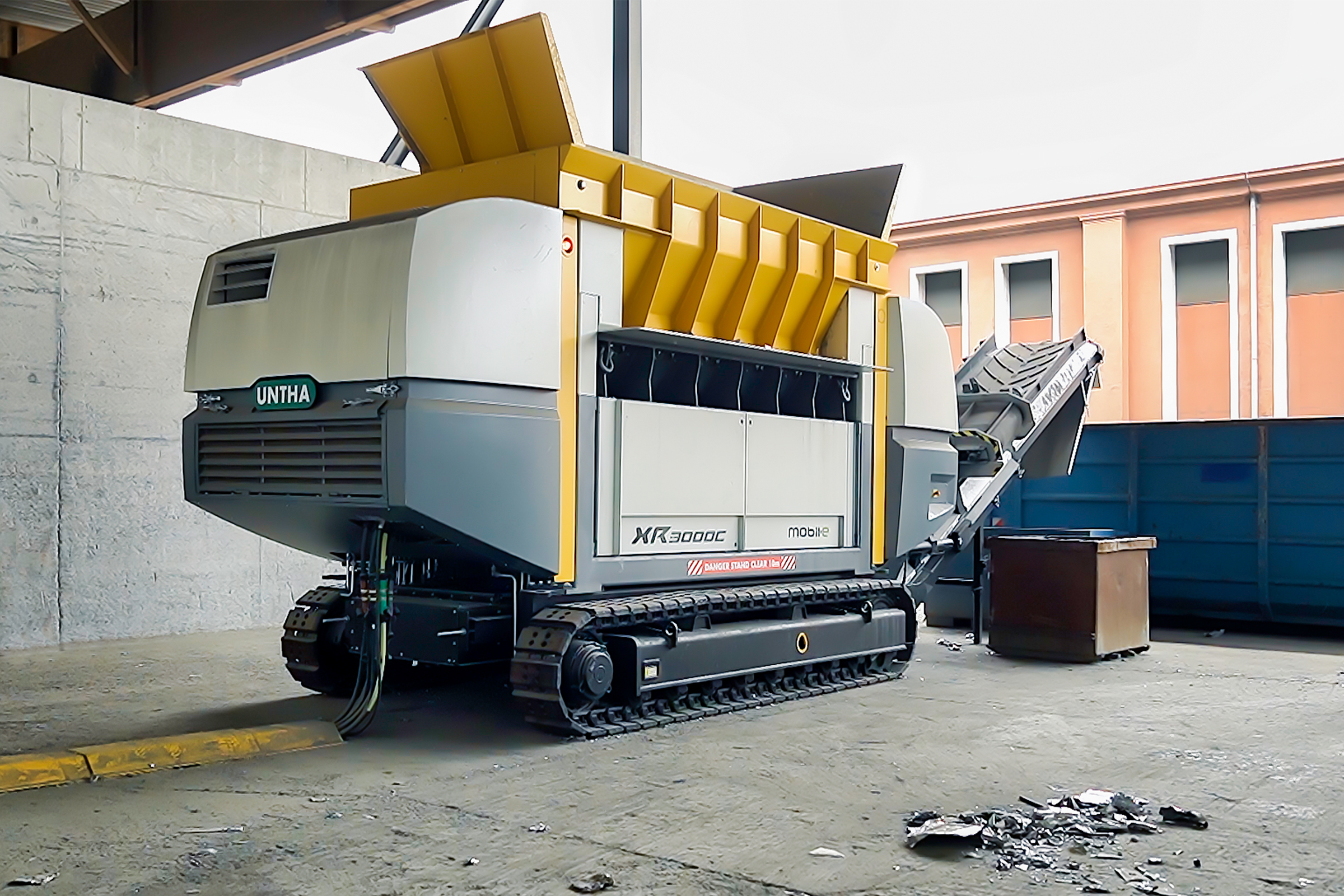
When evaluating options for aluminium processing, AMAG came across the expert solutions provided by UNTHA. The new shredder would have to be flexible and robust, with a definable target grain size achieved by exchangeable perforated screens. Two weeks of extensive trial runs during which the material to be shredded was tested in real-life conditions with a mobile XR solution convinced the AMAG decision-makers that they had found what they’d been looking for.
XR copes with a wide range of material types
The XR3000C mobil-e has been actively in use in Ranshofen since May 2020 and shreds aluminium scrap in a wide range of designs, dimensions, and homogeneities. The input material comes from scrap metal suppliers in the area. Depending on its consistency, the shredded product is either used directly in smelting furnaces or processed further in sorting plants. The throughput is largely determined by the consistency of the input material and varies from 2 to 10 tonnes per hour. The greatest benefits for the company arise from the flexibility of the unit, the fact that it is mobile, and from the definable target grain size, thanks to exchangeable perforated screens. As an additional benefit, the UNTHA machine is highly economical compared to standard diesel drives, thanks to the electric UNTHA Eco Power Drive.
Great results, highly recommended
“So far, our experience with the unit as well as trends and feedback have all been highly positive. AMAG as has also had the chance to try out the UNTHA Service Competence Center, and we are very impressed with the speed and technical quality of the response we got from Kuchl. All in all, we warmly recommend UNTHA!”, says the head of production.
AMAG Ranshofen
The core areas of AMAG are recycling, casting, rolling, and surface and heat treatment of materials. The Ranshofen site produces mostly coils, plates and sheets in all alloys. The main customers are the automotive and aerospace industry, mechanical engineering firms, construction businesses as well as the packaging and consumer goods industry.