References
At the Rohrmoser carpentry firm, the waste wood from production and construction sites is recycled in the compact UNTHA LR700 wood shredder to produce valuable fuel for wood chip heating systems.
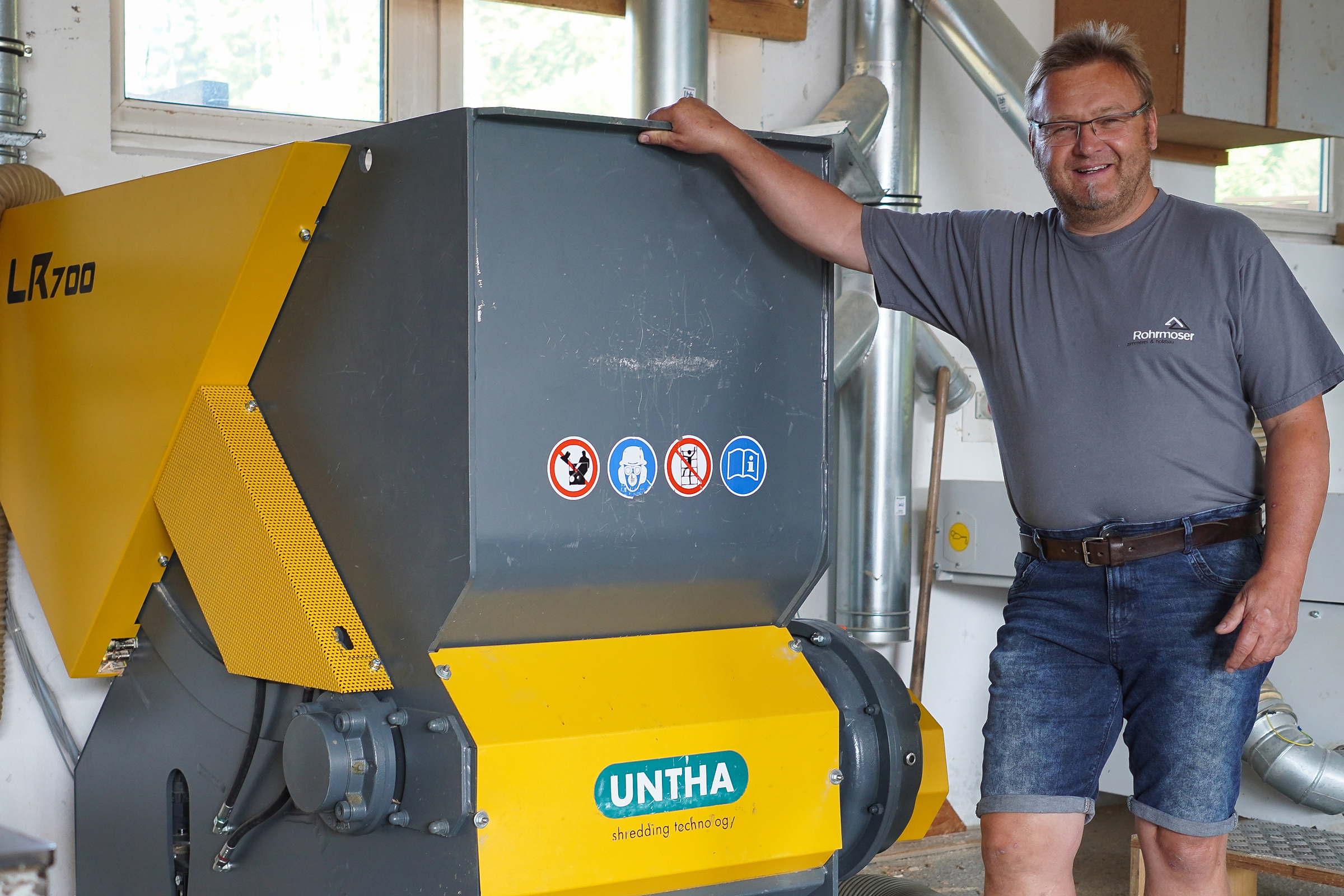
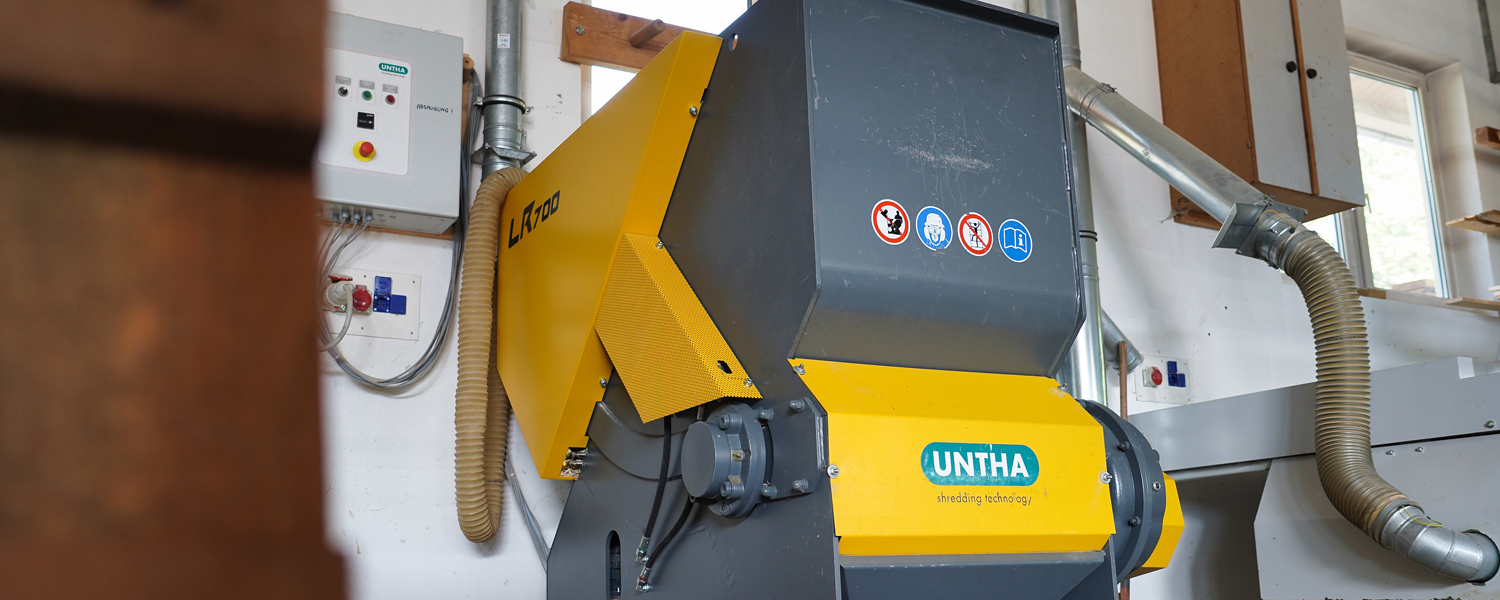
The Rohrmoser carpentry and timber construction business in Flachau/Salzburg employs six people. Ever since 1992, the business has taken on general carpentry work, building wooden houses, car ports, roof structures, and balconies.
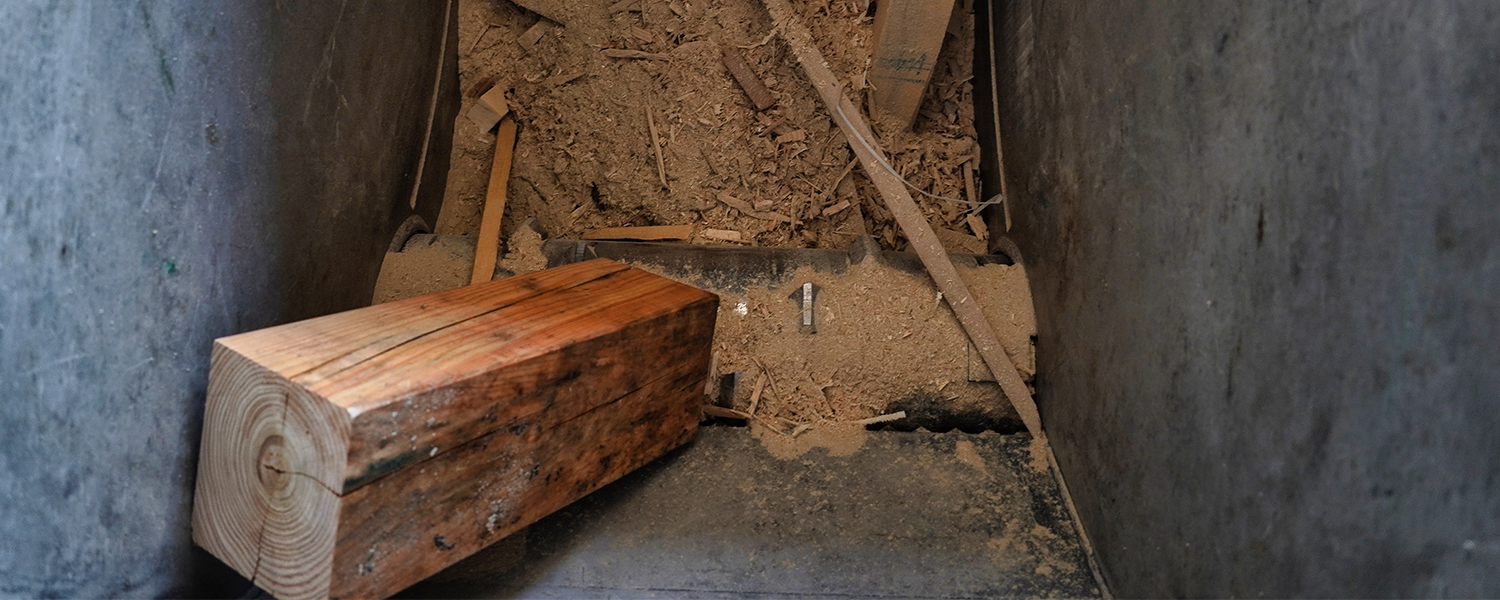
Waste wood from the production process, from construction sites and from single-use pallets needs to be processed quickly in order to be used as an energy source at 100 percent. The wood chips are used to fire the wood chip heating system that heats both the business premises and the adjacent home.
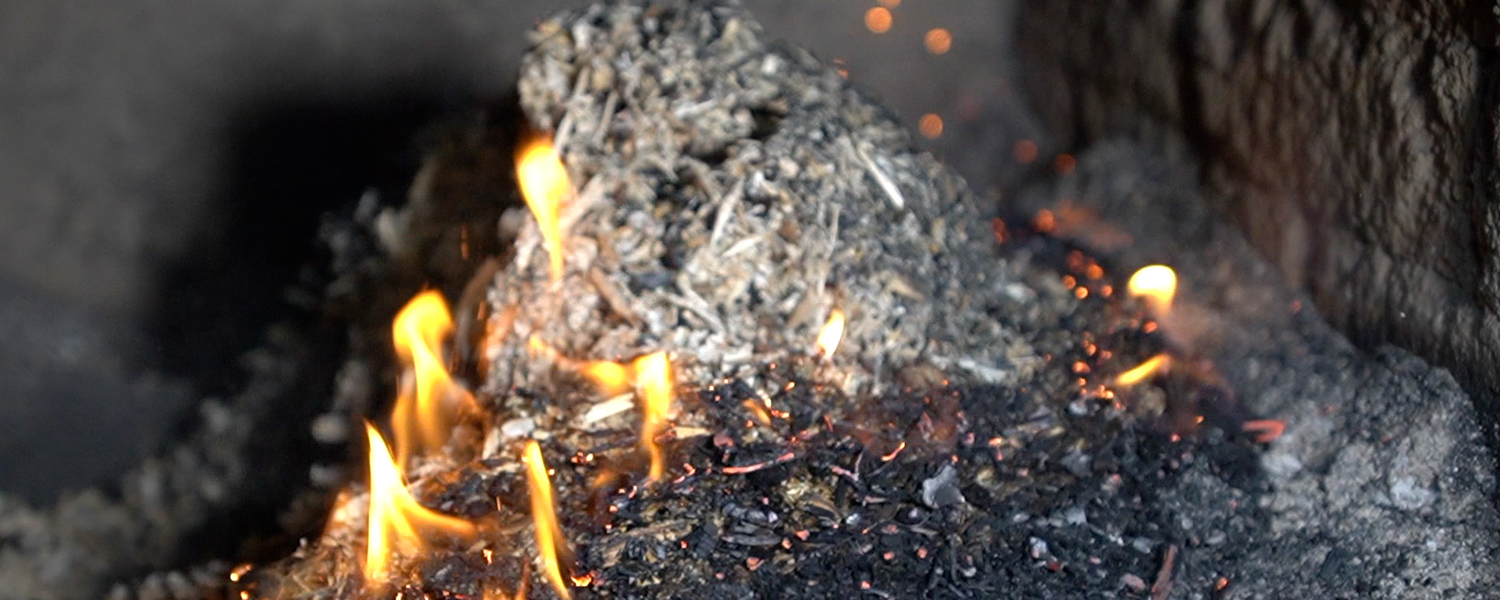
Rohrmoser first began to use an LR700 shredder from UNTHA shredding technology for the shredding of waste wood around Christmas 2016. Waste wood from joinery constructions, splinters from circular saw operations and waste wood from the construction sites are all fed into the shredder and are mixed with wood shavings, resulting in a particularly productive heating material. The chips are extracted into the chip silo straight after the shredding process, where they are stored until the winter, when they are fed into the wood chip heating plant via a discharge system. For business owner Johann Rohrmoser, this means that he is able to heat not only his entire business premises, but also his home right next door. The LR700 shredder is filled twice a day and runs for an hour each time.
The LR700 shredder is robust, compact, and crucial to us in our daily workflows.
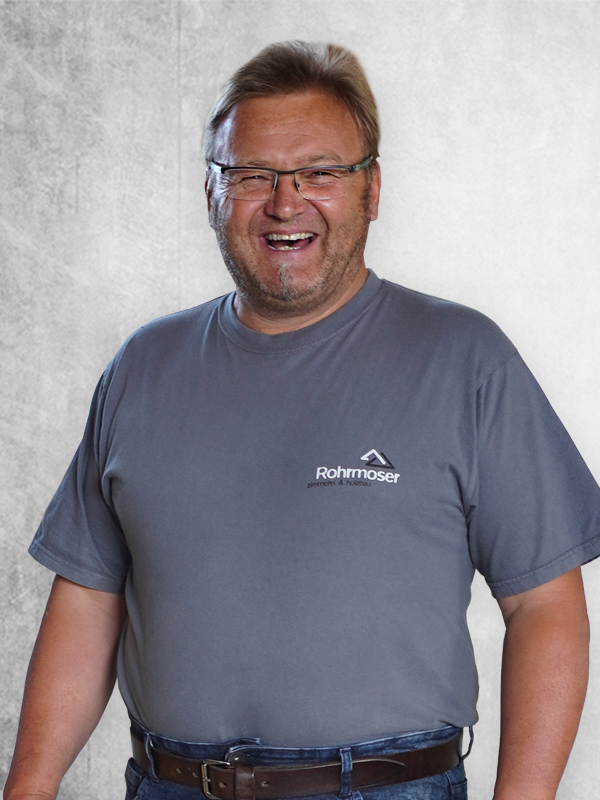
Johann Rohrmoser
Owner
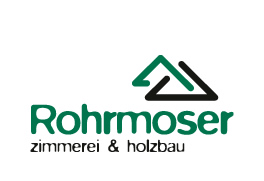
The LR700 is the second UNTHA unit in operation at Rohrmoser, where a smaller, two-shaft shredder had provided a valuable service over many years. Johann Rohrmoser is more than happy with the purchase he made in 2016. Johann Rohrmoser sees the benefits of the unit in the cutting system with a swivelling pusher and the low maintenance requirements. In the three and a half years since the unit was first put into operation, it has completed approximately 250 operating hours.
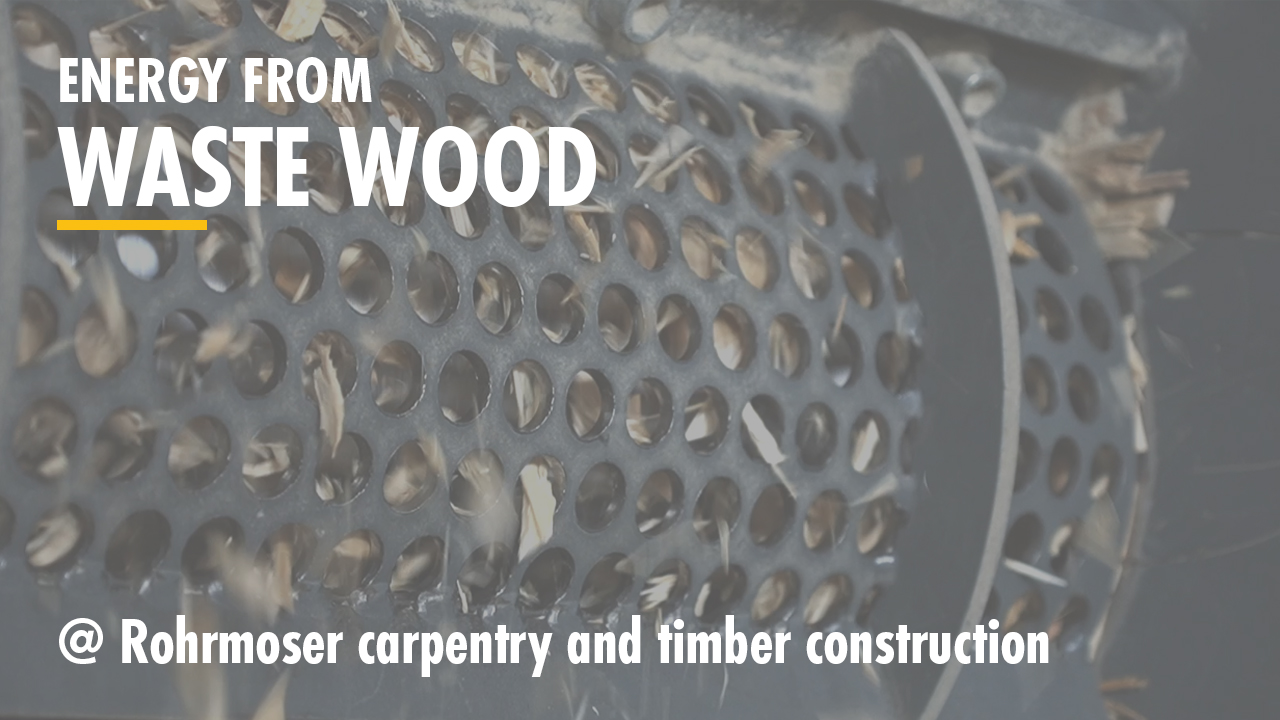