References
An UNTHA XR3000C shredder is processing up to 60 tonnes of C&I and C&D waste per day at the midlands facility. With energy efficiency, reliability, and flexible financing, this investment supports Tom White’s ambitious growth plans.
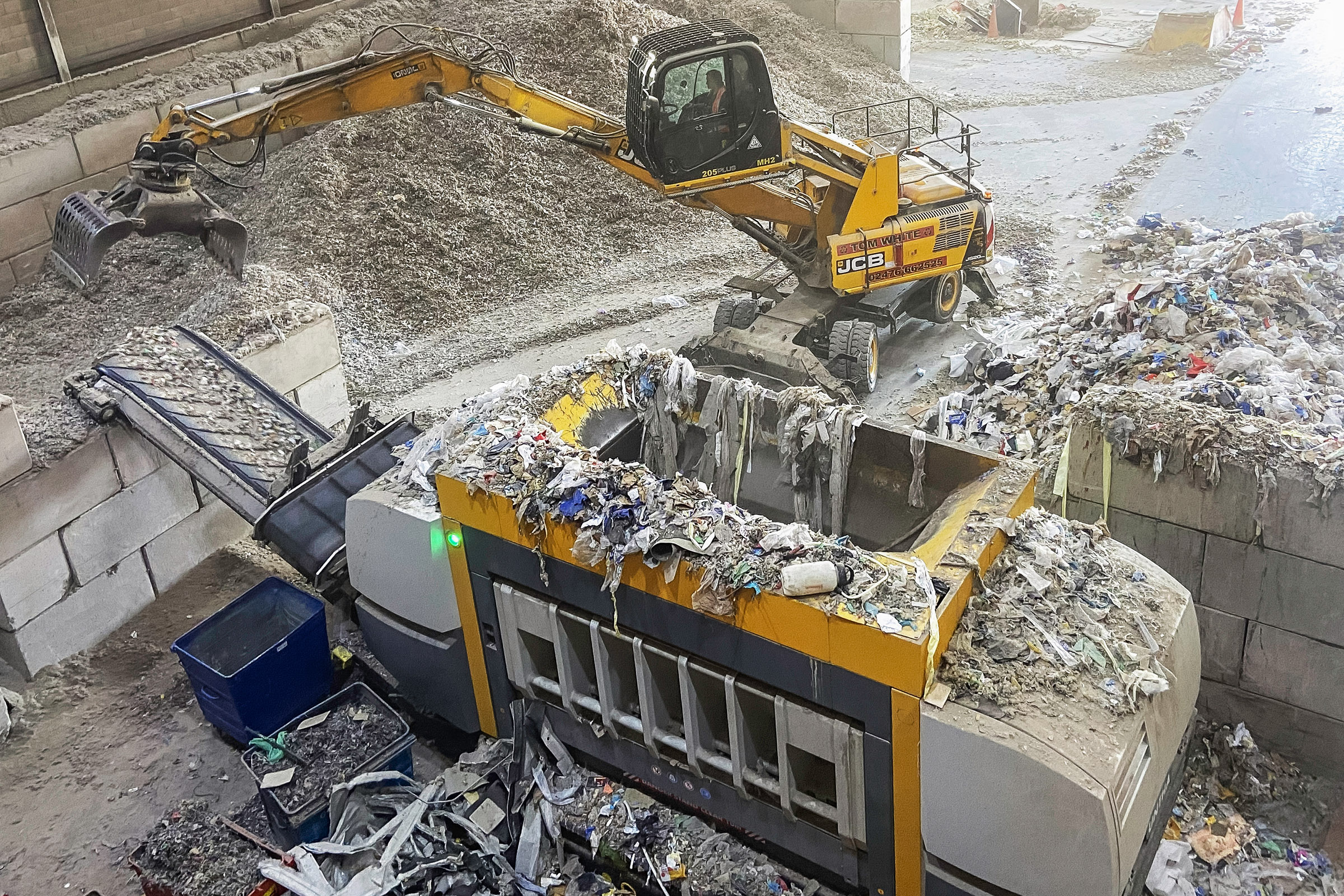
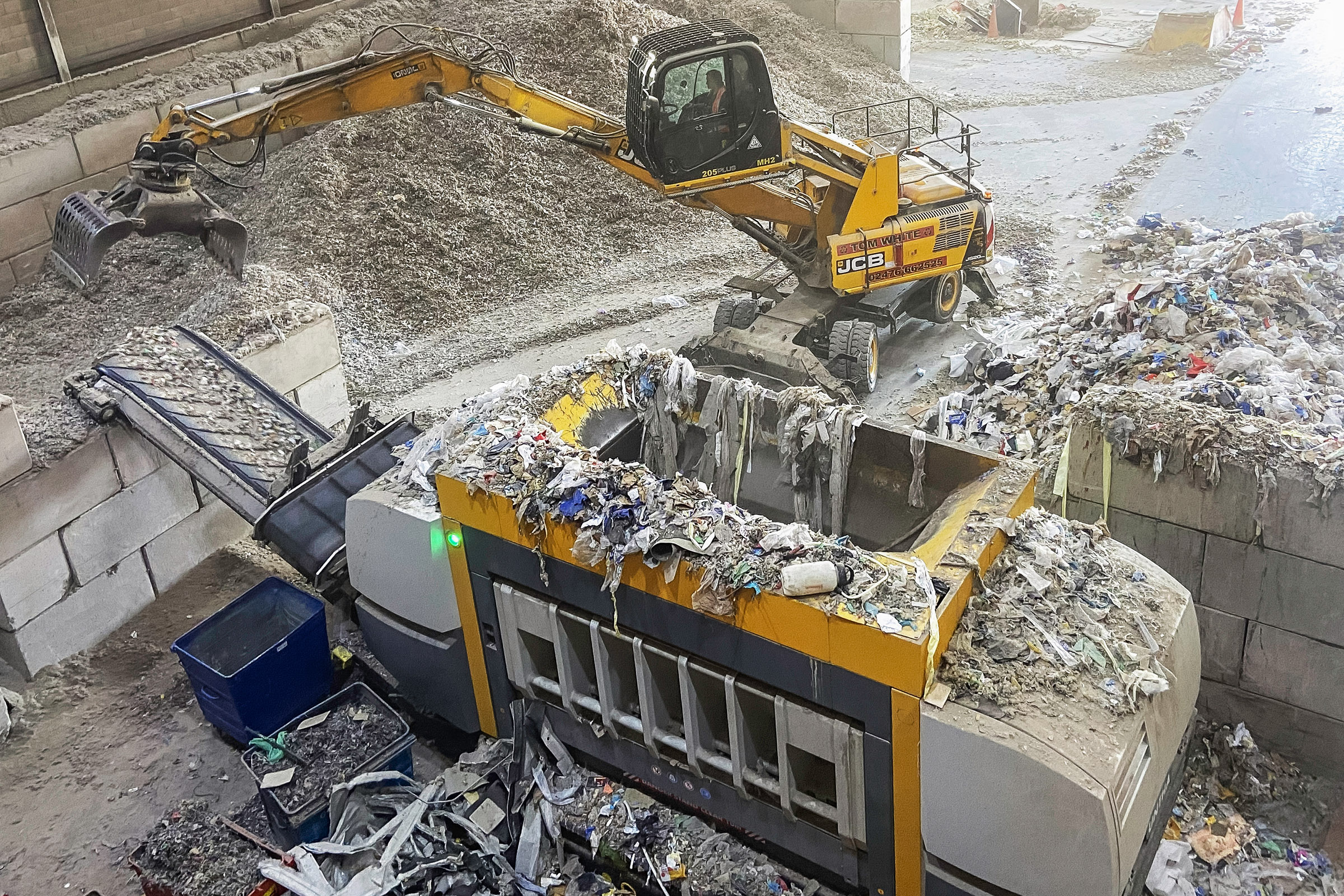
Incorporated in 1975, Coventry-based Tom White Waste has grown from a family-operated company to an established waste management expert, renowned for its changemaking approach to material recycling. Now owned by Coventry City Council, the firm specialises in ethical waste management that puts people first, protects the planet, and generates profit for purpose.
Through the use of its on-site materials recovery facilities (MRFs), Tom White can re-distribute recyclables back into the supply chain — including cardboard, plastics, wood, and both ferrous and non-ferrous metals, with the residual waste being leveraged for alternative fuel production.
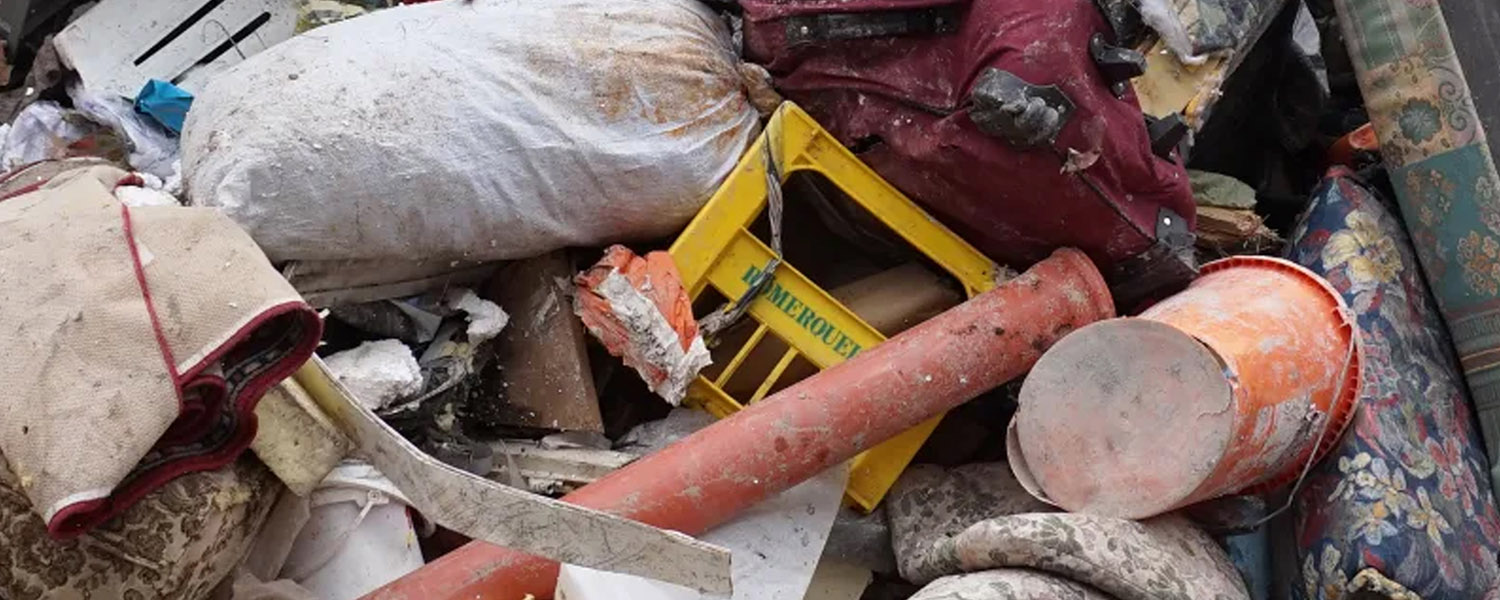
Approximately 180 tonnes of commercial, industrial, and demolition (C&I and C&D) waste pass through Tom White’s facility each day. After being shredded down to a 300mm particle size, heavy fractions and valuable commodities are extracted and segregated from the output. Previously, the remaining residual material was then transported to another waste management company. However, keen to reduce costs, and move one step closer to producing SRF on-site, the organisation sought the expertise of UNTHA UK.
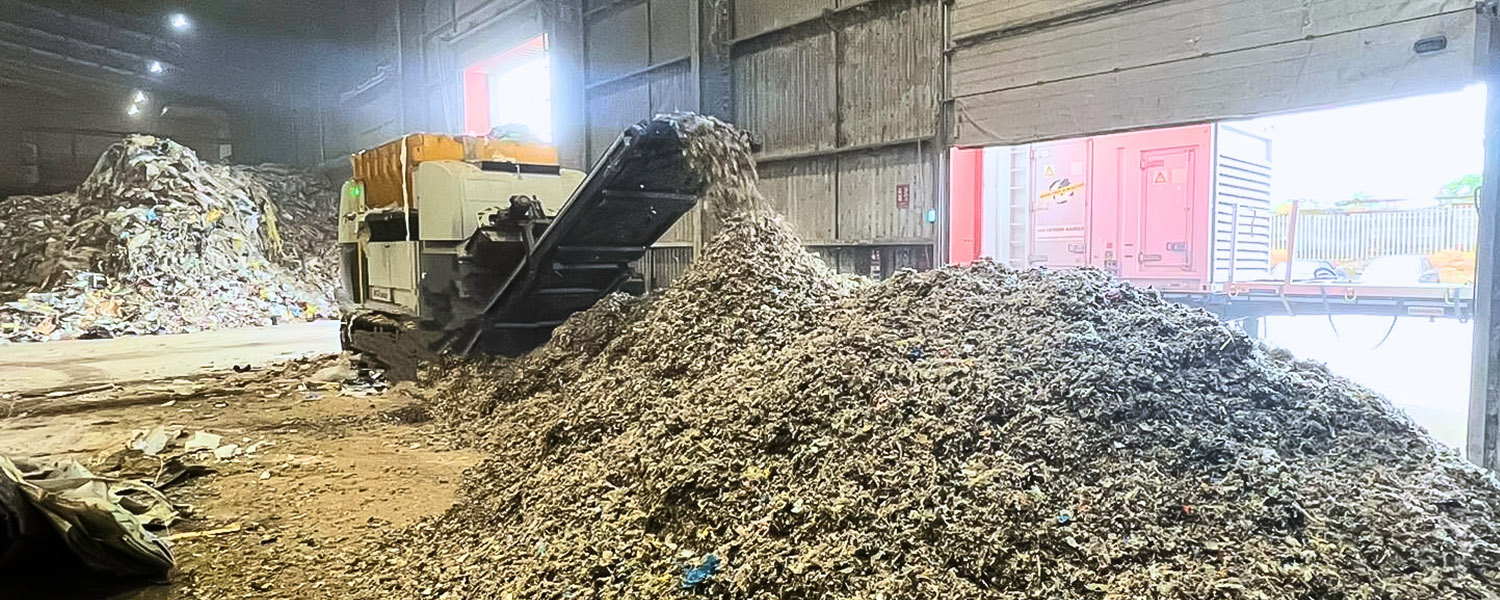
Tom White invested in the UNTHA XR3000C. The machine is 75% more energy efficient than diesel-hydraulic shredders, promises robust and reliable operation, and achieves a homogeneous shredding size of less than 50 mm — providing a high quality feedstock for solid recovered fuel (SRF).
Achieving throughputs of 60 tonnes per day – with capabilities of up to 80 on a single shift, the XR3000C is able to withstand the high volumes of waste facing Tom White’s materials recovery facility (MRF). In fact, the company is even able to take on processed material imported from other waste management specialists, to boost its bottom line and unlock ambitious growth. Bypassing the MRF, the material is mixed with the light residual fractions generated by the plant itself, enabling it to ultimately produce a greater volume of fossil fuel substitutes. The goal is to eventually move this process on-site.
Requirements
High throughput capability
Robust and durable material handling
On-specification SRF feedstock
Temporary mobile operation
Flexible financing options
From a cost perspective, the UNTHA Finance package was an attractive benefit for us too — and not just because we can budget accurately. We have wrapped a five-year service plan into our investment — including three site visits per annum, complete with full machine inspection and service, plus oil and filter change — for ultimate peace of mind.
Michael Trueman
Head of production at Tom White Waste
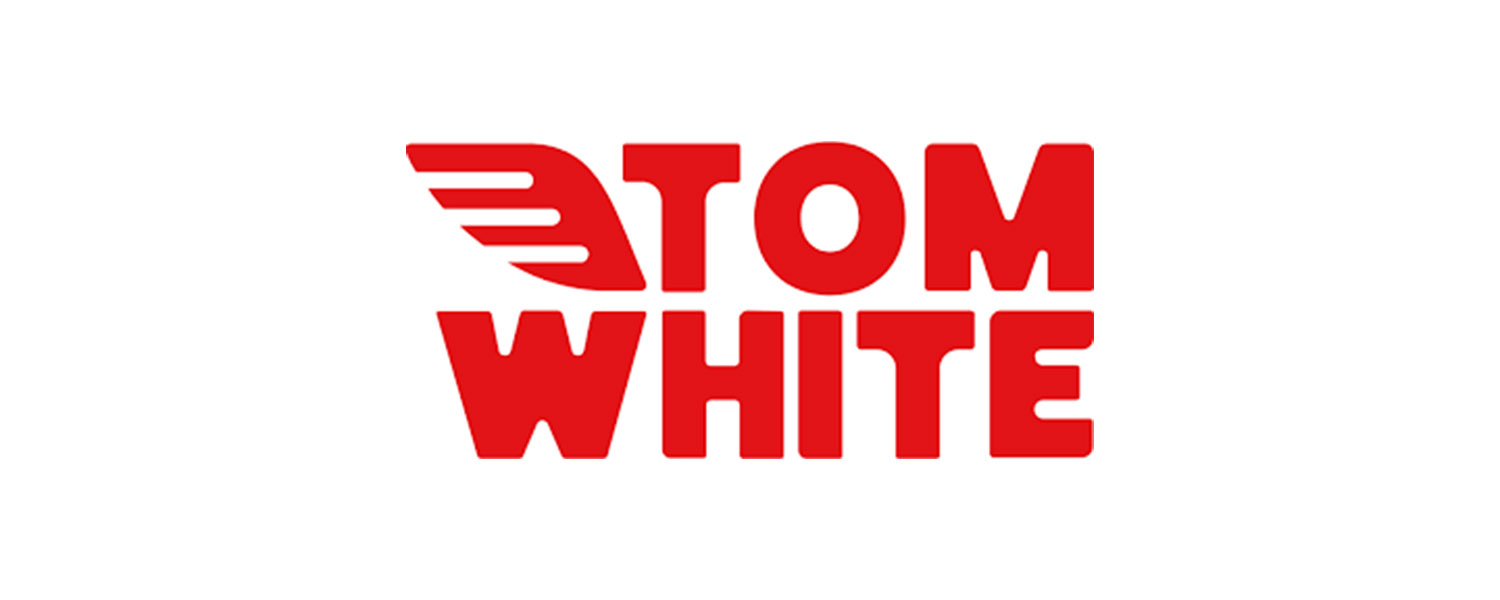