UNTHA 4-shaft technology
UNTHA shredding technology’s latest engineering feat hit the headlines in the Spring of 2024, when the Austrian-headquartered firm unveiled its advanced generation RS shredder series. The news marked the latest iteration of UNTHA’s globally acclaimed four shaft shredder range, which has continued to evolve since its original launch many decades ago. And the market has responded positively, with multiple RS orders placed by customers from numerous different countries, soon after the IFAT ‘reveal’.
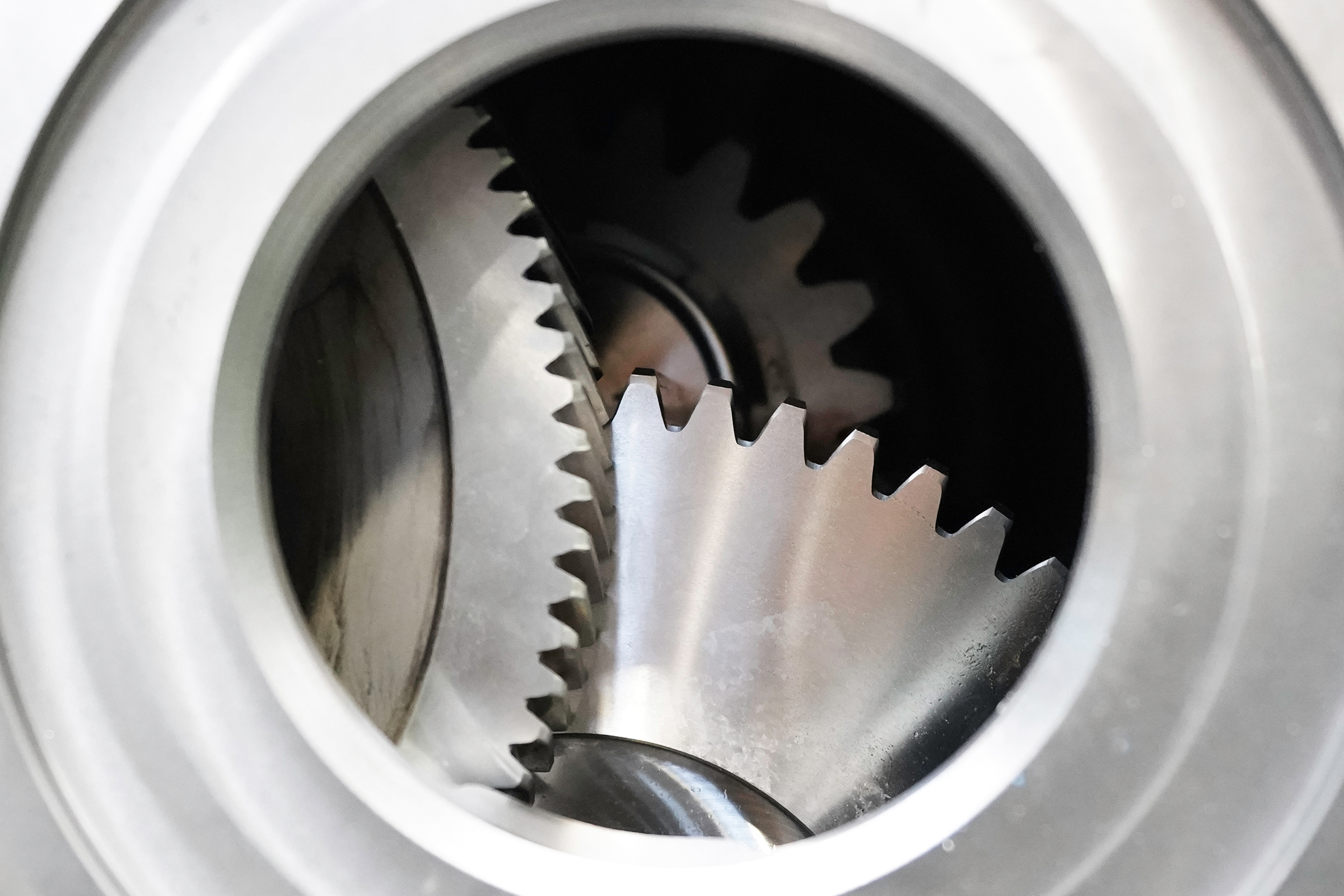
Here’s a quick recap on 10 of the progressive features and design adaptations that will further benefit global customers, moving forward:
Throughputs matter. That’s why small adaptations have been made to the screen body and cutting system symmetry, to reduce clogging and improve the shredder’s capacity.
Sometimes, the most advanced engineering considerations result in operational simplicity. That’s why the RS – with direct drive in all models – now features fewer wear parts for even easier and more cost-effective maintenance.
UNTHA shredders are renowned for their operational uptime, but that doesn’t mean ongoing improvements are not continually explored. UNTHA’s progressive R&D team has thought carefully about the integrated quick change screen system, to increase the speed of this operational process by 30%. That means even less time maintaining the machine, and more time shredding.
Ergonomic service and maintenance access further boosts uptime rates, as well as operator wellbeing. Careful consideration has also been deployed to ensure only non-specialist tooling is required.
Minimising unnecessary exposure to noise, is a big safety focus for UNTHA. Now, RS operators benefit from further improved working conditions, with noise levels now 8% lower – as quiet as 74dB(A).
While performance is of course the priority, UNTHA pays close attention to the aesthetic appeal of the shredders too. A bold new design – with custom hopper colours – makes for a striking appearance, but there’s more to this refresh than visual impact alone. For example, the LED strip light indicates the operational status of the shredder, at a glance – another simple feature introduced to help the customer.
The RS control panel has also had a UX refresh. The enhanced touchscreen display with redesigned interface and integrated machine hours counter, ensures easier error diagnosis and resolution. And did you know, the control system now achieves EN 13849-1 performance level d?
The ability to proactively monitor the condition of UNTHA’s shredding technology, has long been popular among customers of the XR and ZR waste shredders. But now UNTHA’s intuitive data-driven software solution – GENIUS – is available on the four-shaft RS shredders too.
Some customers have relatively straightforward requirements for our shredders, whereas others have more complex or aggressive applications. The RS is engineered for even ultra-heavy-duty waste and recycling streams, so can be supplied with a range of optional features, available in UNTHA’s new ‘tech pack’, if required. Think longer lasting mechanical seals to protect bearings, pre-tensioned cutting discs to enhance the shredder’s resilience against foreign objects, and shaft ventilation to reduce contamination. There are multiple design features available, which can be configured to suit customers’ individual shredding needs.
In truth there are dozens of small but mighty developments packed into the advanced generation RS – all engineered to deliver more strength, more versatility, more uptime, more efficiencies, and more potential for our customers, while controlling costs. But seeing is believing? If you’d like to understand what the RS series can really do, talk to us about your personal shred test.
Contact UNTHA using our contact form, to discuss your shredding needs in more detail – or why not request a demo?
There are currently more than 5,000 UNTHA RS shredders installed worldwide, handling a range of diverse and difficult materials including WEEE, confidential waste, production waste, metals, swarf, plastics, film, and more. These machines are used for size reduction, material liberation and homogenous particle sizing, to achieve optimal reuse, recycling, and recovery performance for customers. As a global group, UNTHA has sold more than 15,000 shredders in total.