Support the circular economy
The composition of materials is becoming more and more diverse. There is not just one type of plastic, instead, different plastics or plastic-metal composites are usually used. In order to recycle these sensibly, they must be processed accordingly. The RDG Recycling Group has set out to do just that: the Upper Austrian company uses innovative recycling processes to ensure that resources are conserved and CO2 emissions are reduced. The recycling process starts with an UNTHA shredder – a XR3000C mobil-e.
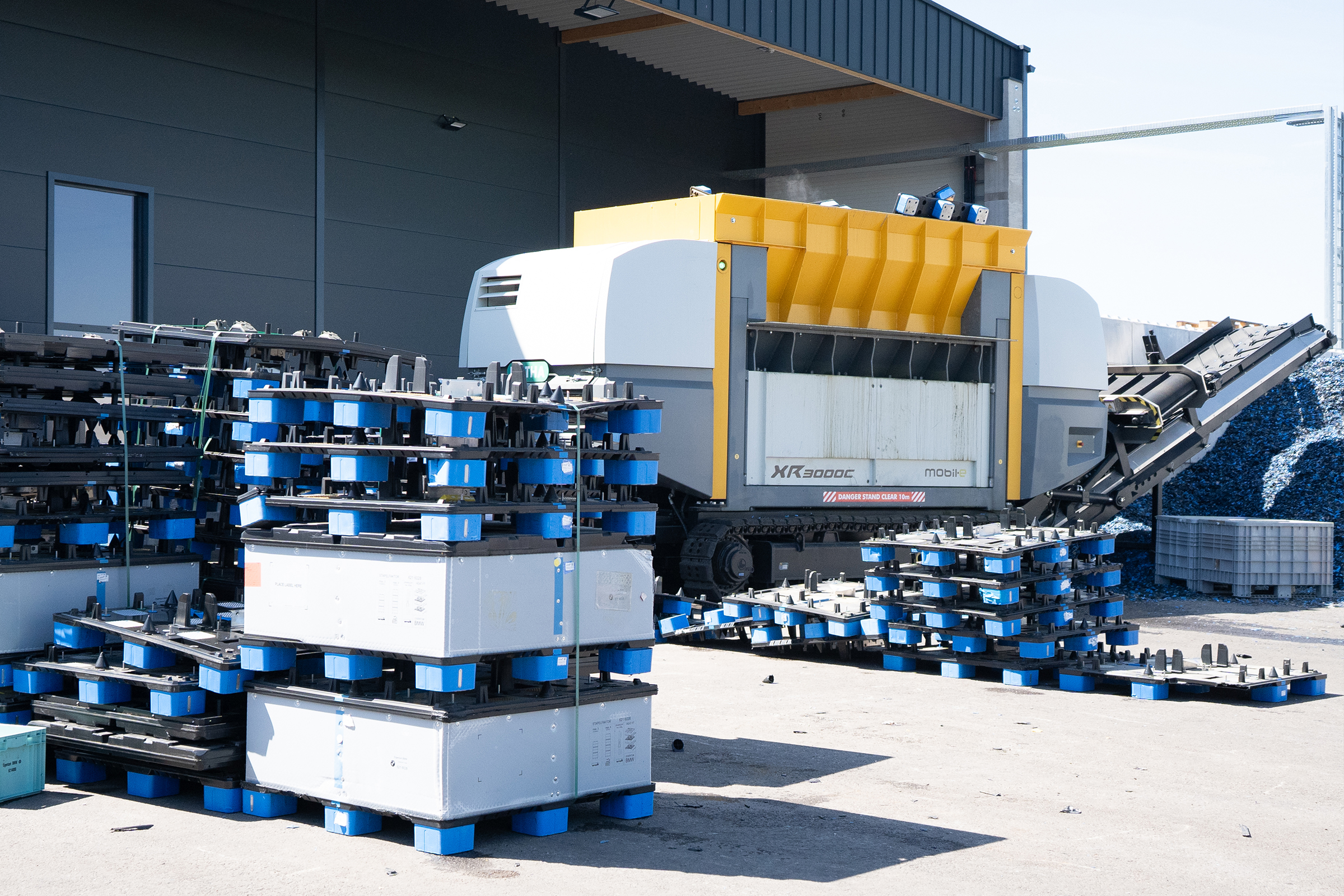
Over the past few years, the requirements for companies, recycling processes and the quality of recyclates have become increasingly differentiated. This has also changed the requirements profile for the technology needed for the individual process steps:
Many shredders are specialised for individual materials. However, if other or changing materials/material composites are to be processed, problems may arise. The RDG Recycling Group, based in Mühlheim am Inn/Austria, was therefore looking for a shredding solution that is suitable for different plastic (composites) and applications in order to be able to react flexibly to different material flows. The company's requirements for a shredder were therefore, among other things: a cutting system that is insensitive to metals/contaminants, an energy-efficient drive, loading by wheel loader/forklift truck and quickly replaceable perforated screens to achieve different shredding stages.
Various materials – new technologies
RDG Recycling Group processes plastics such as production waste, plastic-metal composites and large-volume post-consumer waste. The company produces around 16,000 tonnes of granulate every year, saving 32,000 tonnes of CO2 in the process.
For this purpose, RDG has been using an UNTHA XR3000C mobil-e to pre-shred plastics since 2024. The shredder is driven by the UNTHA Eco Power Drive: this energy-efficient direct drive, consisting of high-torque synchronous motors, ensures powerful shredding and is resistant to foreign objects. The shredder has a wide hopper that allows entire plastic pallets to be fed in by forklift or wheel loader. To ensure a constant material feed, the shredder was equipped with an internal ram that pushes the material to the cutting mechanism in a load-dependent manner. The C-cutting system ensures that the material is optimally pre-shredded. Depending on the requirements, the rotor can be equipped with up to four rows of blades. The blades can be used four times and then reprocessed. The 50 mm perforated screen ensures that 90 percent of the input material smaller than 40 mm leaves the shredder. Perforated screens can be quickly and easily replaced using the quick-change system. Depending on the material composition and the desired output size, the UNTHA XR3000C can shred up to five tonnes of material per hour. A magnetic separator above the discharge conveyor then removes any metal parts.
This is followed by sorting and grinding processes to achieve pure, homogeneous, fine-grained plastic granulate.
Franz Kobleder, shareholder and managing director of RDG Recycling Group, on the UNTHA shredder: ‘We needed a shredder that could handle plastic-metal composites and came across the UNTHA XR3000C mobil-e. This shredder has completely convinced us. It allows us to efficiently pre-shred our materials and thus prepare them for the subsequent process steps.’
User-friendly
The UNTHA shredder is extremely easy to maintain and service: most of the work can be carried out in an upright position and with standard tools. In addition, this XR3000C mobile-e was equipped with a central lubrication system that ensures that relevant points are automatically supplied with lubricant. If necessary, customers can also get support from the manufacturer's service team – either via remote maintenance or an on-site service call. This ensures that solutions are found quickly and downtime is minimised.
Material testing and live demonstrations
UNTHA offers its customers the opportunity to test the shredders intensively before making a purchase decision. To this end, the requirement profile is defined first: input material (size, composition, etc.), desired output size and planned throughput. Customers can test the shredder with their material under real conditions and see the performance for themselves. During the test run, UNTHA experts will be on hand to help the customer achieve the best possible result.
'UNTHA tested the shredding of our materials for us in advance. We then rented the XR3000C mobil-e for an extended period to be on the safe side and to test it extensively in operation. This shredder fulfils all the promises made by the UNTHA experts. We are completely convinced and would recommend this shredder based on our experience,’ says Franz Kobleder.
Images to download (may be reprinted for press purposes free of charge, picture credits: UNTHA shredding technology GmbH) https://untha.canto.de/b/IH5GN
Image 1: UNTHA XR3000C mobil-e shredding plastic-metal composites at RDG
Image 2: Franz Kobleder, shareholder and managing director of the RDG Recycling Group
Images 3+4: Homogeneous raw material: the 50-mm perforated screen ensures that 90% of the material is smaller than 40 mm