Relaunch of the UNTHA customer portal
UNTHA shredding technology GmbH is considered a pioneer in the field of digitalisation in the shredding industry and has been relying on smart services and predictive maintenance for years to ensure maximum efficiency and user convenience for its customers. The customer platform MyUNTHA and digital assistant GENIUS help to support customers in their daily work, optimise processes and further develop the shredders. UNTHA – the Austrian premium manufacturer of industrial shredding technology – promises even more useful apps and features with the extensive update of MyUNTHA, under the slogan ‘Make your business easier’.
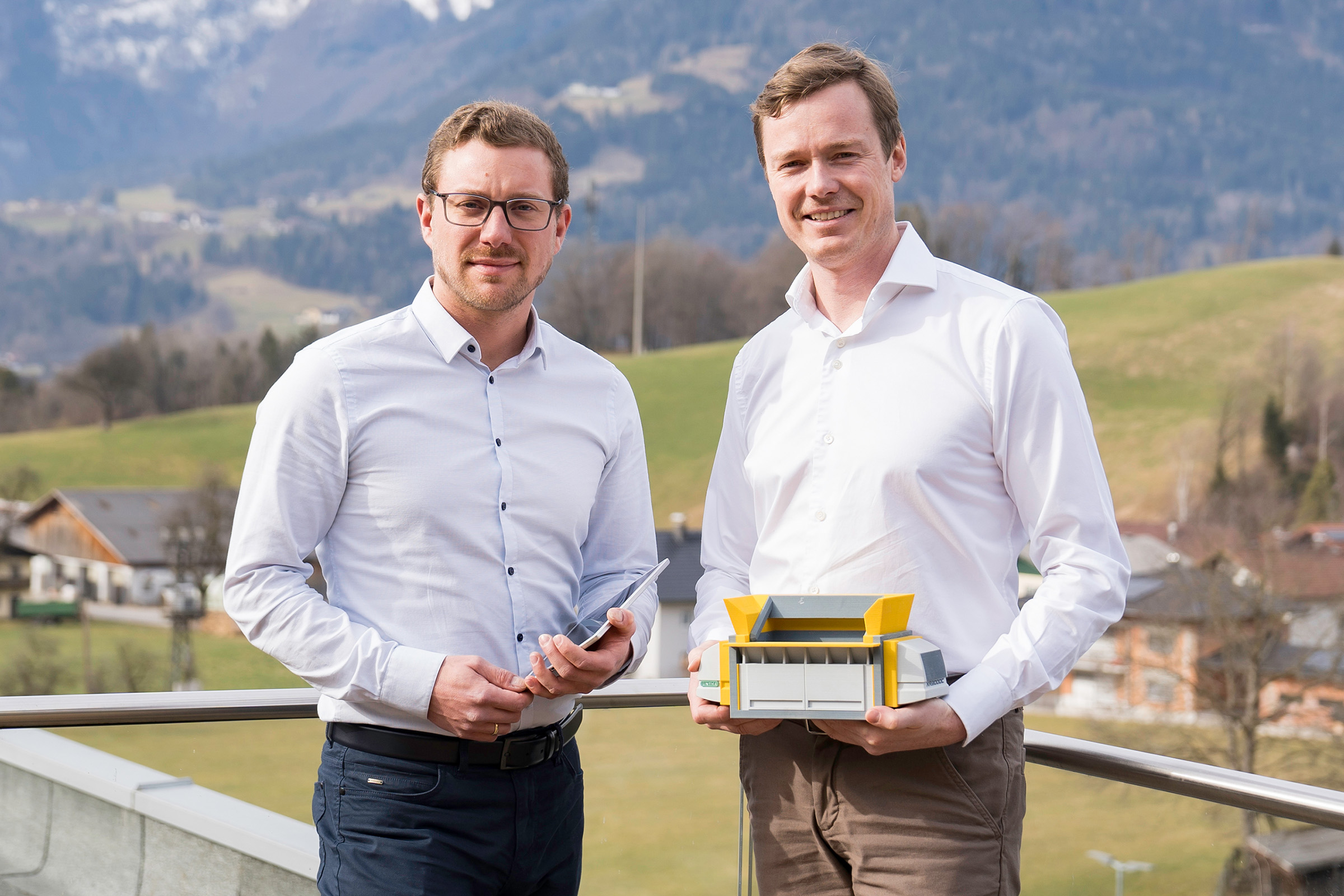
In addition to the further development of innovative technology, the company is constantly working on expanding its digital product portfolio: analysing and optimising processes in real time, planning maintenance work in advance, identifying spare parts online and ordering them quickly and easily – these are just some of the major advantages of the MyUNTHA customer platform.
‘For us, the sale of the shredder is not the end of the story. We focus on long-term customer relationships and, with our digital services and our service team, we ensure that we provide our customers with sustainable support and maintain the efficiency of their shredders over the long term – all in line with our motto ‘Make your business easier’,’ explain Markus Eibl and Stefan Irrnberger, the MyUNTHA project team. ‘MyUNTHA plays a central role in customer care and takes our services to a new level. This customer proximity and the direct feedback allow us to continuously develop our shredders and our (digital) services.’
MyUNTHA 2.0 – the update
The MyUNTHA customer platform is an important link between the customer and the shredding machine manufacturer. On MyUNTHA, customers can find all their individual data and information about their shredding solutions, access additional content and get in touch with the company's service team directly.
The platform update comes with three new or enhanced apps:
Spare parts catalogue & online shop: 3D models of the shredders enable customers to quickly and easily identify spare parts and order them directly online. This ensures that the relevant parts are delivered on time and that maintenance work can be carried out as planned.
Maintenance manager: Based on the continuously collected process data, necessary maintenance work (e.g. due to natural wear and tear) is calculated in advance. This means that such work can be planned and prepared for at an early stage. As a result, unexpected breakdowns are avoided and customers have sufficient time to pre-order necessary spare parts and schedule personnel.
GENIUS: The digital assistance system has also been further developed and will ensure even better data-based process evaluation in the future. With the help of this system, processes can be analysed and optimised during operation. This means that customers can keep an eye on their shredder at all times and make adjustments if necessary – for even greater productivity.
Users can rely on the fact that only they and the UNTHA service team have access to the stored data and that this data is used exclusively to optimise processes and for customer care. GENIUS has an integrated firewall to prevent unauthorised access. In addition, the connection to the cloud is designed as an encrypted end-to-end connection and the platform is hosted in Germany, thus guaranteeing maximum data protection. Access to the customer portal requires authentication from all users, so that only authorised persons have access.
Data-based process optimisation
With the help of reliable sensor technology in the shredder, process data is continuously collected. The intelligent assistance system GENIUS processes this data in real time and provides assistance to optimise the shredding process. The system also reacts immediately to malfunctions, such as the entry of foreign objects, and informs the operator – for example via SMS or e-mail. All this data and information is clearly displayed on the dashboard of the customer platform. This means that users always have the most important information at a glance. Historical data, such as repairs that have already been carried out, are also stored in the system and can be accessed at any time.
‘The UNTHA GENIUS assistance system automatically notifies our employees by email or text message as soon as the shredder can be reloaded. We can easily manage the notifications via MyUNTHA. This smart feature has become an integral part of our internal processes and helps us save time and money,' says Markus Quirchmair, Deputy Head of Raw Materials Handling at Laakirchen Papier AG.
Condition-based maintenance for even greater efficiency
MyUNTHA offers its users the greatest advantage through the interaction of the individual apps: for example, the maintenance manager's planning is based on GENIUS' calculations. The maintenance of the latest generation of shredders is based on AI-supported calculation models that analyse the condition of individual machine parts based on anomalies and natural wear processes and then predict when they will need to be serviced or replaced. This innovative method optimises efficiency and reduces maintenance costs and downtime.
‘The maintenance manager in MyUNTHA makes it much easier for us to plan and carry out maintenance. Thanks to the detailed instructions, we save a lot of time and can ensure that everything runs smoothly. What's more, the platform provides us with clean digital documentation that all approved users can access at any time,’ explains André Riemer, operations manager at Zuser Ressourcenmanagement GmbH.
One platform, many advantages
MyUNTHA is currently available for the new generation of the RS series and the well-established XR & ZR models. The service will be gradually extended to the entire UNTHA product range. Customers can add one or more shredders to the customer portal and use different apps and features depending on the model. All apps are embedded in the clearly laid out app store and can be activated with just a few clicks and then tested free of charge for three months.
All information about MyUNTHA 2.0 is available online at: www.untha.com/en/myuntha.
Images available to download (may be reprinted for press purposes free of charge, image credit: UNTHA shredding technology GmbH) https://untha.canto.de/b/U9TEI
Image 1: The MyUNTHA customer platform promotes productivity and user-friendliness
Image 2: The project team behind MyUNTHA: (from left to right) Markus Eibl, Product Manager for Digital Products & Services, and Stefan Irrnberger, Head of After Sales Service
Image 3: The interaction of the individual MyUNTHA apps optimises processes